Article Chapters
Imagine gliding like a skilled dancer, applying coatings smoothly with precision and deftness. Welcome to the world of roller coating, where innovation and efficiency combine to create a seamless painting experience. In this blog post, we take a journey to uncover the secrets of roller coating. Revealing what roller coating is, from surface preparation to thickness control, and solutions to common problems during the roller coating process. Whether you’re a seasoned pro or just beginning your paint application journey, get ready to discover valuable insights and techniques to improve your roller coating skills.
What Is Roller Coating and How Does It Work?
Roller coating, also known as roller coating or roll coating, is a versatile method for applying liquid paint to a variety of substrates. Unlike other coating methods that rely on spraying or dipping, roller coating utilizes a series of rollers to evenly distribute paint onto the substrate surface.
The roller coating process uses one or more rollers to apply coatings such as adhesives, paints, coatings, and varnishes or clear topcoats to a flat substrate. These rollers are usually made of materials such as rubber or stainless steel and transfer the coating material to the substrate as it passes through the machine. and ensures excellent adhesion between coating and substrate for a durable and long-lasting finish. This makes it suitable for a wide range of applications, from furniture and flooring to automotive and aerospace components.
- Roller coating excels in both efficiency and quality, making it the first choice for applying coatings to flat objects. Roller coating helps reduce production costs and environmental impact by eliminating overspray and minimizing material waste.
- An additional advantage of roller coating is the ability to achieve precise and uniform coating thickness quickly. The speed and pressure of the roller can be carefully controlled to ensure consistent coverage of the entire surface of the substrate. The amount and viscosity of the coating liquid deposited on the substrate can be precisely controlled by metering rollers. The farther the metering roller is from the applicator roller, the thicker the coating, and the closer the metering roller is to the applicator roller, the thinner the coating. This makes it ideal for applications requiring precise coating thickness.
Whether applying a thin protective layer or a thick decorative coating, roller coating can easily accommodate a variety of coating thicknesses. Whether enhancing the visual characteristics of a part or protecting it from environmental damage, roller coating is one of the most effective methods of applying coatings to flat substrates.
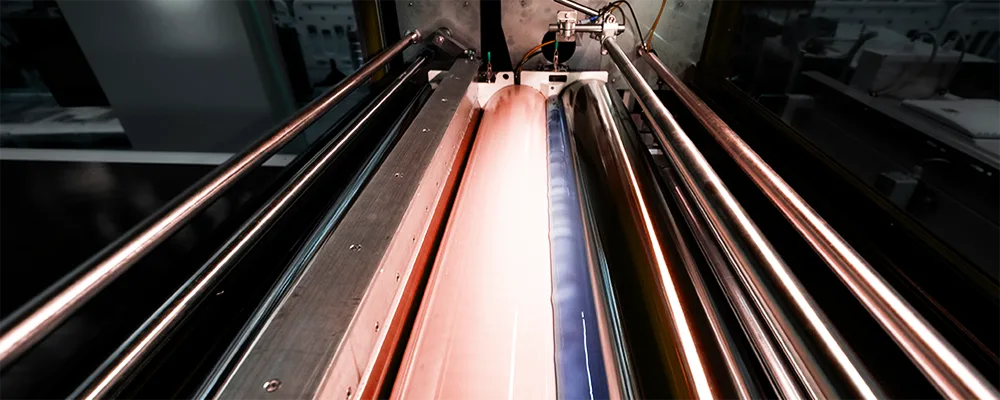
What is roller coating technology
Characteristics and applications of roller coating | ||
---|---|---|
Advantages | Limitations | Application Industries |
Precise and uniform coating thickness; Excellent control over coating thickness; High efficiency with minimal material waste; Reduced overspray and environmental impact; Superior adhesion and durability; Versatility in coating various substrates; | Limited suitability for complex shapes; May require multiple passes for thick coatings; Not suitable for high-volume production; Requires careful setup and maintenance; | Furniture manufacturing; Flooring; Automotive components; Aerospace components; Electronics; Construction materials; Packaging; Textiles; Paper and printing; Renewable energy components; Marine; Renewable energy; Medical devices; Coatings and paints; Adhesives and sealants; And more; |
In summary, roller coating is a versatile and effective method of applying liquid paint to a substrate. Its precise control, uniform coverage and ability to accommodate a wide range of coating thicknesses make it a valuable asset in industries where quality and efficiency are critical. So the next time you’re in awe of a perfectly coated product, remember the magic of roller coating – the silent hero behind the scenes that ensures a smooth, great coating.
