Coatings have become a common substance in life, used to protect the surface of objects and increase their beauty. To make it easier to distinguish, professional coatings industry practitioners usually divide them into conversion and non-conversion types. We have already introduced the knowledge in the field of conversion coatings in detail in another blog. Now we have specially written this article to help you understand what non-conversion coatings are. Explore the expertise of Thermoplastic coatings, Volatile coatings, Hot Melt Coatings, and Non-aqueous dispersion coatings in non-conversion coatings and compare them to conversion coatings. Let’s get started!
What is Non-Conversion Coating?
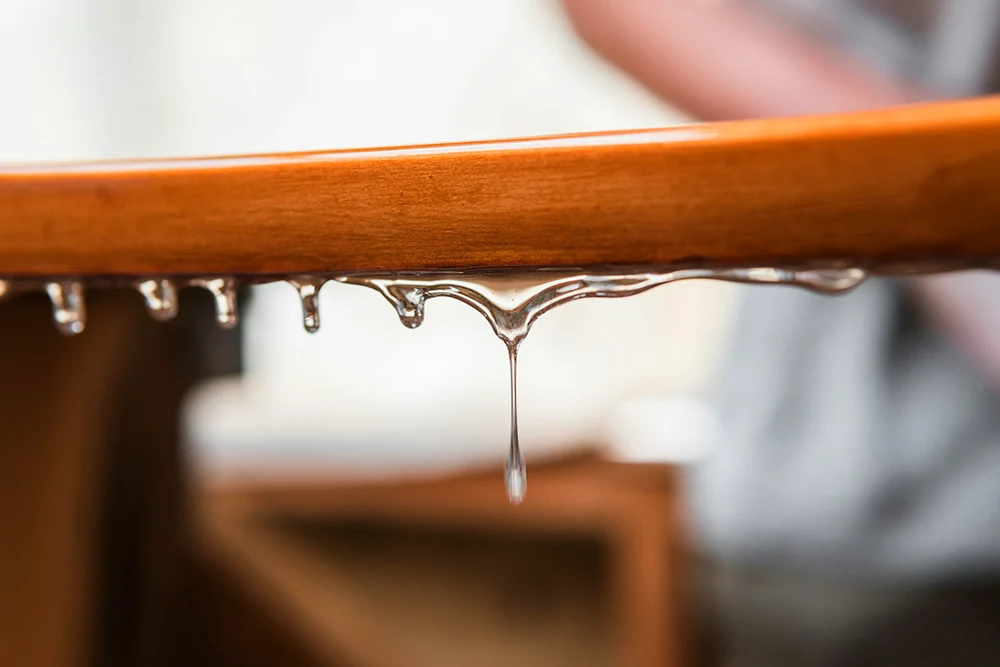
Non-Conversion Coating Alkyd Coatings
Non-conversion coatings are types of coatings that form a protective or decorative film solely through physical changes, without undergoing any chemical transformations during the curing process. Unlike conversion coatings, which rely on complex chemical reactions to create a cross-linked, solid film, non-conversion coatings maintain their chemical structure from the liquid to the solid state. This might sound a bit mundane, but non-conversion coatings are essential in many industries due to their unique properties and ease of application.
The Science Behind Non-Conversion Coatings
Non-conversion coatings typically contain a high percentage of organic materials, such as resins, pigments, and additives, dispersed in a solvent or water. When applied to a surface, the solvent evaporates, leaving behind a continuous film. This evaporation process is purely physical, involving no chemical reactions. The resulting film adheres to the substrate, providing a layer of protection and enhancing the appearance of the material.
The beauty of non-conversion coatings lies in their simplicity. Because they do not rely on chemical curing, they can be formulated to dry quickly at room temperature, making them highly convenient for a variety of applications. These coatings are available in many forms, including paints, varnishes, lacquers, and enamels, each tailored to meet specific needs and preferences.
