Article Chapters
Flow coating is a complex technique used across industries to achieve smooth, uniform finishes on different substrates. This comprehensive guide covers everything you need to know about flow coating, including preparation, application, optimization, and troubleshooting common issues. Whether you are a beginner or an experienced professional, you will find valuable insights to improve your coating results. To help you master the art of flow coating.
What Is Flow Coating?
Flow coating is an automated method of applying liquid coatings. A coating process in which a liquid coating is poured or sprayed onto a substrate and the coating flows under controlled gravity over the substrate, distributing it evenly over the surface. The technique is particularly effective for coating complex shapes and ensuring an even coating without much manual labor. The flow coating process seems simple but requires a certain amount of skill to achieve the desired effect.
The flow coating process begins with preparing the substrate, which must be clean and free of contaminants. The coating (usually a liquid such as paint, varnish or lacquer) is then applied to the substrate. Gravity and the viscosity of the coating work together to ensure that the coating is evenly distributed over the surface. The gravity feature allows it to be used to coat a variety of surfaces. Excess coating is collected, filtered and mixed with new coating and replenishing solvent for recycling, making the process more efficient and reducing waste. For some special shapes, some of the limitations of spraying and dipping are overcome.
Click here to learn about the spray coating process.
Click here to learn about the dip coating process.
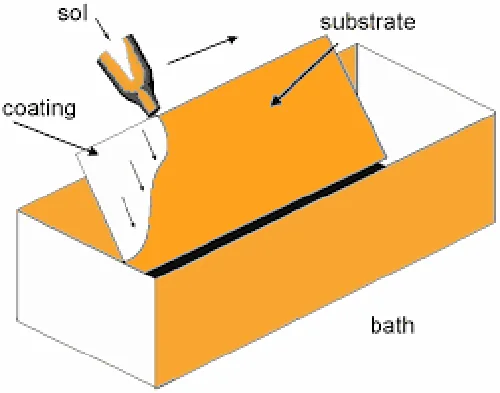
Flow coating process
Advantages and Limitations of Flow Coating.
As an automated coating application system. One of the main advantages of flow coating is its ability to provide a high-quality finish with minimal human intervention. Automated systems can precisely control flow rate, coating thickness, and drying time, ensuring consistent results. In addition, excess coating material can be recycled, making the process both environmentally friendly and cost-effective. Flow coating produces scratch-resistant, durable coatings with improved gloss and image clarity compared to traditional spray techniques. It offers a variety of advantages, but also has some limitations. The following table outlines the advantages and limitations of flow coating in detail to help you understand its suitability for different applications.
Advantages | Limitations | ||
---|---|---|---|
Features | Description | Features | Description |
Uniform Coating | Flow coating ensures a smooth and even layer of coating material, reducing the likelihood of streaks and inconsistencies. | Requires Careful Substrate Preparation | The substrate must be meticulously cleaned and prepared to avoid defects in the coating. |
Efficiency and Speed | Automated flow coating systems can quickly and efficiently coat large quantities of products, saving time and labor costs. | Limited to Liquid Coatings | This technique is primarily suitable for liquid coatings, which may limit its use with certain types of materials. |
Cost-Effective | The recirculation of excess coating material reduces waste and lowers overall material costs. | Excess Coating Management | Managing and recycling excess coating material requires additional equipment and maintenance. |
Versatility | Suitable for a wide range of substrates, including metals, plastics, ceramics, and composites. | Environmental Considerations | The use of certain coating materials may have environmental implications, requiring proper handling and disposal. |
Minimal Manual Intervention | Automated systems reduce the need for manual labor, minimizing the risk of human error. | Thickness Control Challenges | Achieving consistent coating thickness can be challenging, especially with very thin or very thick layers. (For very thin coatings, spin coating is usually recommended) |
Enhanced Surface Protection | Provides a durable and protective finish that enhances the longevity and performance of coated products. | Equipment Costs | Initial setup and maintenance of flow coating equipment can be expensive. |
Flow coating offers numerous advantages, making it a valuable technique in many industries. However, understanding its limitations is essential for optimizing its use and ensuring the best possible results. By carefully considering both the benefits and challenges, you can determine if flow coating is the right choice for your specific application.
In summary, flow coating is a versatile, efficient coating technique that has stood the test of time. From the earliest hand-painting methods to modern high-tech industrial processes, flow coating has proven to be an invaluable tool for achieving smooth, uniform finishes in a wide range of applications. Whether you are coating a complex aerospace component or a simple piece of furniture, flow coating offers a reliable and effective solution. So, the next time you admire the surface of a perfectly coated surface, remember the flow coating process that makes it possible – an art and science that is constantly evolving and improving.
