Article Chapters
Spin coaters or Spin coating machines may sound like something out of a sci-fi movie, but they are actually an indispensable tool in modern manufacturing. From research labs to large-scale manufacturing. These machines are responsible for applying thin, uniform coatings to a wide variety of substrates with unparalleled precision. Follow us as we dive into the different types of spin coaters, key accessories, how to choose the right machine for your needs, and important maintenance and safety tips to see what makes them so fascinating and indispensable.
What is a Spin Coater?
A spin coater is a piece of equipment used to apply a uniform thin film to a flat substrate. It works by depositing a small amount of coating material onto the center of the substrate and then spinning the substrate at a set matching speed, distributing the coating material evenly onto the substrate surface through centrifugal force.
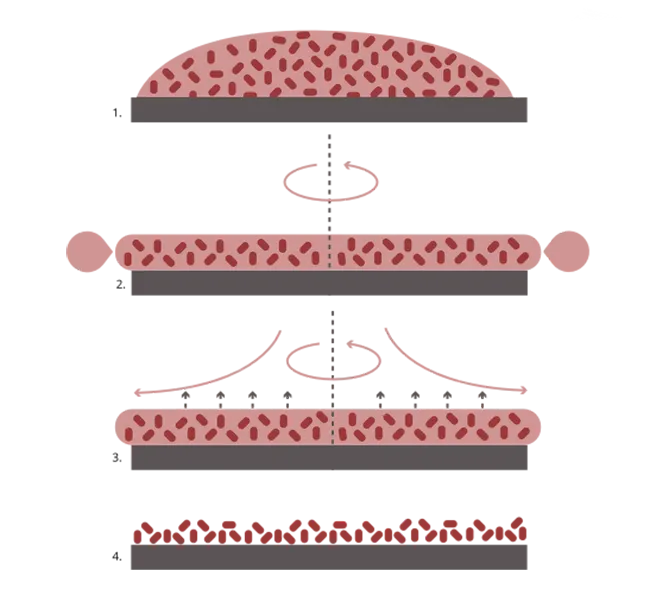
How Spin coater works
Spin coating machines are essential in industries that require precise and uniform coatings. They are widely used in the production of semiconductors, photovoltaic cells, optical components, and even for photoresist applications during micromachining. These machines ensure that the coating remains consistently thin and uniform, which is critical to the performance and reliability of the end product.
Why spin coaters are essential:
- Uniform coating: Spin coaters ensure that the coating is applied evenly, which is critical to the performance of many high-tech products.
- Thickness control: By adjusting the speed and duration of the spin, manufacturers can precisely control the thickness of the coating.
- Efficiency: Spin coating is a fast and efficient process, ideal for high-volume production environments.
Spin coaters (or Spin coating machines) are the marvel of modern manufacturing technology. They provide the precision and control required to apply thin, uniform coatings, which is critical to a wide range of high-tech applications.
What are the Different Types of Spin Coaters?
Spin coaters, also known as spin coaters, are essential tools in the world of thin film deposition. They are widely used in a variety of industries and research fields for forming uniform thin coatings on substrates. But did you know that there are different types of spin coating equipment tailored for specific applications? Let’s delve into the diverse world of spin coaters and discover the unique features of each.
Benchtop Spin Coaters for Research Labs.
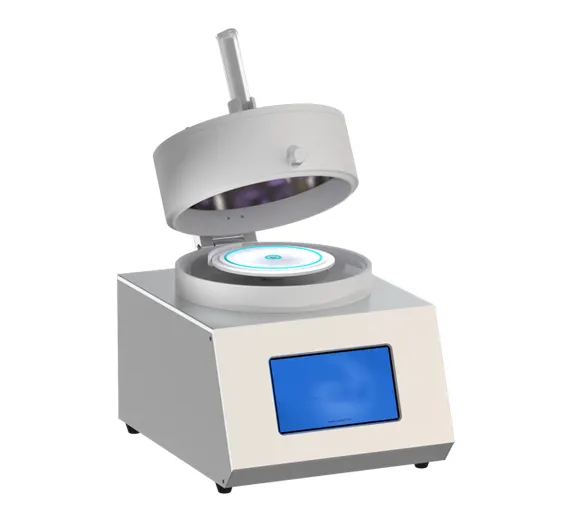
Benchtop spin coaters
Benchtop spin coaters are the workhorses of research labs. These compact and versatile machines are designed for ease of use and precise control, making them ideal for lab-scale applications, research, and development. But only for small and medium-sized substrates. Benchtop spin coaters have several features:
- Precise control: Adjustable spin speeds and programmable parameters allow researchers to fine-tune the coating process.
