Article Chapters
Are you ready to enter the world of dip coating equipment? Imagine a machine coating a delicious dish with chocolate like a chef, only this time, it’s not a dessert, but your product is perfectly protected or enhanced. This is the magic of dip coating systems! Dip coaters play a vital role in applying uniform coatings to a variety of products, from industrial components to household items. It’s like a skilled artist’s paintbrush, delicately applying a thin, even coat to the workpiece. Understanding how these machines work can provide valuable insights into their applications and benefits.
What is a Dip Coating Machine?
Dip coaters are essential tools in the manufacturing industry for applying uniform coatings to a variety of products. Dip coating equipment is a precision instrument used to apply a thin, even layer of paint to a substrate surface. The process is commonly used in industries that require consistent and high-quality coatings, such as automotive, electronics and medical device manufacturing. The process involves dipping the substrate into a paint can and then removing it at a controlled speed to achieve a uniform coating thickness.
The working principle of dip coating equipment is simple. Start by attaching the substrate to the clamp, making sure it is stable and positioned correctly. Next, the substrate is immersed in a tank or reservoir containing the paint. Carefully control the speed of dipping and removing to ensure an even coating. Click for a detailed explanation of dip coating technology.
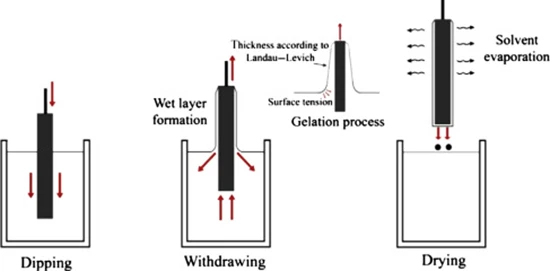
How Does Dip Coating Work
When the substrate is removed, excess coating material will drip off, leaving a thin, even layer on the surface. This process can be repeated multiple times to obtain the desired coating thickness.
Advantages and Disadvantages of Dip Coating Machines | |
---|---|
Advantages | Disadvantages |
Uniform coating thickness | Limited substrate size |
Cost-effectiveness | Lack of control over coating thickness |
Versatility | Longer drying time |
Minimal waste | Environmental impact |
Ease of use |
All in all, dip coating equipment is an essential tool in the manufacturing industry, providing a reliable and efficient method for applying coatings to a variety of substrates. Understanding the basics of how these machines work will help you understand their importance and the role they play in ensuring a high-quality coated product.
How does a Dip Coating Machine Compare to Other Coating Equipment?
Dip coaters are widely used in various industries due to their ability to apply uniform coatings on substrates. However, as with any technology, they have their own advantages and disadvantages compared to other coating methods.
Follow along as we learn how dip coaters compare to other common coating equipment, including roller coating, spray coating, spin coating, flow coating, electrophoresis and electroplating coating equipment.
Comparison of application methods of different coating equipment | ||||||
---|---|---|---|---|---|---|
Aspect | Dip Coating | Roll Coating | Spray Coating | Flow Coating | Spin Coating | Electrophoretic Coating |
Uniformity | High | High | Variable | Medium to High | High | High |
Efficiency | Medium | High | High | High | High | High |
Substrate Size | Small to Medium | Medium to Large | Small to Large | Medium to Large | Small to Medium | Small to Medium |
Control Over Thickness | Limited | High | Medium | High | Limited | High |
Complexity of Shapes | Good | Good | Good | Good | Good | Good |
Environmental Impact | Depends on coating material | Medium to High | High | Medium to High | Medium to High | Low to Medium |
Cost-effectiveness | Good | Medium to High | Medium to High | Medium to High | Medium to High | Medium to High |
Read an overview of 7 common coating application processes.
Dip Coating vs. Flow Coating:
Flow coating involves the continuous flow of coating material over the substrate. It is suitable for large surfaces but may result in uneven coating thickness.
- Advantages of Dip Coating over Flow Coating:
Uniform Coating Thickness: Dip coating provides a more uniform coating thickness compared to flow coating.
Cost-Effectiveness: Dip coating is generally more cost-effective for small to medium-sized production runs.
Suitable for Complex Shapes: Dip coating can coat complex shapes and irregular surfaces more effectively than flow coating. - Disadvantages of Dip Coating Compared to Flow Coating:
Limited to Small to Medium-Sized Substrates: Dip coating is not suitable for large substrates that require continuous coating.
Longer Drying Times: Dip coating may require longer drying times compared to flow coating due to the immersion process.
Dip Coating vs. Spin Coating:
Spin coating involves applying a thin layer of coating material to a rotating substrate. It is used for thin films and uniform coatings. It is worth noting that in some cases spin coating may need to be combined with a dip coating process. Dip the substrate into the paint and spin to apply an even coating.