Surface Preparation for Roller Coating.
You’re getting ready to implement the roll coating process, but before you get started, there’s one important step – surface preparation. Having a clean surface is the foundation of any successful painting, and roller coating is no exception. Proper surface preparation ensures optimal adhesion between the paint and the substrate during roller coating, resulting in a long-lasting coating.
Without adequate surface preparation, the coating may not adhere properly, causing issues such as peeling, flaking, or uneven coverage. By investing time and effort in surface preparation, you can avoid costly rework and achieve superior coating quality.
Here are some practical tips for surface preparation based on our past experience to ensure your journey to a perfect coating goes smoothly and successfully:
- Cleanliness is Key:Before applying any coating, ensure the substrate surface is clean and free from contaminants such as dirt, oil, grease, and rust. Cleaning methods may include solvent wiping, degreasing, or abrasive blasting, depending on the substrate material and the level of contamination.
- Surface Profiling: To enhance adhesion, consider profiling the substrate surface to create a rough texture. This can be achieved through methods such as sanding, abrasive blasting, or chemical etching, depending on the substrate material and coating requirements.
- Moisture Management:Moisture can interfere with coating adhesion and performance. Ensure the substrate surface is dry and free from moisture before applying the coating. Use moisture meters or moisture-resistant coatings if necessary to prevent moisture-related issues.
- Equipment inspection:The cleanliness and stability of the roller coating equipment determines whether the roller coating goes smoothly. So be sure to check the roller coater for debris and residue from the last roller application before you begin. Timely cleaning and regular maintenance of the Roller coating machine is very important. You can go to our corresponding blog to learn how to properly maintain the Roller coating machine.
- Primer Application:In some cases, applying a primer before roller coating can further enhance adhesion and corrosion resistance. Choose a primer compatible with both the substrate and the coating material, and follow manufacturer recommendations for application and curing.
- Quality Control:Regularly inspect the substrate surface before and during the roller coating process to ensure it meets the required cleanliness and profile standards. Address any surface defects or contamination promptly to prevent coating failures.
In summary, surface preparation is a critical step in achieving a successful roll coating application. By following these guidelines and investing in proper surface preparation techniques, you can ensure optimal adhesion, durability and performance of your coated products. So before you embark on your roller coating adventure, remember: preparation for perfection is the key to successful roll coater painting!
How to Apply Roller Coating?
Roller coating, also known as roll application or roll coating. Roller coating involves the application of liquid paint using a series of rollers, each with a specific purpose in the coating process. The process begins by dispensing coating material onto a series of rotating rollers (either immersed in a coating fluid or introduced through separate die nozzles), carrying a thin film on the surface of the rollers. The film is then transferred to the substrate as the roller rotates. This is a precise, efficient method for applying paint to a variety of substrates. Below, let us reveal the secrets to achieving a high-quality, smooth, and even coating to suit your project needs.
- Surface Preparation: Thoroughly clean and prepare the substrate surface before applying the coating. Remove any dirt, grease or contaminants that may affect the quality of the coating. Make sure the substrate surface is clean, dry and free of any contaminants. Proper surface preparation is essential to achieve good adhesion and even coating coverage.
- Coating material selection:Select a coating material that is compatible with the substrate and application requirements. When selecting a coating material, consider factors such as viscosity, drying time, and desired finish.
- Adjust roll speed and pressure:Correctly adjusting roll speed and pressure is critical to achieving uniform coating thickness. Properly adjust the speed and pressure of the roller in the roller coating equipment to achieve the desired coating thickness. Experiment with different settings to find the best combination for your specific coating project.
- Control coating thickness:Use precision metering rollers to control coating thickness. Adjust the roller coating equipment structure (gap between rollers, die nozzle pressure, etc.) to achieve the required coating thickness to ensure even coverage of the entire substrate surface.
- Keep your drum clean:Regularly clean and maintain your drum to prevent the buildup of dry coating material that can affect coating quality and consistency. Proper roller maintenance is critical to obtaining a smooth, even coating.
