Varnish is a type of coating commonly seen in daily life, and it may be that shiny protective layer we see on wood or artwork. The reason why I say “maybe” is that some paints have a very similar appearance to varnish. When we analyze the internal composition and working principle, you can be sure whether it is varnish or not.
What is Varnish Paint?
Varnish is a clear, hard and durable coating. It is an organic coating formed by a combination of natural or synthetic resins, oils and solvents. It is applied thinly to the surface and dries to form a tough, transparent film. It is usually used to protect the surface and enhance its appearance. Unlike paint, varnish does not contain pigments or colors. Its function is to protect the surface and give it a beautiful high gloss or satin effect.
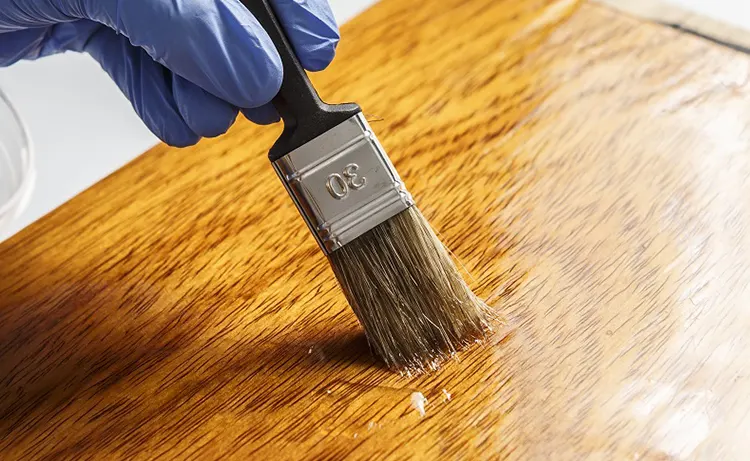
What is Varnish Paint
The history of varnish paint dates back centuries and is one of the oldest in the coatings category. It is believed that the ancient Egyptians and ancient Chinese (Tang Dynasty) civilizations used egg whites, natural resins and oils to make varnish to protect paintings. With the advancement of human civilization, varnishes have continued to develop, and many synthetic Varnish Paints have been developed by adding various chemical ingredients to improve durability and ease of use. By the 17th century, varnish had become an important assistant in the woodworking and painting art industries, and artists and craftsmen used it to protect and enhance their works. Today, varnish is still widely used for furniture finishing, art protection and various industrial applications.
To really understand what varnish is, it is important to know what varnish is made of. The composition of varnish is usually composed of 4 main components: resin, oil, solvent and additives.
Resin is the main component of varnish. Early varnishes were natural resin solutions extracted from plant secretions, including dammar, copal and rosin. It is made by heating the resin, adding natural oils such as linseed oil, cooking the mixture to the desired viscosity, and then diluting it with turpentine.
Today, natural varnishes have been largely replaced by varnishes made from synthetic resins. Most modern varnishes are a blend of resin, drying oil, drier, and volatile solvent. Among them, there are mainly alkyd resin, polyurethane resin, phenolic resin, vinyl resin and epoxy resin. The choice of resin affects the durability, finish, and drying time of the varnish.
Oil (usually linseed oil or tung oil) helps to enhance the flexibility of varnish paint, making it less likely to crack over time. The addition of oil also helps to apply the varnish smoothly and evenly.
Solvents are used to dilute varnishes, making them easier to apply and drying faster. As the varnish dries, its solvent portion evaporates and the remaining components oxidize or polymerize to form a durable, clear film. Common solvents include turpentine, mineral spirits, and even water (water-based varnish paint).
Additives are optional ingredients. The varnish can be formulated according to its specific properties, such as UV resistance, resistance to yellowing or faster drying times.
The differences and proportions of the ingredients in varnish paint directly determine the gloss, protection, flexibility, and durability of the coating.
Varnish has been able to develop to this day in the long river of history, and it must have irreplaceable advantages. From a modern and objective point of view, the correct use of varnish can indeed gain many advantages. For example:
- Waterproof: It can protect the surface from rain in the daily life environment.
- Protect: Varnish can prevent scratches and abrasions on the tabletop (any wood). Also protects artwork from dust, dirt.
- Enhance beauty: Enhance the natural grain and texture of the material, providing a consistent gloss, satin or matte effect.
- Environmental protection: Low VOC water-based varnish and natural varnish are conducive to the development of green ecology.
How Does Varnish Work?
The function of varnish is to coat and cure the surface of the material into a hard, transparent layer. When we paint, spray or roll varnish onto a surface, the resin in the varnish sticks to the surface of the substrate. The resin component acts like glue and forms a strong bond between the substrate surface and the varnish.