- Advantages of Dip Coating over Spin Coating:
Suitable for Thicker Coatings: Dip coating is more suitable for thicker coatings than spin coating.
Better for Large Substrates: Dip coating can coat larger substrates than spin coating. - Disadvantages of Dip Coating Compared to Spin Coating:
Limited to Simple Geometries: Dip coating is less suitable for complex geometries compared to spin coating.
Requires Immersion: Dip coating requires the substrate to be immersed in the coating material, which may not be suitable for all applications.
Dip Coating vs. Electrophoretic Coating:
Electrophoretic coating uses an electric field to deposit coatings onto substrates, resulting in a more controlled and uniform coating.
- Advantages of Dip Coating over Electrophoretic Coating:
Lower Cost: Dip coating is generally more cost-effective than electrophoretic coating.
Simplicity: Dip coating is a simpler process that requires less specialized equipment than electrophoretic coating. - Disadvantages of Dip Coating Compared to Electrophoretic Coating:
Less Control Over Coating Thickness: Dip coating may result in less control over coating thickness compared to electrophoretic coating.
Limited to Certain Substrates: Dip coating may not be suitable for all types of substrates, particularly those that require precise control over coating thickness.
In summary, dip coating equipment offers several advantages, including uniform coating thickness, cost-effectiveness, and versatility. However, they also have limitations, such as limited substrate size and lack of control over coating thickness. Understanding these advantages and disadvantages can help manufacturers make informed decisions about using dip coaters in their production processes.
What Industries Benefit Most from Dip Coating Machines?
Dip coating machines are like all-rounders that can take care of different fields. As a versatile tool, it can be used in various industries that require precise and uniform coating. Let’s take a closer look at the industries that benefit the most from these machines and how they can enhance products within those industries.
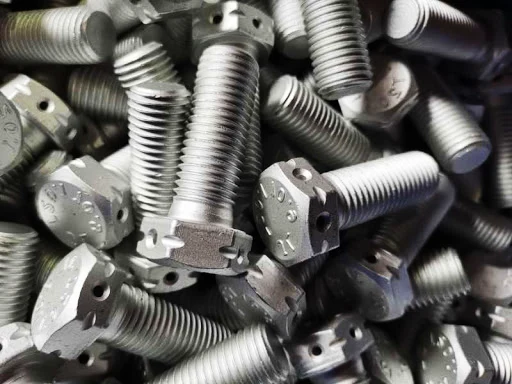
Hot dip coated galvanized finished product
- Industrial Manufacturing:In industrial manufacturing, dip coating equipment is used to apply protective coatings to metal components such as steel pipes, springs, and fasteners. These coatings improve the corrosion resistance of parts and enhance their overall durability, ensuring they can withstand harsh environmental conditions.
- Electronics Industry:In the electronics industry, dip coating machines are employed to apply insulating coatings to electronic components. These coatings protect the components from moisture, dust, and other contaminants, ensuring their reliability and longevity.
- Medical Industry:In the medical industry, dip coating machines are used to apply biocompatible coatings to medical devices and implants. These coatings reduce the risk of infection and improve the compatibility of the devices with the human body, enhancing patient safety and comfort.
- Aerospace Industry:In the aerospace industry, dip coating machines are utilized for applying protective coatings to aircraft components. These coatings protect the components from corrosion, abrasion, and thermal degradation, ensuring the safety and reliability of the aircraft.
- Other Industries:Dip coating machines also find applications in industries such as furniture manufacturing, where they are used to apply decorative coatings to furniture components, enhancing their aesthetic appeal and durability.
All in all, dip coating equipment is an invaluable tool that benefits numerous industries by improving the quality, durability and functionality of their products. Whether improving the aesthetics of surfaces, protecting metal components from corrosion or improving the biocompatibility of medical devices, these machines play a vital role in ensuring the reliability and performance of a variety of products across different industries.
Dip coating equipment comes in various shapes and sizes, each designed for specific applications and industries. Understanding the different types of dip coating equipment available can help you choose the right tool for your coating needs. Let’s dive in and explore the world of dip coating equipment!
- Laboratory Dip Coating Machines:Starting small, laboratory dip coating machines are ideal for research and development purposes. They are compact, easy to use, and allow for precise control over the coating process. These machines are often used to test new coating formulations and techniques before scaling up to larger equipment.
- Large-Scale Industrial Dip Coating Equipment:For mass production purposes, large-scale industrial dip coating equipment is the go-to choice. These machines are capable of coating large volumes of parts or components quickly and efficiently. They are often used in industries such as automotive, electronics, and aerospace for applying protective or decorative coatings.