The origins of flow coating can be traced back to early painting techniques, when craftsmen would pour paint on a surface to achieve an even effect. However, it was not until the mid-20th century that flow coating became a standardized industrial process. Advances in materials science and engineering have led to the development of precision flow coating equipment and techniques, enabling precise and consistent coating of a wide range of materials.
In the early days, flow coating was primarily used in the automotive and furniture industries, where achieving a smooth, durable surface was critical. Over time, the process has evolved to incorporate new technologies and advanced materials, such as automated flow coating systems, which have improved the quality and efficiency of coating.
Today, modern flow coating is used in a wide range of industries for its versatility and effectiveness. The process has been modified to accommodate different types of substrates and coating materials, from metals and plastics to ceramics and composites. Here are some common areas where flow coating is used:
- In the automotive industry, it is used to coat automotive parts, providing corrosion resistance and a smooth surface.
- The electronics industry uses flow coating to apply insulating layers to circuit boards and components, protecting them from environmental factors such as moisture and dust.
- In the aerospace industry, flow coating technology is used to coat aircraft components, increasing their durability and resistance to extreme conditions.
- The construction industry also benefits from flow coating technology, using it to apply protective and decorative coatings to building materials and structures.
- The furniture industry uses flow coating to achieve a smooth, high-quality finish on wooden and metal furniture.
How to Prepare for Flow Coating?
Imagine trying to paint a masterpiece on a dirty, uneven canvas. The result would be far from perfect. The same principle applies to flow coating. Proper surface preparation is crucial for ensuring that the coating adheres well, provides a smooth finish, and lasts longer. A well-prepared surface helps avoid common issues such as coating flow irregularities, bubbles, and peeling, ensuring a clear and professional result. CoatingsDirectory recommends the following pre-treatment steps before implementing the flow coating process:
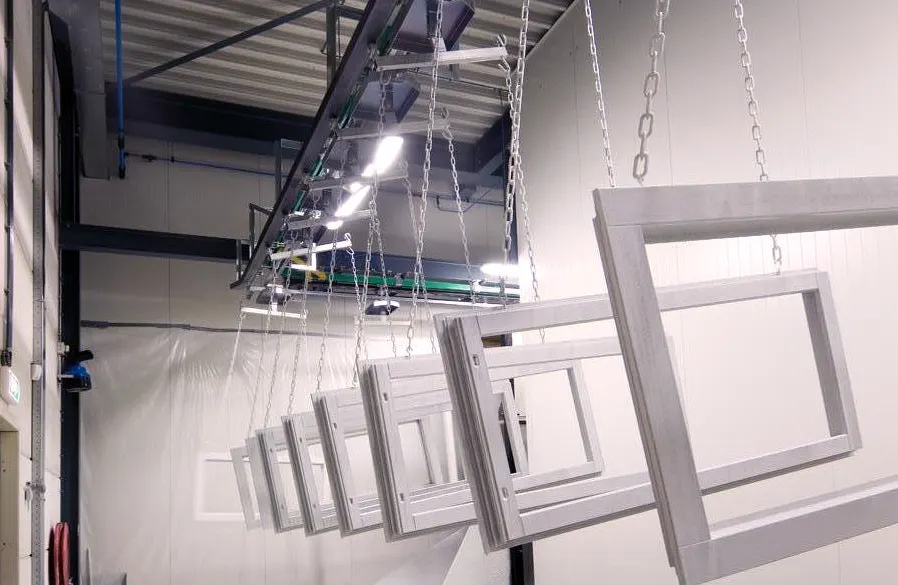
Flow Coating Machine in Action–Substrate cleaning completed
- Cleaning the Surface:
Begin by thoroughly cleaning the substrate to remove any dirt, grease, oil, or other contaminants. Use appropriate cleaning agents based on the material of the substrate. For metals, a degreasing solution works best, while for plastics, a mild detergent may suffice.
Rinse the substrate with clean water and let it dry completely. Any residual moisture can affect the adhesion of the coating. - Sanding and Smoothing:
Lightly sand the surface to create a slightly rough texture, which helps the coating adhere better. Use fine-grit sandpaper for this purpose.
After sanding, remove any dust or particles using a clean, dry cloth or a compressed air blower. This step ensures a clean surface for the primer application. - Applying the Primer:
Choose a primer that is compatible with both the substrate and the coating material. The primer serves as a bonding agent, improving the adhesion of the flow coating.