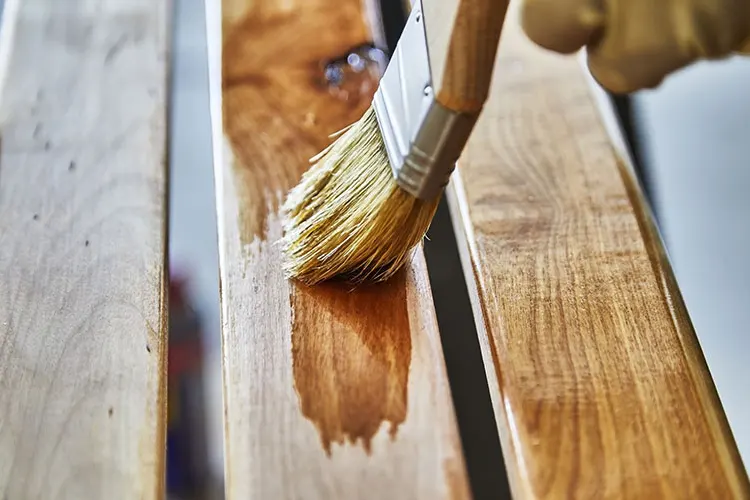
The role of varnish
During the application of varnish and after painting is complete, solvents begin to evaporate. During the evaporation process, the remaining resin and oil begin to harden, and the varnish solidifies from a viscous liquid into a solid coating. Over time, the resin in the varnish hardens to form a tough, transparent film. This film provides the above-mentioned protection against moisture, dirt and scratches.
When applying varnish over primer or undercoats, the varnish is combined with the primer. The primer or undercoat provides a smooth, stable surface for the varnish, so the entire protective coating can last longer. Without a primer, the varnish is more likely to peel or chip over time. Click to learn more tips on maintaining and extending Varnish Paint.
In either case, maintaining a clean, smooth substrate surface is always an important prerequisite for determining the effectiveness of varnish curing. The specific varnish coating steps can be read in detail in our corresponding blog.
What Are The Types of Varnish Paint?
Varnish Paint has evolved and developed into many different types through the long history of development. Before actual application, it is necessary to choose the right type of varnish based on the needs of the project. From a macro perspective, there are two main categories of Varnish Paint: natural varnish and synthetic varnish.
- Natural varnish: Made from natural oils and resins, such as resins (frankincense resin and dammar resin), fossil resins (copal), and insect excrement (shellac) or linseed oil. These types of varnishes have been used for hundreds of years and provide a classic, beautiful, and rich finish. But it takes longer to dry and requires more maintenance over time.
- Synthetic varnish:In contrast, synthetic varnishes made from modern formulas use chemicals and synthetic resins to make them more durable and have faster drying times. Supports high-volume production in modern industrial environments and can be chemically tailored with great precision for specific applications. For example, the molecular structure of the resin can be manipulated to change its viscosity and hardness, improve the solubility of varnish ingredients in water or other substances, and the ability to successfully mix with various additives.
In addition to the two main categories of natural and synthetic varnishes, there are many types of varnishes. Different varnish formulation ingredients can be targeted to provide unique advantages to the substrate surface. Here are a few of the most commonly encountered types of varnishes on the market:
Quick Comparison of Varnish Types | |||||
---|---|---|---|---|---|
Varnish Type | Key Ingredients | Durability | Best For | Finish | Drying Time |
Oil-Based Varnish | Natural oils (linseed, tung oil), resins (alkyds) + solvents | High | Wood furniture, trim, floors, exterior surfaces | Glossy, Warm | Slow |
Acrylic & Water-Based Varnish | Acrylic resins + water-based solvents | Medium to High | Furniture, indoor wood, art projects | Matte, Satin, Glossy | Fast |
Polyurethane Varnish | Polyurethane resins (isocyanates + polyols) + solvents or water | Very High | High-traffic floors, kitchen counters, outdoor furniture | Glossy, Satin | Medium |
Nitrocellulose Varnish | Nitrocellulose + plasticizers | Medium | Musical instruments, automotive, high-quality finishes | Glossy | Very Fast |
Resin-Based Varnish | Varies by resin type (Epoxy, Alkyd, Phenolic, Polyurethane, Vinyl) | High to Very High | Marine, industrial, automotive, outdoor furniture | Glossy, Hard | Slow |
Oil-based varnish:
Traditional oil-based varnish is made from natural oils such as linseed oil or tung oil mixed with resins. It provides a rich, warm finish that enhances the natural grain of the wood, making it a top choice for furniture and cabinets. While oil-based varnish is known for its durability and glossy effect, it takes longer to dry and produces a strong odor due to the large amount of solvents in its composition, requiring proper ventilation when applied.
Acrylic and water-based varnish:
This type of Varnish Paint uses water or acrylic as the primary solvent, making it a very eco-friendly option. They dry much faster than oil-based varnishes and have less smell (which is key when we advocate). These varnishes are often used on interior projects such as wood floors, furniture, and art to provide a clean finish that is easy to maintain. However, water-based varnishes do not deepen the appearance of wood as well as oil-based varnishes, and are not wear-resistant.