- Automated industrial dip coating system: In order to simplify the coating process and improve efficiency, an automated chain industrial dip coating system is adopted. The line moves continuously at a constant speed from gripping and carrying substrate items through dipping tanks, ovens and associated handling systems. These continuous chain dip coating equipment systems feature robotics and advanced controls for precise and consistent coating application. They are ideal for high-volume production environments where speed and quality are critical.
- Specialized Functional and Coating-Specific Dip Coating Equipment:In addition to standard dip coating machines, there are also specialized equipment designed for specific functions or coatings. For example, dip-spin coating equipment used to achieve more uniform and thin coatings, there are dip coaters designed to coat thin films for optical or electronic applications. and equipment designed to apply coatings with specific properties, such as anti-reflective or hydrophobic coatings.
In conclusion, the world of dip coating equipment is diverse and offers a range of options to suit different applications and industries. Whether you need a small-scale laboratory machine for research purposes or a large-scale industrial system for mass production, there’s a dip coating equipment that’s right for you. Understanding the different types of equipment available can help you make an informed decision and achieve the best results for your coating needs.
A complete industrial dip coating system is a sophisticated assembly of equipment designed to apply precise and uniform coatings to various substrates. Let’s explore the essential components that make up these systems and how each contributes to the overall coating process.
- Coating Reservoir Tank:The coating reservoir tank is where the coating material is stored. It is equipped with features such as temperature control and agitation to ensure the coating material remains in optimal condition for application. Think of it as the heart of the system, pumping the coating material to where it’s needed.
- Substrate Placement and Fixture Platform:The substrate placement and fixture platform provide a stable and secure base for holding the substrates during the coating process. This component is crucial for ensuring that the substrates are properly positioned and aligned for uniform coating application. It’s like a stage where the substrates perform their coating dance.
- Immersion and Withdrawal System:The immersion and withdrawal system is responsible for lowering the substrates into the coating material and withdrawing them at a controlled speed. This system ensures that the substrates are evenly coated and that excess coating material is allowed to drain off. It’s like a choreographer, directing the movements of the substrates for a flawless performance.
- Drying and Curing Equipment:After the substrates are coated, they need to be dried or cured to set the coating. Drying and curing equipment, such as ovens or UV lamps, are used for this purpose. These equipment ensure that the coating material is properly cured or dried, providing a durable and high-quality finish. They’re like the backstage crew, ensuring that everything is set for the final act.
In conclusion, a complete industrial dip coating system consists of several key components, each playing a crucial role in the coating process. From the coating reservoir tank to the drying and curing equipment, each component contributes to the overall efficiency and quality of the coating application. Understanding these components can help appreciate the complexity and sophistication of dip coating systems in industrial applications.
How to Choose Dip Coating Machine and Equipment?
Are you planning to purchase a powerful assistant for your dip coating business? Whether you are a researcher in a laboratory or a manufacturer in an industrial environment, choosing the right dip coating machine and equipment is a critical decision. Understanding the key factors involved in this decision-making process can help you make an informed choice that meets your specific needs.
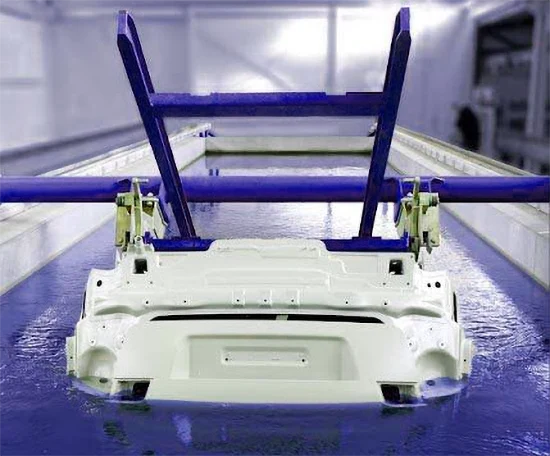
Dip Coating Machine (Dip Coater)
- Application areas:Before delving into technical details, consider your specific requirements. Are you looking for a dip coating system for experimental purposes or industrial applications? The intended use will significantly affect the type of machinery and equipment you need. Often laboratories require desktop dip coating machines with high precision and controllability, while industrial applications require large-scale dip coating equipment suitable for their factory workshop space.
- Operator Note:Identify the primary users of the dip coating system. Are they experienced professionals or new operators? Look for a dip coater with user-friendly features, such as easy-to-use controls and an intuitive interface. These features can make operations more efficient and reduce the learning curve for new users while increasing productivity.