- Versatility: Suitable for a wide range of coating materials, from photoresists to polymers.
- Compact design: They have a small footprint, making them ideal for limited lab space.
Industrial Automated Spin Coating Equipment.
When it comes to high-volume, large-scale production, industrial automated spin coating equipment reigns supreme. These machines are much larger than benchtop spin coaters and are designed for high throughput and consistent performance. This type of spin coating equipment can process multiple substrates simultaneously and is often integrated into a complete production line that may include multiple automated equipment components.
The most representative machines in Industrial Automatic Spin Coating Equipment are multi-step spin coaters and co-located spin coaters.
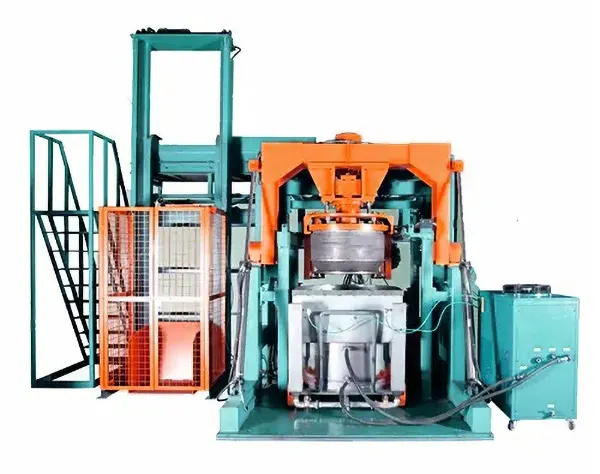
Complete Automated Spin Coating Equipment System
Multi-step Spin Coaters: Multi-step spin coaters are designed for applications that require multiple layers of coating. These machines have multiple dispensing nozzles and programmable steps that allow different materials to be applied continuously without removing the substrate. Maintain efficiency and precise thickness of each layer when applying complex multi-layer coatings.
Co-located Spin Coaters: Co-located Spin Coaters are also called Cluster spin coaters. Known for its ability to integrate the spin coating process with other manufacturing steps, such as deposition or etching, without disrupting the controlled environment. These machines allow for seamless transfer of substrates between different process modules as part of a larger industrial system. Ideal for use in semiconductor manufacturing and other environmentally sensitive high-tech industries.
Industrial spin coating equipment features include:
- Automation: Fully automated processes minimize human intervention, ensure repeatability and reduce errors.
- High throughput: Ability to coat multiple substrates simultaneously, increasing productivity.
- Advanced features: Integration with other manufacturing systems for seamless operation.
Vacuum Spin Coaters.
Vacuum spin coaters are machines designed specifically for environments where contamination must be minimized and for high-precision thickness control. Essential for applications such as semiconductor manufacturing, these coaters offer:
- Contamination Control: Operates under vacuum conditions to prevent particle contamination.
- Enhanced Uniformity: Vacuum conditions improve precise control of film thickness and uniformity by reducing air drag and turbulence.
- Versatile Applications: Ideal for Electronic and Optical Thin Film Deposition.
Nitrogen Purge Spin Coaters.
For sensitive materials that may degrade in the presence of oxygen or moisture, nitrogen purged spin coaters are the perfect solution. This type of spin coating machine utilizes nitrogen or other inert gas to purge the chamber to maintain a specific, highly controlled atmosphere. They provide:
- Inert atmosphere: Nitrogen environment protects sensitive coatings from oxidation and moisture.
- Improves coating quality: Reduces risk of defects and increases stability of coated materials.