Apply the primer evenly using a brush, roller, or spray, depending on the substrate’s shape and size. Ensure a uniform coat without any drips or runs.
Allow the primer to dry completely as per the manufacturer’s instructions before proceeding to the next step. - Pre-Treatment for Specific Materials:
For metals, consider additional pre-treatment steps like phosphating or anodizing to enhance corrosion resistance and adhesion.
For plastics, a flame treatment or plasma treatment might be necessary to improve surface energy and coating adhesion.
After carefully preparing the substrate by cleaning, sanding and priming, you are almost ready to start the flow coating process. However, it is important to remember that a well-prepared surface is only part of the process. Ensuring safety during the coating process is equally important. Taking the necessary safety precautions when performing flow coating applications will protect you and your workplace, ensuring a smooth and hazard-free operation. Follow along as we continue to explore the key safety measures you should implement to maintain a safe and efficient painting environment.
Essential Safety Measures for Flow Coating Process.
- Personal Protective Equipment (PPE):
Always wear appropriate PPE, including gloves, safety goggles, and a respirator, to protect yourself from harmful fumes and chemicals.
Ensure that your work area is well-ventilated to avoid inhaling toxic vapors. - Handling and Storage:
Store all chemicals, including cleaners, primers, and coating materials, in their original containers and in a cool, dry place.
Follow all safety instructions provided by the manufacturers for handling and disposal. - Equipment Safety:
Regularly inspect and maintain all equipment used in the flow coating process to ensure it is in good working condition.
Follow proper operating procedures to avoid accidents and ensure a consistent coating application. You can visit our corresponding blog for detailed flow coating Machines daily maintenance guide.
Preparing for flow coating is a meticulous process that demands attention to detail and adherence to safety protocols. By thoroughly cleaning, sanding, and priming your substrate, you set the stage for a flawless coating flow. Remember, the quality of your flow coating clear finish depends largely on how well you prepare the surface. So, take the time to do it right, and you’ll achieve professional, long-lasting results that shine. Happy coating!
How Does Flow Coating Work?
Flow coating involves applying a liquid coating to a substrate, allowing it to flow and spread evenly over the surface. Excess coating that drips off is then collected, filtered, and automatically reintroduced into the coating system. This process ensures an even coating and requires no human intervention, making it ideal for efficiently coating complex shapes and large surfaces.
Flow coating can be done by feeding parts into an enclosed space via a conveyor belt, or it can be done in a flow coating chamber. It is important to note that flow coating, like dip coating, suffers from solvent backflow and a wedge effect. To understand how flow coating works, we first need to understand the basic equipment and materials required for the process. The basic materials and equipment required to implement the flow coating process are as follows:
- Substrate: The item being coated, which ranges from metals, plastics, ceramics, and composites.
- Coating material: The primary material used in flow coating is the liquid coating itself, which can be paint, varnish, lacquer, or any other liquid suitable for the application. The choice of material depends on the desired characteristics of the final coating, such as durability, appearance, and protection.
- Flow coating chamber: This is the controlled environment in which the flow coating process takes place. The flow coating chamber is designed to contain the coating material and prevent contamination.
- Substrate Holder: A fixture or holder holds the substrate (the item to be coated) in place, ensuring it remains stable during the coating process.
- Pump and Nozzle: These are used to deliver the coating material to the substrate. The pump controls the flow rate, while the nozzle ensures that the material is evenly distributed.
- Collection and Recirculation System: Excess coating material is collected and recirculated back into the system, minimizing waste and ensuring efficient use of materials.
Once the equipment and materials are ready, flow coating can begin. The following steps are typically required for the flow coating process.
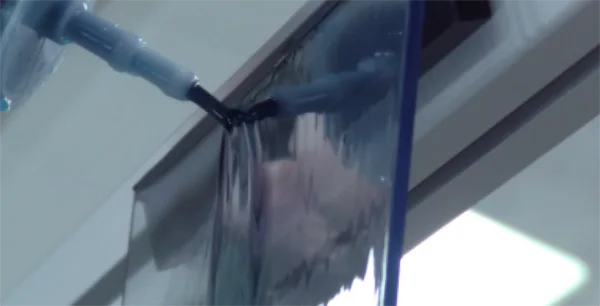
Perform flow coating construction
- Preparation: Proper substrate preparation, including cleaning, degreasing, and surface preparation, ensures optimal adhesion and prevents defects.The substrate must be thoroughly cleaned and prepared to ensure optimal adhesion of the coating. Remove any dust, grease, or contaminants to create a pristine surface.
- Positioning: The substrate is placed in the flow coating chamber and secured to the holder. Proper positioning is critical to achieving an even coating.