- Key Functions:Evaluate the key functions of a dip coating system. Consider the key features that are critical to your app. These may include aspects such as the ability to control immersion and extraction speeds, uniformity of coating thickness, etc. Considering the functional points supported by the dip coating system will help achieve the target coating effect.
- Coating Material Compatibility:Make sure the dip coating system is compatible with the coating materials you plan to use. Some systems may have limitations on the viscosity or chemical composition of the coating material. Verify compatibility to avoid operational issues and ensure optimal performance. Click to explore popular organic and inorganic coatings.
- Equipment Specifications:Check the specifications of the dip coating equipment in detail. Pay attention to the size and material of the coating vessel, as well as the accuracy and reliability of the immersion and extraction system. Consider the overall build quality and durability of the device.
- Process flexibility:In practical applications of batch impregnation machinery, there will always be situations where new products are added to the production line or coating types and processes are switched. At this time, in order to help us convey multiple different products on the same dip coating system to improve efficiency. Dip coating equipment provides us with greater adjustability. Remember: any method of increasing production capacity requires testing of the entire production line before implementing a batch process.
- Customization options:Some dip coating system manufacturers offer customization options for their dip coating equipment, allowing you to customize the equipment to meet your specific requirements. Evaluate the customization options offered by the manufacturer. Customization can help tailor a dip coating system to your specific requirements, improving its performance and efficiency. Consider whether custom options fit your budget and long-term needs.
- Maintenance and Support:Consider the availability of maintenance services and technical support. A reliable manufacturer should provide comprehensive support to resolve any issues that may arise during operation. Look for warranties and service agreements to protect your investment.
Choosing the right dip coater and equipment requires careful consideration of a range of factors including your specific needs, the key features of the equipment and the customization options available. By considering these must-have options, you can make an informed decision to meet your specific requirements and enhance your dip coating productivity.
How to Adjust Dip Coating Equipment to Troubleshoot?
Dip coating equipment is a valuable tool for applying coatings to various substrates. However, like any machinery, it may encounter issues that affect its performance. In this guide, we’ll explore common defects in dip coating and how to adjust the equipment to troubleshoot them effectively.
Dip Coating Equipment Troubleshooting Guide | ||
---|---|---|
Issue | Cause | Adjustment |
Uneven Coating Thickness | Inconsistent immersion or withdrawal speed | Ensure consistent speed; check substrate fixture stability |
Drips or Runs in the Coating | Excessive coating material or improper viscosity | Adjust withdrawal speed; check coating material viscosity |
Air Bubbles in the Coating | Rapid or uneven withdrawal | Immersion and withdrawal at steady speed; degas coating material before use |
Incomplete Coating Coverage | Insufficient immersion or withdrawal | Adjust immersion depth and withdrawal speed for complete coverage |
Visible Particle Pinholes and Pits | Presence of particles in coating material | Filter coating material; ensure substrate is clean and free of debris |
Cracking Defects | Excessive coating thickness or improper curing | Adjust coating thickness; ensure proper curing process according to manufacturer’s recommendations |
By addressing these common defects and adjusting the dip coating equipment accordingly, you can ensure that your coatings are applied smoothly and effectively. Regular maintenance and inspection of the equipment are also essential to prevent issues and maintain optimal performance. Let’s read on.
How to Maintain and Maintain A Dip Coating Machine?
Your dip coater is an artist’s paintbrush and a magician’s wand, turning ordinary works into coated masterpieces. To ensure your dip coater continues to deliver high-quality coatings and operates smoothly, regular maintenance is essential. Let’s explore how to keep your dip coating equipment in tip-top shape and ensure your coatings stay attractive!
- Clean regularly:Think of your dip coater like a culinary masterpiece; it needs a clean kitchen to work its magic. Regularly clean the dip coater, including the tank, fixtures and extraction system, to remove any residue or build-up that may affect the quality of the coating. Use mild solvents or cleaning solutions recommended by the machine manufacturer to avoid damaging sensitive parts. A clean machine ensures your coating is as pristine as freshly washed dishes.
- Parts Inspection: Like a vigilant guardian guarding a treasure, inspect your dip coater’s parts regularly. Such as dipping and removing the system, whether there are signs of wear or damage. Promptly replace any worn or damaged parts to prevent further problems and ensure smooth operation.
- Lubrication:In the mechanical world, lubrication is the secret. Make sure the moving parts of your dip coater are properly lubricated to reduce friction and wear. Use the lubricant recommended by the manufacturer and follow their guidelines for frequency and quantity of use.