- Specialized uses: Commonly used in organic electronics and photovoltaic manufacturing.
Specialized spin coaters for specific applications.
Some applications require spin coaters with unique features, including specialized dispensing systems or material handling capabilities, to meet their specific needs. These specialized spin coaters include:
- Photoresist spin coaters: Designed for precise application of photoresists in the photolithography process.
- Sol-gel spin coaters: Optimized for sol-gel coatings used in ceramic and glass production.
- High-speed spin coaters: Capable of achieving very high spin speeds, suitable for ultra-thin film applications.
Understanding the different types of spin coaters can help you choose the right equipment for your specific needs. Whether you perform research in a lab or run a large industrial operation, there is a spin coater that can meet your requirements. Each type of spin coater has unique specifications, capabilities, and limitations, and considering your specific needs will ensure that you get the best coating application results. So, the next time you start a coating project, consider which spin coater can give your job the spin it needs to succeed.
What are the Important Accessories & Components in a Spin Coating System?
Spin coating systems are essential tools for creating uniform thin films on substrates in a variety of industries and fields of research. While the spin coater or spin coater is the star of the show, ancillary accessories and components play a vital role in ensuring optimal performance and results. Let’s take a closer look at these key components and their functions in a spin coating system.
- Substrate Holders (Chucks):
Substrate holders or chucks are like reliable stage hands that ensure the star stays in place. They securely hold the substrate during the spin coating process. The most common chucks are: vacuum chucks and adjustable chucks. Vacuum chucks use vacuum suction to hold the substrate, providing a secure grip without physical clamping. Adjustable chucks accommodate different substrate sizes and shapes, enhancing the versatility of the system. - Dispensing Systems:
Dispensing systems are precision artists that ensure accurate and uniform application of coating materials. This component includes: syringes and needles, which precisely dispense small amounts of coating material onto substrates, and automated dispensers, which provide consistent and repeatable dispensing, which is critical for high-throughput applications. - Spin Motors and Controllers:
Spin motors and controllers are a dynamic combination that controls the speed and duration of spin. They ensure that coating material is evenly distributed across the substrate. High-precision motors provide precise control of rotation speed, which is critical to achieving uniform coating. Programmable controllers allow users to set specific rotation profiles, including acceleration, speed, and duration. - Encapsulation Covers:
Encapsulation covers are protective shields that prevent contamination and ensure a clean environment during the coating process. Covers and covers are used to protect substrates and coating materials from dust and other contaminants. Inert gas purge systems are used to create a controlled atmosphere to prevent oxidation or moisture contamination. - Vacuum Pumps:
Vacuum pumps maintain the vacuum required for the chuck to securely hold the substrate. They help create a vacuum seal, ensuring the substrate stays in place during high-speed rotation. They also remove air, preventing bubbles and ensuring a smooth, defect-free coating. - Cleaning Stations:
Cleaning stations are diligent custodians used to thoroughly clean chucks and other components, ensuring that all components are free of residue. And ready for the next round of coating. - Drying and Curing System:
The drying and curing system is the finishing touch to ensure that the coating material solidifies properly, providing a durable, uniform surface. This component includes:
Heating Plate: used for initial drying and curing of coating materials.
Ovens and UV curing systems: provide advanced curing options for specific coating materials.
The spin coating system is a well-orchestrated ensemble where each component plays a vital role in achieving high-quality coatings. From the substrate holders to the drying and curing systems, every accessory and component ensures the spin coater performs at its best. Understanding these elements helps in optimizing the spin coating process, ensuring precision, efficiency, and superior results.
How to Choose the Right Spin Coater for Your Needs?
Choosing the right spin coater, or spin coating machine, is crucial for achieving high-quality thin films. To ensure you make the best choice, consider these six key factors: substrate material, size, and shape; coating material; desired film thickness; process requirements; application field; and functional features. Let’s delve into each factor to help you find the perfect spin coating equipment for your needs.