Advantages | Disadvantages |
---|---|
Ease of Application: Can be applied with simple tools like brushes, rollers, or spray guns. | Lower Durability: Typically less durable than conversion coatings. |
Quick Drying: Dries quickly at room temperature, reducing downtime. | Limited Chemical Resistance: Less resistant to chemicals and harsh environments. |
Versatility: Available in various forms and finishes to suit different needs. | Potential for Solvent Emission: Some formulations may release volatile organic compounds (VOCs) during application and drying. |
Cost-Effective: Generally more affordable than conversion coatings. | Maintenance: May require more frequent reapplication or maintenance compared to conversion coatings. |
User-Friendly: Requires no special curing equipment or complex processes. | Adhesion Issues: May not adhere as well to some substrates compared to chemically bonded coatings. |
Non-conversion coatings are used extensively in numerous industries due to their versatility and ease of use. In the automotive industry, for instance, they are employed as topcoats to provide a glossy finish and protect vehicles from environmental damage. In the construction sector, these coatings are used on surfaces like wood, metal, and concrete to enhance durability and aesthetics. Additionally, non-conversion coatings are popular in the furniture and consumer goods industries, where they provide attractive finishes and protect against wear and tear.
What Are the Types of Non Conversion Coating?
Non-conversion coatings form a protective or decorative film purely through physical changes, without any chemical reactions during the curing process. This simple process makes non-conversion coatings invaluable in many industries due to their ease of application and versatility. Let’s explore the main types of non-conversion coatings and their specific applications.
Volatile coatings
Volatile coatings dry through the evaporation of solvents and form a solid film. These coatings are easy to apply and dry quickly, making them ideal for a variety of applications.Types of Volatile Coatings:
- Solvent-based coatings: These coatings use organic solvents and are known for their durability and gloss. They are often used on exterior surfaces due to their weather resistance.
- Water-based coatings: These coatings utilize water as a solvent and are environmentally friendly, fast-drying, and emit fewer volatile organic compounds (VOCs), making them suitable for interior applications.
Thermoplastic coatings
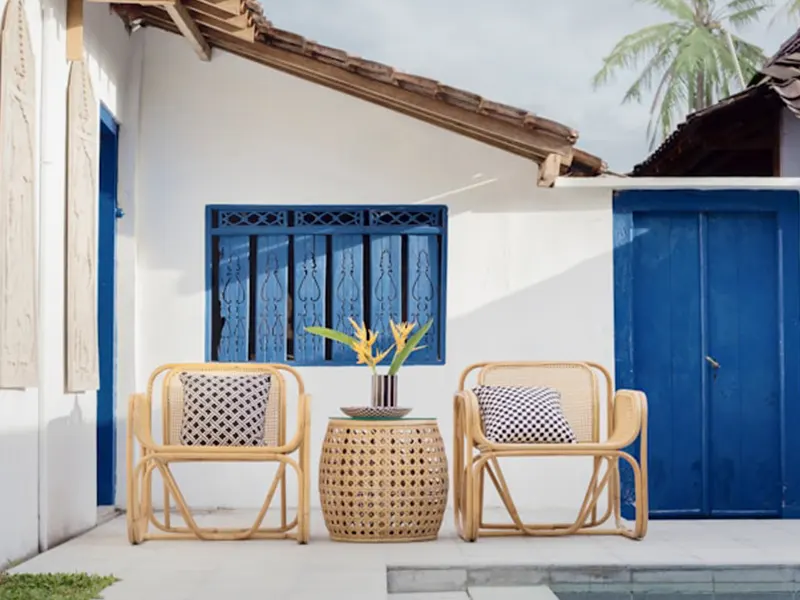
Preparing for construction Thermoplastic coatings
Thermoplastic coatings form a film through a physical drying or melting process without any chemical cross-linking. These coatings can be re-melted and reapplied, offering flexibility and reusability. Types of Thermoplastic Coatings:
- Acrylic coatings: These coatings offer excellent UV resistance and flexibility. They are often used on exterior surfaces, including walls and roofs.
- Vinyl coatings: Vinyl coatings are known for their durability and water resistance and are often used on floors, walls, and various industrial surfaces.
- Polyvinyl chloride (PVC) coatings: These coatings have high chemical resistance and can be used in environments exposed to harsh chemicals and conditions.