- Coating Application: The pump delivers the coating material through the nozzle, pouring or spraying the liquid onto the substrate. Gravity helps the coating material flow evenly across the surface. The flow rate and viscosity of the coating material are carefully controlled to ensure an even coating. Generally, we recommend that the coating “flood” the part so that the coating can carry away specific debris on the part and aid adhesion by increasing the “wet time” of the coating on the part.
- Drainage and Recirculation: As the coating material flows over the substrate, excess material is drained and collected by the recirculation system. This excess material is filtered and pumped back into the system for reuse.
- Drying or Curing: Once the substrate is coated, it enters the drying or curing stage. Depending on the type of coating material used, this may involve air drying, baking in an oven, or using UV light to cure the coating. This step ensures that the coating hardens and adheres properly to the substrate.
- Inspection and Quality Control: After drying or curing, the coated substrate is thoroughly inspected to ensure that the coating is uniform and free of defects. Quality control measures may include visual inspection, thickness measurement, and adhesion testing.
To achieve the ideal flow coating effect, we usually need to repeat the process of flow coating-curing-sanding for 2-3 times. These process flows are just the basics of flow coating. In some special applications and customer requirements, construction workers need to flexibly adjust some key parameters and variables as needed.
Key Parameters and Variables of Flow Coating Process.
- Coating material characteristics: The specific characteristics of the coating material, such as density, surface tension and rheology, affect its flow behavior and final appearance. In particular, the viscosity of the coating plays a key role in determining the behavior of the coating. Lower viscosities produce thinner, more fluid coatings, while higher viscosities produce thicker, stickier coatings.Note: When using water-based coatings, foaming and foaming need to be controlled.
- Application speed: The application speed has a significant impact on the final result. The faster the application speed, the thinner the coating, while the slower the speed, the thicker the coating.
- Substrate speed: The speed at which the substrate passes through the application area affects the consistency of the coating. The faster the speed, the thinner the coating, and the slower the speed, the thicker the coating.
- Equipment configuration: The configuration of the flow coating equipment, including nozzle size, spray angle and air pressure setting, determines the application mode and thickness of the coating.
- Substrate Properties: The nature of the substrate (i.e., the surface to be coated) has a significant impact on the flow coating process. Factors such as material, texture, and surface tension must be considered to ensure optimal adhesion and uniform surface finish.
- Environmental Conditions: Environmental factors, including temperature, humidity, and air circulation, subtly affect the flow coating process, carefully controlling evaporation to obtain a uniform coating. Maintaining consistent environmental conditions minimizes variation and promotes consistent results.
- Curing Conditions: Curing conditions, which include temperature, humidity, and time, determine the final hardness, durability, and chemical resistance of the coating. Proper drying or curing conditions are critical to the performance of the coating. Curing conditions must be optimized based on the coating material and substrate. A suitable flow coating curing space can be created by adjusting the settings of the drying room or drying equipment.
The above several key parameters and variables affect the flow coating application process, which in turn affects the quality and efficiency of the final coating. Remember that consistency in the application process, meticulous preparation, and continuous learning are the keys to success. By understanding and closely controlling these key parameters and variables, you can transform flow coating from a mere technique to an art form. With each successful application, your skills will improve, your expertise will be refined, and you will create fascinating and inspiring masterpieces.
As an efficient and versatile process, flow coating can be used to achieve a uniform and high-quality surface finish on a variety of substrates. By understanding the equipment & materials involved, process steps and critical parameters, we can appreciate the complexity and effectiveness of this technology. Whether you are in the automotive, electronics or aerospace industries, flow coating provides a reliable and efficient solution to obtain smooth, durable and beautiful surfaces.
How to Optimize Flow Coating Performance?
With the above knowledge, I believe you have an understanding of the flow coating process and some key parameters that determine coating quality. Next, follow CoatingsDirectory to continue to learn more about best practices to improve coating quality and ensure high-quality coatings every time.
- Prepare the Substrate:Ensure the substrate is clean and free of contaminants such as dust, grease, or oils. Proper surface preparation is crucial for achieving a uniform and adherent coating.
- Control Coating Viscosity:Adjust the viscosity of the coating material to suit the specific application. The right viscosity ensures smooth flow and even distribution over the substrate. Use viscosity cups or rheometers to measure and maintain the desired consistency.
- Maintain Consistent Flow Rate:Use automated systems to control the flow rate of the coating material. Consistent flow rates prevent defects such as runs or sags and ensure an even coating thickness.