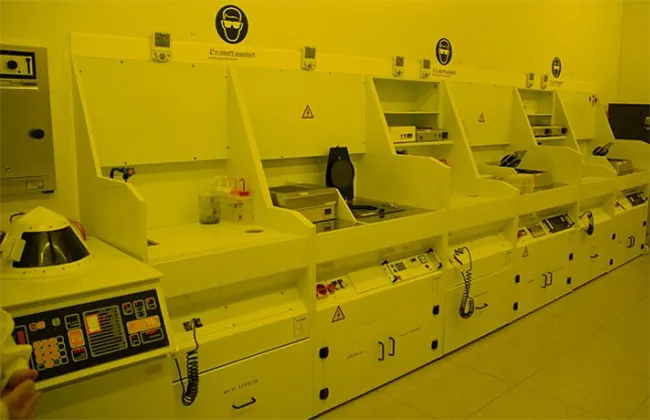
Photoresist spin coating machines
Substrate Considerations (Material, Size, Shape)
The substrate is the foundation upon which your thin film will be deposited. Key factors include:
- Material: Different substrates (glass, silicon, metal) have unique properties that influence coating adhesion and quality. For instance, silicon wafers are commonly used in semiconductor applications, while glass substrates might be preferred in optics.
- Size: Ensure the spin coater can accommodate the maximum dimensions of your substrates. Bench-top models are ideal for smaller substrates, while industrial models handle larger sizes. Measure your substrates and verify the spin coater’s capacity.
- Shape: Standard spin coaters typically handle flat substrates, but if you work with irregular shapes, you might need specialized chucks or adapters to secure the substrates properly during the spin process.
Coating Material
The type of coating material significantly impacts your choice of spin coater:
- Viscosity: High-viscosity materials require robust spin motors to ensure even distribution. Check the spin coater’s specifications for compatibility with the viscosity range of your coating materials.
- Chemical Compatibility: Ensure that the spin coater components (chucks, dispense systems) are resistant to the chemicals in your coating material. Using incompatible materials can lead to degradation and contamination of the coating.
Desired Film Thickness
The required thickness of the film plays a crucial role in determining the right spin coater:
- Spin Speed and Time: Higher speeds and longer spin times generally produce thinner films. Choose a spin coater with adjustable and precise control over these parameters to achieve your desired film thickness.
- Uniformity: Consistent spin speeds and controlled environments help achieve uniform thickness across the substrate. Look for models with advanced speed control and environmental control features to ensure high uniformity.
Process Requirements
Different processes have unique demands:
- Vacuum Requirements: For processes sensitive to contamination, a vacuum spin coater might be necessary to maintain a clean environment. Vacuum spin coaters are essential in applications such as semiconductor fabrication.
- Inert Atmosphere: If your process requires an inert atmosphere (e.g., nitrogen purge), ensure the spin coater supports this feature. This is crucial for preventing oxidation and ensuring the stability of sensitive coating materials.
Application Field
The specific field of application also influences your choice:
- Research and Development: Bench-top models with versatile and programmable features are ideal for R&D settings, allowing researchers to experiment with different parameters and materials.
- Industrial Production: Automated and high-throughput spin coaters are better suited for industrial applications, offering consistency and efficiency. These models often come with features like automated substrate loading and unloading, which streamline the production process.
Functional Features
Consider the functional features that enhance usability and performance:
- User Interface: A user-friendly interface with programmable settings allows for easier operation and repeatability. This is particularly important in both research and industrial settings where multiple users may operate the equipment.
- Data Logging: Advanced models with data logging capabilities enable detailed process analysis and optimization. This feature is valuable for documenting and refining the coating process.
- Maintenance and Cleaning: Easy-to-clean components and robust design reduce downtime and extend the life of the equipment. Consider spin coaters with detachable parts and simple cleaning protocols.
Choosing the right spin coater involves careful consideration of several factors, including the substrate, coating material, desired film thickness, process requirements, application field, and functional features. Of course, if it is a regular laboratory spin coater, you can also take the brand and model into consideration. Generally, big brands have better after-sales service. By evaluating these aspects, you can select a spin coating machine that meets your specific needs, ensuring optimal performance and high-quality results. Whether you are in a research laboratory or an industrial setting, the right spin coater will be a valuable asset in achieving precise and uniform thin films.