Polyurethane Varnish:
Polyurethane Varnish is the strongest representative of the synthetic Varnish Paints. It’s made from a synthetic polymer that creates a hard, durable surface that’s resistant to moisture, heat, and scratches. Available in both water-based and oil-based formulas, polyurethane varnish is ideal for high-traffic areas such as wood floors or kitchen countertops where strong protection against scuffs is needed.
Nitrocellulose Varnish:
Nitrocellulose Varnish Paint is known for its ultra-fast drying time and is often used to refinish wooden musical instruments or automotive surfaces. While it can be applied quickly, it is not as durable as resin varnishes and tends to crack or chip over time.
Resin-based Varnish:
Resin-based Varnish Paint is made from synthetic resins such as epoxy, alkyd, phenolic, polyurethane or vinyl. These resins give the varnish a hard, glossy surface and add durability. Each resin-based varnish type has specific advantages:
- Epoxy Varnish Paint consists of epoxy resin (usually derived from bisphenol A and epichlorohydrin) combined with an amine hardener or curing agent. These ingredients give the varnish excellent adhesion, water resistance and chemical stability.
- Alkyd Varnish Paint is produced by reacting polyols (such as glycerin) with fatty acids (such as linseed oil or soybean oil) and dicarboxylic acids (such as phthalic acid). This combination gives alkyd varnish great flexibility and a beautiful glossy finish.
- Phenolic varnishes are made from phenol (an alcohol) mixed with formaldehyde in the presence of a catalyst. This varnish is highly resistant to heat, chemicals and weathering and is often used in industrial applications where resistance to extreme conditions is critical.
- Polyurethane Resin The polyurethane resin in varnishes is synthesized by reacting an isocyanate (such as TDI or MDI) with a polyol (such as glycerin or propylene glycol). The resin can be modified with solvents or water to produce an oil-based or water-based product. Offers excellent toughness, chemical resistance and scratch resistance.
- Vinyl resin varnishes are made from vinyl resin, which is polymerized from a vinyl compound such as vinyl chloride or vinyl acetate and mixed with plasticizers and stabilizers. Vinyl resin varnish has excellent flexibility, moisture resistance and good corrosion protection.
Breakdown of Resin-Based Varnishes | ||||
---|---|---|---|---|
Type of Resin-Based Varnish | Key Ingredients | Durability | Best For | Features |
Epoxy Resin Varnish | Epoxy resins (bisphenol-A and epichlorohydrin) + hardeners (amines) | Very High | Boats, Outdoor equipment, Industrial surfaces | Excellent chemical resistance, superior adhesion, water resistance |
Alkyd Resin Varnish | Polyols (glycerol), fatty acids (linseed oil), dicarboxylic acids | High | Indoor/outdoor furniture, Cabinets, Wood trim | Glossy finish, great flexibility, indoor and outdoor use |
Phenolic Resin Varnish | Phenol + formaldehyde | Very High | Industrial machinery, Heat-resistant surfaces | Heat-resistant, chemical-resistant, ideal for tough environments |
Polyurethane Resin Varnish | Polyurethane resins (isocyanates + polyols) | Very High | Floors, Kitchen counters, High-wear surfaces | Scratch-resistant, versatile, high durability |
Vinyl Resin Varnish | Vinyl resins (vinyl chloride + plasticizers) | High | Automotive, Industrial, Exterior furniture | Flexible, resistant to moisture, weather, and chemicals |
Knowing the various types of varnish and their ideal uses will help you choose the right Varnish Paint for your next painting project. For more considerations and price analysis on purchasing varnish, please visit our related blog for in-depth information.
In short, as a highly decorative and durable coating, Varnish Paint is definitely worth buying. I believe that through the professional explanation above, you have already got a clear direction on the type of varnish you need. Are you ready? Easily find varnish suppliers and even on-site varnish application services with coatingsdirectory.com. If you have any questions or unique experiences worth sharing, please leave a message in the comment section below and let’s talk together.
FAQs
Is varnish the same as Polyurethane?
Varnishes and polyurethanes are different. Polyurethanes are a synthetic resin of water-based or oil-based plastic resins that offer greater durability and abrasion resistance. Varnishes are older in development and are made from a mixture of resins, oils, and solvents.
What is varnish called now?
Varnish IS a catchall term, basically any film building finish, although its formulations have evolved. Modern varnish names are more specific, such as “polyurethane varnish” or “acrylic varnish.” These new names reflect the added materials or techniques used to enhance the varnish’s performance.
The difference between oil-based varnish and nitrocellulose varnish.
Oil-based varnishes are more durable, dry slowly, and provide a rich, deep finish. Nitrocellulose varnishes, on the other hand, dry faster, are thinner, and are often used in applications such as musical instruments or furniture that require a quicker turnaround time. The two meet different needs.