- Optimize Application Environment: Maintain a controlled environment with consistent temperature and humidity levels. Environmental factors can affect the drying and curing process, impacting the final coating quality.
- Use Quality Coating Materials: Select high-quality coating materials compatible with the substrate and application requirements. Using subpar materials can lead to poor adhesion, uneven finishes, and reduced durability.
- Implement Proper Drying and Curing Techniques: Ensure the coated substrates are dried and cured according to the manufacturer’s specifications. Proper curing enhances the coating’s adhesion, hardness, and overall performance. At this time, it is very important to choose a suitable drying & curing equipment.
To further optimize flow coating performance, it’s essential to recognize and address common errors in the process. The table below outlines typical issues, their causes, and solutions:
Common Flow Coating Errors, Causes, and Solutions | ||
---|---|---|
Error | Cause | Solution |
Uneven Coating Thickness | Inconsistent flow rate | Calibrate and maintain consistent flow rate |
Runs or Sags | Excessive coating application | Adjust flow rate and viscosity |
Air Bubbles in Coating | Contaminants or trapped air in coating | Filter coating material and degas if necessary |
Poor Adhesion | Improper surface preparation | Ensure thorough cleaning and surface prep |
Drying Defects (e.g., Orange Peel) | Inadequate drying/curing conditions | Control environmental factors (temperature, humidity) |
Pinholes or Craters | Contamination on substrate or in coating | Clean substrate thoroughly, use clean coating materials |
Color Variation | Inconsistent mixing of coating material | Ensure thorough and consistent mixing |
Optimizing flow coating performance involves a combination of proper preparation, precise control of application parameters, and addressing common issues proactively. By following these best practices and troubleshooting common errors, you can achieve high-quality, uniform coatings that enhance the durability and appearance of your products. Remember, the key to flawless flow coating lies in the details, so pay attention to every step of the process for the best results. If you have more flow coating suggestions and guidance, please leave a message below to communicate, so that everyone can build a better flow coating process together.
In summary, optimizing flow coating performance requires careful preparation, precise control, and proactive troubleshooting. By following the best practices and solutions outlined in this guide, you can achieve high-quality coatings that enhance product performance. Don’t forget to visit coatsdirectory.com to find a trusted partner for all your flow coating needs. For example: reliable flow coating material suppliers, industrial flow coating services, and flow coating equipment manufacturers.
What is Flow Coating a Car?
Flow coating a car involves applying a uniform layer of paint or protective coating to the vehicle’s surface using the flow coating method.
This technique is particularly popular in the automotive industry for its ability to produce a smooth, high-quality finish. The process involves pouring or spraying the coating material over the car’s surface, allowing it to flow and settle evenly. This method reduces the appearance of brush marks or uneven textures that can occur with traditional painting methods. Flow coating is ideal for achieving a sleek, professional look, enhancing both the appearance and durability of the car’s paintwork.
How many coats for a flow coat?
Flow coating is usually applied in 3-4 coats. Flow coating is designed to provide a smooth and even surface with minimal effort. Usually, one coat is enough to achieve the desired coverage and protection. However, for surfaces that require extra durability or for repeated application 2-3 times after the first coat.
How long does flowcoat take to fully cure?
Flowcoat typically takes 24 to 48 hours to fully cure, depending on the specific product and environmental conditions. Flowcoat cure times will vary depending on factors such as temperature, humidity and the type and thickness of coating applied.
Although the surface may feel dry to the touch within a few hours, a complete cure process is required to achieve full hardness and durability. It is important to follow the manufacturer’s cure time guidelines to ensure the coating performs as expected and provides lasting protection.
What Grit Sandpaper for Flow Coating?
For flow coating, 320 to P600 grit sandpaper is recommended for surface preparation.
Preparing the substrate with the appropriate grit sandpaper ensures proper adhesion and a smooth surface. Using 320 to 400 grit sandpaper helps to create a slightly rough surface for the flow coating to adhere effectively. After applying the flow coating, sanding the surface evenly with P600 sandpaper helps with the secondary flow coating. It is critical to note that any dust or debris is removed.
Can you flowcoat over flowcoat without sanding?
It is generally not recommended to flow coat over an existing flow coat without sanding.
For the best possible adhesion, you will need to sand the first coat and wipe with accetone before doing the second coat. The surface of the existing flow coat should be lightly sanded with fine sandpaper (about 400 grit) to create a suitable bonding surface. Sanding helps remove any shine and provides a texture to which the new layer can adhere. Skipping this step will result in poor adhesion and compromised coating performance, causing it to flake or peel over time. you will need to sand the first coat and wipe with acetone before doing the second coat.