How to Maintain Spin Coating Machines?
Proper maintenance and troubleshooting of your spin coater is essential to ensure optimal performance and longevity. We have put together some daily cleaning procedures, regular maintenance tips, and troubleshooting techniques that will hopefully help keep your spin coating equipment in top shape.
Daily Cleaning and Maintenance:
- Start with a Clean Slate: It is critical to clean your spin coater after each use to prevent residue buildup. Use an appropriate solvent to clean the chuck, dispensing system, and other parts that come in contact with the coating material.
- Check for Residue: Inspect the machine for any remaining coating material. Residue can affect the uniformity of subsequent coatings and damage the machine over time.
- Check the Vacuum System: Make sure the vacuum system that holds the substrate is free of contaminants and operating properly. In particular, listen for any unusual sounds from the vacuum pump, which could indicate a problem.
- Clean the Encapsulation Cap: Dust and contaminants can settle on the encapsulation cap and affect the coating process. Wipe it down regularly to maintain a clean environment.
Regular Maintenance Tips:
- Lubricate Moving Parts: Lubricate the moving parts of your spin coater regularly to reduce wear. Use the manufacturer’s recommended lubricant for best results. Note: Over-lubrication is just as bad as under-lubrication, so follow your equipment’s instructions closely.
- Calibrate Spin Speed: Over time, spin speeds can drift from their set values. Calibrate spin speeds regularly to ensure accurate and consistent coatings.
- Inspect Electrical Connections: Check all electrical connections for signs of wear or damage. Loose or corroded connections can cause failures.
- Replace Wear Parts: Parts such as vacuum seals and dispensing needles wear over time. Inspect these parts regularly and replace as needed.
Maintaining and troubleshooting spin coaters does not have to be a daunting task. With regular cleaning and timely maintenance, you can ensure that your spin coating equipment performs at its best. Remember, a well-maintained spin coater is like a well-tuned musical instrument – harmonious, reliable, and able to create a perfect coating every time.
How to Troubleshoot Spin Coating Machine Failure?
Spin coaters are essential for producing uniform thin films, but like any precision equipment, they are subject to some malfunctions. Therefore, it is critical for spin coaters to understand some common problems and their solutions to maintain efficiency and product quality.
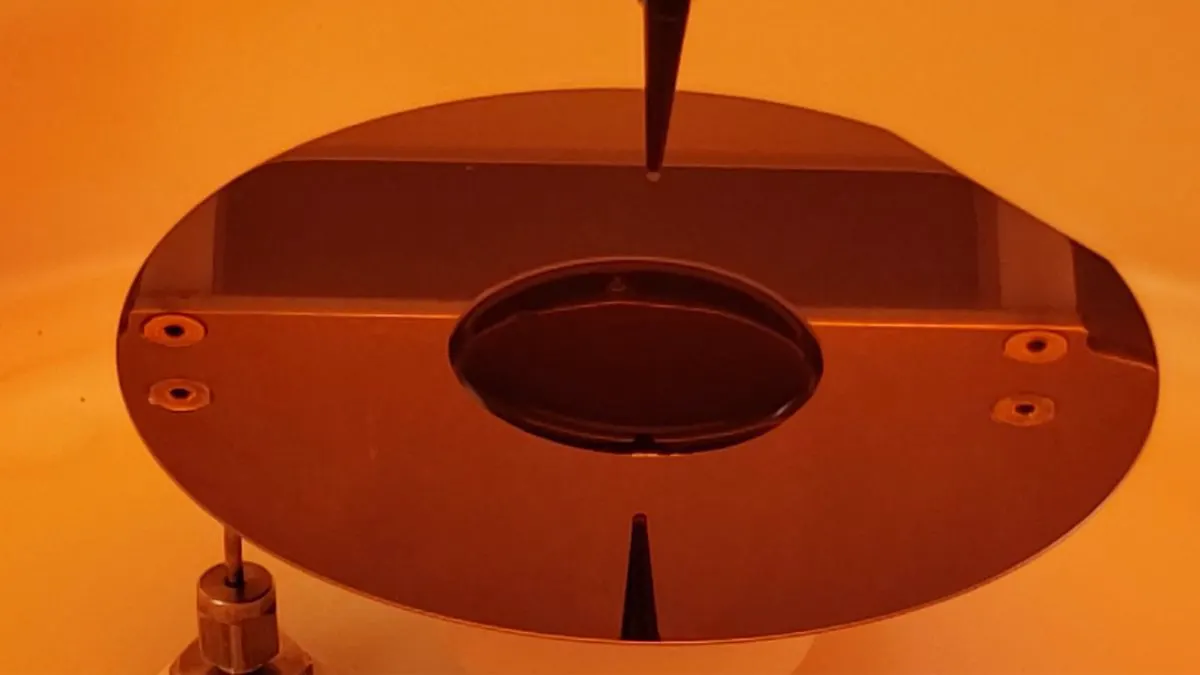
Spin coater
Common Spin Coating Machine Issues and Solutions | ||||