In conclusion, mastering the art of roller coating requires attention to detail, precision, and a deep understanding of the coating process. By following these tips and techniques, you can achieve high-quality, smooth, and uniform coatings that meet the highest standards of quality and performance. So, whether you’re coating furniture, automotive parts, or electronic components, remember these roller coating secrets to unlock the full potential of your coating project.
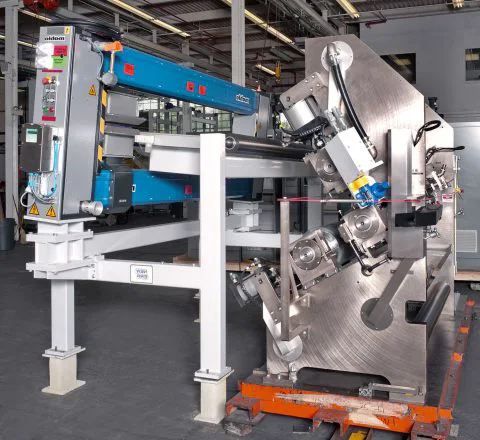
Reverse roller coating machine in operation
How to Control Roller Coating Thickness?
As we all know, roller coating provides a method of accurately and efficiently applying coatings to a variety of substrates. But how do you ensure the coating thickness is just right? Understanding the factors that affect thickness and methods for precise control is critical. Let’s uncover the secrets to controlling roller coating thickness and achieving perfection in every application.
Just like learning mathematics, let us analyze it step by step from the surface to the deep. Before learning to control roller coating thickness, let us understand the factors that affect coating thickness. They include:
- Roller speed:Adjusting the roll speed plays a vital role in controlling coating thickness. Higher roller speeds generally produce thinner coatings, while slower speeds produce thicker coatings. It’s like adjusting the tempo of a song to create the perfect beat.
- Roller Pressure:The pressure the roller exerts on the substrate affects the amount of coating transfer. By fine-tuning the roller pressure, the operator can precisely achieve the desired thickness. This is similar to adjusting the pressure when painting a beautiful masterpiece.
- Paint viscosity:Anyone who knows anything knows that the viscosity of a paint material affects its fluidity and coverage. Therefore, the viscosity of the coating material also affects the coating thickness. Higher viscosity paints produce thicker layers, while lower viscosity paints produce thinner layers. Finding application balance is crucial.
- Substrate Properties:Surface properties of the substrate, such as roughness or porosity, can affect coating thickness. Smoother substrates tend to produce thinner coatings, while rougher substrates may require adjustment to obtain an even thickness.
- Speed of paint delivery pump:Some roller coaters have independent paint delivery pumps, such as slot die coater and lip coater. The speed of the paint delivery pump determines the amount of paint applied per unit time, which directly affects the coating thickness.
- Substrate assembly line speed: The speed of the substrate assembly line affects the residence time of the substrate in the coating zone, thereby affecting the coating thickness. The faster the transfer speed, the thinner the coating thickness. vice versa. Give appropriate dwell time for perfect transfer and adhesion of paint.
- Coating gap: In blade-type roller coating equipment,the final roller has a knife to remove excess paint. Therefore, the distance between the applicator and the substrate affects the amount of coating material applied and directly affects the coating thickness.
We have taken a detailed look at the factors that influence roller coating thickness. The next step is to learn how to control the coating thickness.
- Precise roller adjustment:Modern roller coaters are equipped with advanced controls that allow operators to precisely adjust roller speed, pressure and other parameters. By taking advantage of these features, operators can achieve consistent and accurate coating thickness.
- Online thickness measurement:Using an online thickness measurement system, the coating thickness can be monitored in real time during the application process. This proactive approach allows for immediate adjustments to ensure uniformity and accuracy.
- Metering blades or rollers:Using roller coating equipment with metering blades or metering rollers helps regulate the amount of coating material applied to the substrate, ensuring precise thickness control. Click to learn more about the types of roller coating equipment and important accessories.
- Transfer from another roller:Coating thickness can also be controlled by increasing the number of rollers and the direction of transfer to transfer the coating from another roller to the substrate. Adjust the gap between the rollers to achieve the desired thickness.