- Thermoplastic powder coatings: Thermoplastic powder coatings need to be heated above the melting temperature to allow the resin particles to fuse to form a continuous, unbroken coating film. Film formation at this point depends on the melt flow temperature, melt viscosity, and melt surface tension. Of course, powder coatings are hot melts in addition to being thermoplastic.
Hot Melt Coatings
Hot melt coatings are applied in a molten state and solidify after cooling. These coatings are solvent-free and provide a strong, durable surface. Types of Hot Melt Coatings:
- Polyurethane Hot Melt Coatings: These coatings have excellent adhesion and durability. They are widely used in bonding and finishing applications in the automotive and furniture industries.
- Ethylene Vinyl Acetate (EVA) Hot Melt Coatings: EVA coatings are known for their flexibility and strong adhesion and are often used in packaging, textiles, and woodworking.
Hot Melt powder coatings for cars
Non-aqueous dispersion coatings
Non-aqueous dispersion coatings consist of finely dispersed polymer particles in an organic solvent. These coatings provide uniform films with good mechanical properties. Types of non-aqueous dispersion coatings:
- Nitrocellulose lacquers: These lacquers dry quickly and have a high gloss finish, making them popular in the automotive and furniture industries.
- Alkyd enamels: These solvent-based enamels offer excellent adhesion and durability. They are used on metal surfaces, machinery, and industrial equipment.
Non-conversion coatings play a vital role in many industries, providing a practical solution for surface protection and enhancement. While they may not offer the same durability as conversion coatings, their ease of application, quick drying time, and cost-effectiveness make them a valuable option in many cases. By understanding the different types and their specific applications, professionals can make an informed decision to achieve optimal performance and durability. Whether for aesthetic or protective purposes, non-conversion coatings remain indispensable in various fields.
Conversion Coating VS Non Conversion Coating.
Both conversion coatings and non-conversion coatings have unique properties, advantages, and limitations that make them suitable for different environments and uses. Understanding the differences between conversion coatings and non-conversion coatings is essential to choosing the right type of coating for a specific application. We have made a detailed comparison of conversion coatings and non-conversion coatings from the following 6 aspects to fully analyze their differences.
- Definition and Formation Process
Conversion coatings form a protective layer on the surface of the substrate through chemical reactions to form a metal surface or change the resin molecules. Provide corrosion resistance, adhesion, and other desirable properties. Common types include chromate, phosphate, and oxide coatings. These coatings involve complex chemical processes that form cross-linked solid films.
On the other hand, non-conversion coatings rely on physical changes to form protective or decorative films. These coatings maintain their chemical structure during the process from liquid to solid without undergoing chemical transformation. They include paints, varnishes, lacquers, and enamels. Film formation is usually achieved by solvent evaporation or drying. - Chemical Resistance and Durability
Conversion coatings are known for their excellent chemical resistance and durability. The chemical reactions during their formation process form a strong and tightly bonded coating that can withstand harsh environments. This makes them ideal for industrial applications where corrosion protection and long-term durability are critical.
While non-conversion coatings provide a protective barrier, their chemical resistance and durability are generally lower than conversion coatings. They are more susceptible to abrasion, chemical exposure, and environmental factors. However, modern formulation advances have significantly improved their performance, making them suitable for less demanding, specialized environments. - Application Methods and Equipment
The application of conversion coatings generally requires specialized equipment and controlled conditions. The application process for these coatings involves large equipment such as dipping, spraying, or electroplating, and then precise control of temperature, time, and chemical concentration to ensure optimal results. This often involves more complexity and cost.
Non-conversion coatings are easier to apply using simple tools such as brushes, rollers, or spray guns. They do not require complex equipment or rigorous conditions, making them more suitable for a wide range of applications. This simplicity is one of their main advantages, especially for DIY projects and small-scale applications. - Environmental Impact and Safety
Many traditional conversion coatings, especially chromate-based coatings, pose significant risks to the environment and health due to the toxic chemicals involved. The industry has been moving toward greener alternatives, but the impact on the environment remains a concern. Proper handling, disposal, and regulatory compliance are critical.