---|---|---|---|---|
Issue | Symptoms | Possible Causes | Troubleshooting Tips | Solution |
Uneven Coating Thickness | Variability in film thickness across the substrate | Incorrect spin speed or time, substrate not level | Verify and adjust spin speed and time, check substrate level | Calibrate spin speed and time settings, level the substrate |
Coating Bubbles | Presence of air bubbles in the coating layer | Contaminated substrate, improper dispensing technique | Clean the substrate thoroughly, adjust dispensing method | Ensure substrate is clean, dispense coating material evenly |
Incomplete Coating Coverage | Areas of the substrate remain uncoated | Insufficient coating material, incorrect spin parameters | Increase amount of coating material, verify spin parameters | Dispense adequate coating material, adjust spin settings |
Chipping or Peeling Coating | Coating detaches from the substrate after curing | Poor adhesion, substrate contamination | Improve substrate cleaning, use adhesion promoter | Ensure thorough cleaning, apply adhesion promoters if needed |
Non-uniform Coating | Irregularities or streaks in the coating | Uneven dispensing, improper spin acceleration | Check dispensing uniformity, adjust acceleration settings | Dispense uniformly, optimize spin acceleration profile |
Machine Vibration | Noticeable vibration during operation | Loose components, unbalanced substrate | Inspect and tighten machine components, ensure substrate balance | Secure all components, balance the substrate |
Spin Motor Failure | Spin motor does not start or stops abruptly | Electrical issues, motor malfunction | Check power supply, inspect motor connections | Ensure stable power supply, repair or replace the motor |
Vacuum Chuck Malfunction | Substrate not held securely, loss of vacuum during spin | Vacuum leak, damaged chuck | Inspect vacuum lines and chuck for leaks or damage | Repair or replace faulty vacuum lines or chuck |
Dispensing System Blockage | Coating material not dispensing correctly | Clogged needle or dispenser | Clean or replace the needle or dispenser | Regularly clean dispensing system, use appropriate needles |
Overheating | Machine components becoming excessively hot | Poor ventilation, high operational load | Ensure adequate ventilation, reduce operational load | Improve ventilation, allow cooling periods between operations |
What are the Safety Considerations When Using Spin Coaters?
Ensuring safe operation of your spin coating equipment not only protects the operator, but also ensures optimal results from the spin coating process. Let’s take a look at basic safety measures, hazardous materials handling, and emergency procedures when using a spin coater.