- Quality Assurance Inspections:Regular quality assurance inspections, such as regularly sampling and testing coating samples, can help verify coating thickness and determine if it deviates from specifications. It’s like double-checking your work to make sure it’s perfect every time.
By understanding these factors and mastering methods of controlling roller coating thickness, roller coating service providers can achieve unparalleled roller coating thickness accuracy, ensuring high-quality results in a variety of applications. So the next time you admire a perfectly coated product, remember the meticulous craftsmanship that goes on behind the scenes – a symphony of precision and control orchestrated by masterful roller coating techniques.
Common Problems and Solutions During the Roller Coating Process.
Embarking on the roller coating journey can feel like riding a roller coaster—full of twists, turns, and unexpected challenges. But fear not, fellow adventurers! In this blog post, we’ll be your guides, equipping you with the knowledge to navigate the ups and downs of the roller coating process. From roller coatings to reverse roll coating, ceramic roller coating, and clear coat roller, we’ll explore the common problems encountered along the way and provide practical solutions to keep your coating process on track.
Common problems and countermeasures for roller coating | ||
---|---|---|
Problem | Cause | Solution |
Uneven Coating Thickness | Uneven roller pressure or speed | Adjust roller pressure and speed for uniform coating |
Orange Peel Effect | Incorrect viscosity of coating material | Dilute or adjust viscosity for smoother application |
Air Bubbles | Entrapment of air during application | Degassing coating material before application |
Streaking or Smearing | Contaminated or worn rollers | Clean or replace rollers regularly |
Poor Adhesion | Ensure proper surface preparation and curing process | Degassing coating material before application |
Wrinkling or Crinkling | Excessive coating thickness or improper drying | Control coating thickness and ensure proper drying conditions |
Fish Eyes | Contamination by silicone or other foreign particles | Use clean materials and avoid silicone contamination |
Pinholing | Incomplete wetting of substrate or air entrapment | Improve substrate surface preparation and coating application |
Edge Build-Up | Excessive coating accumulation at substrate edges | Adjust roller settings or use edge guards to prevent build-up |
Color Variation | Inconsistent application or coating material | Maintain consistent application parameters and material quality |
Roller Marking | Defective or improperly maintained rollers | Inspect and maintain rollers regularly to prevent marking |
Drips and Runs | Excessive coating material or improper application | Control coating volume and application technique |
As we reach the end of our roller coaster ride through the world of roller coating, remember that every twist and turn is an opportunity to learn and improve. By understanding the common problems and solutions outlined in this post, you’ll be better equipped to tackle any challenges that arise during the roller coating process. So, strap in, hold on tight, and enjoy the ride as you master the art of roller coating like a seasoned pro!
Innovation and Future Trends in Roller Coating.
In the fast-paced world of manufacturing and coatings applications, staying ahead of the curve is critical. Today, we take a deep dive into the world of roller coating, where innovation and future trends are coming together to redefine the way paint is applied.
As industries continue to push the boundaries of performance and efficiency, roller coating is at the forefront of innovation. From advances in coating formulations to the development of precision roller coating equipment, the field of roller coating is developing rapidly. Let’s explore the innovative technology of roller coating together.
- Advanced Coating Formulations:Innovations in roller coating are driving the development of advanced coating formulations tailored to specific applications. From eco-friendly and sustainable coatings to high-performance formulations with enhanced durability, roller coaters are embracing new materials to meet evolving market demands.
- Precision Roller Coating Equipment: The future of roller coating lies in precision and efficiency. Manufacturers are investing in cutting-edge roll coaters equipped with advanced automation, precision control systems, and predictive maintenance capabilities. These innovations not only streamline the coating process but also ensure consistent and high-quality results, ultimately improving productivity and reducing downtime.
- Customized roller coating equipment:The issue of roller coating of large substrates has been hotly discussed in the industry this year. In many cases roller coating of large substrates requires large equipment and extensive changeover work. In recent years, roller coating equipment developers and manufacturers have adopted box rollers in some roller coating equipment to make it easier to change coating conditions.