Non-conversion coatings, especially water-based ones, are generally more environmentally friendly. They emit fewer volatile organic compounds (VOCs) and present fewer health risks during use. Developments in green chemistry have further improved their environmental friendliness, making them a safer choice for interior and residential applications. - Cost and Maintenance
Conversion coatings can be more expensive to apply due to the need for specialized equipment and a controlled process. However, their superior durability often means lower maintenance costs over time. They are a cost-effective option for applications where longevity and minimal maintenance are critical.
Non-conversion coatings are generally less expensive due to the simplicity of the process and the availability of materials. However, they may require more frequent maintenance and reapplication, which can increase long-term costs. Their lower initial cost makes them attractive for budget-conscious projects. - Aesthetic and Functional Properties
Although primarily functional, conversion coatings can also provide aesthetic benefits. For example, phosphate coatings can provide a pleasing matte finish, and anodized coatings come in a variety of colors. However, their primary purpose is protection and adhesion, not decoration.
Non-conversion coatings excel in providing aesthetic enhancements. They are available in a wide variety of colors, finishes, and textures, allowing for a great deal of customization. Whether you require a glossy, matte, or textured finish, non-conversion coatings offer a variety of options to meet decorative requirements.
Factor | Conversion Coatings | Non-Conversion Coatings |
---|---|---|
Definition and Formation | Formed through chemical reactions converting the surface into a protective compound. | Formed through physical changes without chemical transformations. |
Chemical Resistance | Excellent chemical resistance and durability due to strong chemical bonds. | Lower chemical resistance and durability, improved by advanced formulations. |
Application Methods | Requires specialized equipment and controlled conditions (dipping, spraying, electroplating). | Easy to apply with simple tools (brushes, rollers, spray guns). |
Environmental Impact | Can be environmentally hazardous, especially chromate-based coatings; requires careful handling and disposal. | Generally more environmentally friendly, especially water-based options. |
Cost and Maintenance | Higher initial cost due to complex processes, but lower maintenance over time. | Lower initial cost and easier application, but may require more frequent maintenance. |
Aesthetic Properties | Primarily functional with some aesthetic options (matte, anodized colors). | Wide range of colors, finishes, and textures for decorative purposes. |
In summary, the choice between conversion and non-conversion coatings depends on the specific requirements of the project. Conversion coatings are the preferred choice for industrial applications that require superior durability, chemical resistance, and long-term protection. They involve complex chemical processes and specialized application methods, but offer unmatched performance in harsh environments. Non-conversion coatings, while less rugged, are easy to apply, affordable, and available in a wide range of aesthetic options. They are suitable for residential, commercial, and light industrial applications where environmental impact, safety, and cost are important considerations.
Understanding these differences will help you make an informed decision, ensuring you select the right coating to meet your project’s needs, balancing performance, cost, and environmental considerations.
To wrap up, both conversion and non-conversion coatings have unique advantages and applications. Choosing the right coating depends on your specific needs and industry requirements. This guide has provided you with essential insights to make an informed decision. For further assistance, visit coatingsdirectory.com to explore our extensive database of coating suppliers, local service providers, and industrial Non-Conversion service companies, ensuring you find the perfect solution for your projects.
How Long Do Conversion Coatings Last?
The longevity of conversion coatings depends on several factors, including the type of coating, the environment it’s exposed to, and the quality of application. Typically, these coatings can last several years, providing long-term protection against corrosion and wear. Proper maintenance can extend their lifespan even further, making them a durable choice for many applications.
Are Non-Conversion Coatings Suitable for High-Temperature Environments?
Non-conversion coatings can be used in high-temperature environments, but they might not offer the same level of protection as conversion coatings. Conversion coatings are specifically designed to enhance the durability and heat resistance of metal surfaces, making them a better choice for applications involving extreme temperatures.
How Can I Maintain and Extend the Life of Coated Surfaces?
Maintaining and extending the life of coated surfaces involves regular cleaning and inspection. Avoid using harsh chemicals that can damage the coating and ensure that any chips or damage are promptly repaired. Applying a sealant or protective wax can also help in preserving the coating’s integrity. Regular maintenance routines can significantly enhance the durability and effectiveness of conversion coatings.