Topic | Details |
---|---|
Personal Protective Equipment (PPE) | Safety Glasses: Protect your eyes from splashes of coating materials and solvents. Gloves: Prevent skin contact with hazardous chemicals. Lab Coats: Shield your clothes and skin from potential spills. |
Proper Ventilation | Fume Hoods: Use a fume hood when handling volatile substances to keep the air clean. Exhaust Fans: Maintain proper air circulation to disperse any fumes quickly. |
Handling Hazardous Materials | Read Material Safety Data Sheets (MSDS): Familiarize yourself with the properties and hazards of the chemicals you’re using. Label Containers: Clearly label all containers with their contents and hazard information. Storage: Store chemicals in appropriate containers and cabinets, away from incompatible substances. |
Equipment Safety | Secure the Substrate: Ensure the substrate is properly secured on the chuck to prevent it from flying off during high-speed spinning. Check for Damage: Regularly inspect the spin coater for any signs of wear or damage. Follow Manufacturer Instructions: Always adhere to the manufacturer’s guidelines for operation and maintenance. |
Emergency Procedures | Spill Kits: Keep spill kits readily available to quickly clean up any chemical spills. First Aid Kits: Ensure first aid kits are accessible and stocked with necessary supplies. Know Your Exits: Familiarize yourself with the emergency exits and evacuation routes in your workspace. Emergency Contacts: Keep a list of emergency contacts, including poison control and emergency medical services, within reach. |
Regular Training and Drills | Safety Training: Participate in safety training sessions to stay updated on best practices. Emergency Drills: Conduct regular emergency drills to ensure everyone knows what to do in case of an incident. |
Remember, a safe lab is a happy lab, and taking these precautions ensures that you can focus on achieving the best results with your spin coating machine.
In conclusion, understanding the different types of spin coaters, their component functions, and proper maintenance is essential to achieving the best coating performance. We invite you to share your thoughts and experiences with spin coating equipment in the comments below. Don’t forget to use the “coatingsdirectory.com” filter tool to find the best spin coating service provider and equipment manufacturer that best suits your needs.
How to operate a spin coater?
Operating a spin coater is simple! First, secure the substrate to the vacuum chuck and apply the coating solution to the center. Set the desired spin speed and duration, press start, and let the machine work its magic. In more detail, make sure the substrate is clean and dry before you begin. Once secured, dispense a measured amount of coating solution. The spin coater will evenly apply the solution by spinning the substrate at high speeds. Adjust the parameters based on the desired thickness and uniformity, and after spinning, follow any necessary drying or curing steps.
What speed is a spin coater?
Typical speeds for spin coaters range from 1500-6000 rpm, and Most common spin coaters will also reach a maximum speed of 6000 to 8000 rpm (although specialist coaters may go to 12000 rpm or higher). In more detail, the speed you choose affects the thickness and uniformity of the coating. Lower speeds (around 500 RPM) are used for thicker coatings, while higher speeds (up to 10,000 RPM) are used for ultra-thin films. The optimal speed depends on your coating fluid, desired film thickness, substrate properties, and specific application requirements. By adjusting the speed setting, you can achieve the exact coating characteristics you need for your project.
What substrates are compatible with spin coating?
Spin coating is suitable for many substrates, including glass, silicon wafers, metals, and plastics. In more detail, glass is commonly used in optics and electronics due to its smooth, transparent surface. Silicon wafers are the preferred choice in the semiconductor industry for coating thin films such as photoresists. Metal coatings can be used for protection or functional enhancement in a variety of industrial applications. Plastics are used in flexible electronics and displays. The key to a successful spin coating process is to ensure that the substrate is clean and properly prepared to achieve an even and adherent coating.
What are the Applications of Spin Coating?
Spin coating is used in various fields like semiconductor manufacturing, optics, and biomedical devices. For a bit more detail, in semiconductor manufacturing, it’s used for applying photoresists and other thin films. In optics, spin coating helps create anti-reflective and protective layers on lenses. In biomedical devices, it’s used for coating surfaces with biocompatible materials. Its ability to produce uniform, thin films makes it versatile for different high-precision applications.
What Factors Affect the Quality of Spin Coating?
The quality of spin coating is influenced by spin speed, viscosity of the coating solution, and substrate preparation. For a bit more detail, the spin speed determines the thickness and uniformity of the coating. A higher viscosity solution requires a different spin speed compared to a lower viscosity one to achieve the desired film thickness. Proper substrate preparation, such as cleaning and drying, ensures good adhesion and uniformity of the coating. Environmental factors like temperature and humidity can also play a role in the final coating quality. For more detailed information on the key factors for spin coating quality, please visit our corresponding blog.