- Calibration: Accuracy is key in dip coating. Regularly calibrate the machine’s dip and exit speeds to ensure even and consistent coating application. Use a calibrated speedometer or tachometer to accurately measure speed. A well-calibrated dip coating machine is like conducting a symphony, ensuring each coat is a masterpiece.
- Training and Education:Knowledge is power, especially when it comes to machine maintenance. Provide training to operators on the proper use and maintenance of dip coating machines. Educate them on the importance of regular maintenance and how it affects coating quality and machine life. Helps ensure your machine is running at its best.
In the world of dip coating, maintenance is the secret to success. By following these maintenance tips, you can ensure your dip coater remains in top condition, delivers high-quality coatings and extends its lifespan. Regular maintenance not only improves machine performance but also reduces the risk of downtime and expensive repairs.
Future Trends in Dip Coating Equipment.
Dip coating equipment has been a cornerstone of surface coating applications for decades. However, advancements in technology are revolutionizing the capabilities of these machines. In what direction will it develop in the future? Let’s explore some of the emerging technologies in dip coating equipment and how they are shaping the future of surface coatings.
- Automated Control Systems: One of the most significant advancements in dip coating equipment is the integration of automated control systems. These systems utilize sensors and algorithms to precisely control the immersion and withdrawal speeds, coating thickness, and other parameters. This not only improves the quality and consistency of the coatings but also reduces the need for manual intervention, making the process more efficient and less prone to errors.
- Robotics and AI: The integration of robotics and artificial intelligence (AI) is another trend that is transforming dip coating equipment. Robots are being used to handle and position the substrates, allowing for more precise and repeatable coating processes. AI algorithms analyze data from sensors to optimize coating parameters in real-time, ensuring optimal coating quality and efficiency.
- Advanced Coating Materials: Advancements in coating materials are also driving innovation in dip coating equipment. New materials, such as self-healing coatings and smart coatings that change properties in response to external stimuli, are being developed. Dip coating equipment is being adapted to accommodate these new materials, opening up new possibilities for applications in various industries.
- Environmental Sustainability: Another trend in dip coating equipment is the focus on environmental sustainability. Manufacturers are developing eco-friendly coatings that reduce the environmental impact of the coating process. Dip coating equipment is being designed to minimize waste and energy consumption, making the process more sustainable.
The future of dip coating equipment is bright, with emerging technologies opening up new possibilities for coating applications. Automated control systems, robotics, advanced coating materials, and environmental sustainability are just some of the trends shaping the future of dip coating equipment. As these technologies continue to evolve, we can expect to see further advancements in the capabilities and efficiency of dip coating machines, revolutionizing surface coating processes across industries. What other new technologies do you think will change the development of dip coating equipment? Please leave a message below to discuss.
To sum up, dip coating equipment plays a crucial role in achieving high-quality coatings. By knowing the different types available, the components of a complete industrial system, and how to address common defects, you can make informed decisions. A complete directory of reliable dip coating machine and industrial dip coating equipment manufacturers and service providers can be filtered by visiting coatingsdirectory.com and using the filter function.
What is a dip tank for?
In the dip coating process, a dip tank refers to a container that holds coatings liquid and is used for dipping or coating. The substrate object is submerged (or partially submerged) in a dip tank to apply a thin, even coating. Immersion tanks are commonly used in industries such as automotive, aerospace and electronics to apply protective or decorative coatings to a variety of products.
What are the requirements for powder coating pretreatment dip tank?
For a powder coating pretreatment dip tank, several key requirements must be met. First, the tank material must be compatible with the pretreatment chemicals used, such as cleaners and phosphates. The tank should also have adequate ventilation to remove fumes and ensure worker safety. Additionally, the tank should be equipped with heating elements to maintain the pretreatment chemicals at the required temperature for optimal performance.
What components does a laboratory dip coating machine consist of?
Laboratory dip coaters typically consist of several key components, including a coating material reservoir, an acrylic panel, a linear actuator assembly, a substrate fixture or clamp, and an additional drying or curing system. The coating material reservoir holds the coating material, while the substrate clamp holds the substrate securely during the coating process. Linear actuator assemblies control the speed and movement of the substrate into and out of the coating material, ensuring uniform coating. Finally, a drying or curing system helps dry or cure the coating after application.
Can dip coating Systems be used for both small and large-scale production?
Yes, dip coating systems are available for both small and large scale production. For large-scale production, automated dip coating systems are more common, where robots or other automated systems handle the dip coating and take-out processes. These systems can be scaled up to accommodate large quantities of substrates, making them suitable for large-scale production. However, it can also be used for small batch experiments. For small-scale production, manual or semi-automatic dip coating systems can be used, with operators manually dipping and removing the substrate.