- Digitalization and Industry 4.0 Integration:In line with the broader industry trends towards digitalization and Industry 4.0, roller coating systems are undergoing a digital transformation. Integration with data analytics, machine learning, and IoT (Internet of Things) technologies enables real-time monitoring, optimization, and predictive maintenance of roller coaters, leading to increased efficiency, reduced waste, and enhanced quality control.
We have already gained a certain understanding of the innovation of roller coating through the above content. To truly understand the trajectory of roller coating, we must explore the emerging trends that are poised to revolutionize the industry. Customization, sustainability, and integration with additive manufacturing are just a few of the key themes driving innovation in roller coating. By embracing these trends, industrial roller coating service providers and manufacturers can unlock new possibilities and drive roller coating into the future.
- Customization and Flexibility:As consumer preferences continue to evolve, the future of roller coating will prioritize customization and flexibility. Manufacturers will seek versatile roller coaters capable of handling a diverse range of substrates, coating materials, and application techniques, allowing for greater customization and adaptability to changing market needs.
- Sustainability and Environmental Responsibility:In response to growing environmental concerns, the future of roller coating will focus on sustainability and eco-friendliness. Innovations in water-based coatings, solvent-free formulations, and recyclable materials will drive the development of roller coating systems that minimize environmental impact while delivering superior performance and quality.
- Integration with Additive Manufacturing:With the rise of additive manufacturing (3D printing), the future of roller coating will see increased integration with additive processes. Roller coaters will play a crucial role in post-processing and surface finishing of additively manufactured parts, offering opportunities for enhanced surface properties, aesthetics, and functionality.
All in all, the future of roller coating is characterized by innovation, efficiency and sustainability. As technology continues to evolve and market demands change, roller coaters will play a key role in shaping the future of coating applications across industries. By focusing on the latest advances and future trends, we can realize the full potential of roller coating technology and pave the way for a brighter, more efficient future. Join us on a journey to discover the latest advances and emerging trends that promise to shape the future of roller coating technology. If you have any new insights into roller coating technology, please leave a message below.
As we conclude our exploration of roller coating, we hope you’ve gained a deeper understanding of this versatile process. From mastering surface preparation to overcoming common challenges, roller coating offers endless possibilities for achieving superior coatings. Remember, the journey doesn’t end here. Explore our platform, coatingsdirectory.com, to connect with leading roller coating service providers and equipment manufacturers. With our extensive directory and search functionality, you’re empowered to find the perfect solution for your coating needs. Here’s to smoother surfaces and endless possibilities in the world of roller coating!
What type of roller for skim coating?
Choosing the right skimmer roller is crucial to getting smooth, even results. Usually choose high-quality microfiber or lambswool rollers with short pile (Drywall compound rollers are the best recommendation). These rollers are designed to evenly set and release skim coating material for an even finish without leaving fibers or lint behind. Avoid using foam rollers as they may create bubbles and uneven texture on the surface.
How do you know if your roller coating is too thick?
Determining the thickness of your roller coating is crucial to ensure proper adhesion and drying time. One way to gauge if the coating is too thick is by observing the application process. If the roller leaves behind noticeable streaks or ridges, it may indicate that the coating is too thick. Additionally, excessive dripping or sagging of the coating material can be a sign of over-application. To remedy this, adjust the roller pressure and speed to achieve a smoother and more consistent coating thickness.
Do i need to wash paint roller between coats?
Yes, it’s essential to wash your paint roller between coats to maintain the quality of your finish and prolong the life of your roller. Cleaning the roller removes any dried or excess paint that could affect the next coat’s application. Simply rinse the roller thoroughly with warm water until the water runs clear, then gently squeeze out any remaining paint. For oil-based paints, use mineral spirits or paint thinner for cleaning. Allow the roller to dry completely before reusing it for the next coat.
How do I keep my paint roller from drying out between coats?
To prevent your paint roller from drying out between coats, follow these simple tips:
- Wrap the roller tightly in plastic wrap or aluminum foil to seal out air and moisture.
- Place the wrapped roller in a plastic bag and seal it to maintain moisture.
- Store the roller in a cool, dry place away from direct sunlight to prevent premature drying.
- If you’re taking a break between coats, you can also immerse the roller in a bucket of water or paint solvent to keep it moist until you’re ready to resume painting.
By following these practices, you can ensure that your paint roller stays in optimal condition and ready for use whenever you need it.