Article Chapters
Flow coaters are essential in a variety of industries, providing smooth, uniform coatings on a wide range of products. But did you know how many different types of flow coating equipment there are? What equipment & components make up a complete flow coating system? Today, here at CoatingsDirectory, we take a deep dive and show you how to choose the right flow coating system for your specific needs. We also explore the environmental considerations of using flow coaters to ensure you make an informed, environmentally friendly decision.
What Are Flow Coaters?
Flow coaters, also known as flow coating machines, are specialized equipment designed to evenly apply primers and topcoats. These machines are widely used in industries that require high-quality, consistent coatings, such as automotive, electronics, and furniture manufacturing.
Flow coaters operate by seamlessly coordinating a variety of components. The process begins with the substrate being prepared for coating. The coating material is pumped from a reservoir through a precisely calibrated nozzle or dispenser to ensure a controlled and steady flow. The coated parts are mounted on a conveyor using rods for transport to a vacuum chamber. As the substrate moves along the conveyor or remains stationary, the coating material, such as paint or varnish, that was sprayed over flows over its surface, using gravity and surface tension to form an even coating. Excess coating material is collected and recirculated back to the reservoir, minimizing waste.Finally, the coated substrate is conveyed to a flashing and heating zone for drying or curing, which cures the coating and ensures it adheres firmly to the substrate. This harmonious interplay of the components of a flow coating system produces a perfectly coated product every time.
Why Are Flow Coaters Important?
Flow coaters offer several significant advantages that make them invaluable in various industries:
- Consistency: They provide a uniform coating thickness, which is crucial for both aesthetic and functional purposes.
- Efficiency: Flow coaters minimize material waste and optimize the use of coating materials.
- Versatility: They can handle a wide range of coating materials, from paints and varnishes to adhesives and sealants.
- Speed: Flow coating is a rapid process, ideal for high-volume production lines.
Flow coaters are the unsung heroes behind many perfectly coated products. By understanding how these machines work, we can appreciate the blend of art and science that goes into creating flawless finishes. Whether it’s a sleek car part or a beautifully finished piece of furniture, flow coaters ensure that everything gets a smooth, even coat—every time. So next time you admire a perfectly coated surface, give a nod to the flow coater, quietly working its magic behind the scenes.
What Equipment & Components are There in the Flow Coating System?
Flow coating systems are intricate assemblies designed to apply uniform coatings to a variety of substrates. These systems comprise several critical components that work together seamlessly to ensure precise and consistent coating applications. Now, follow us as we explore the basic equipment and components that make up a flow coating system.
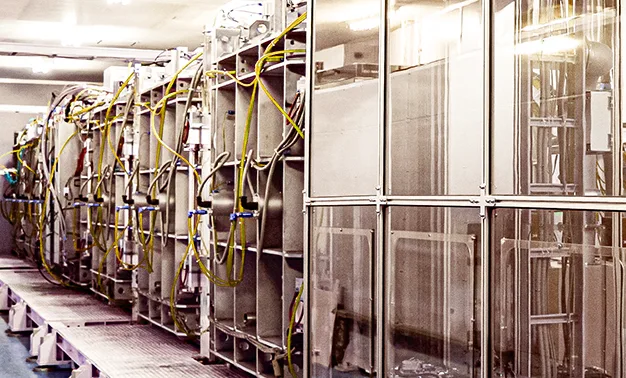
Flow Coating Equipment system
- Flow Coater:The flow coater is the heart of any flow coating system. This machine is responsible for actually applying the coating material to the substrate. Depending on the type of flow coater (dip, spray, curtain, or tilt), these flow coating devices vary in design and operation.
- Reservoir:The reservoir is where the coating is stored before it is applied to the substrate. It must be designed to maintain the consistency of the coating and prevent contamination. Reservoir materials are often compatible with the coating to prevent reactions. Some reservoirs also include temperature regulation to maintain the optimal viscosity of the coating.
- Pumps and Piping: The pump and piping system is critical to transport the coating from the reservoir to the flow coater. A high-quality pump is essential to maintain consistent pressure and flow rate, and the transfer piping needs to be designed to minimize turbulence and prevent clogging. These components ensure a steady and controlled flow of material.
- Dispensing nozzles:Dispensing nozzles are commonly found on spray and curtain flow coaters. Dispensing nozzles play a key role in determining the accuracy and uniformity of coating application. Different types of nozzles are used depending on the specific requirements of the coating process.
- Conveyor system:Modern flow coating systems are equipped with advanced control systems. Real-time monitoring of flow rate, temperature and other key parameters combined with a programmable logic controller (PLC) allows the operator to monitor and adjust various parameters for precise control of the coating process. These control systems are commonly used in semi-automatic and automatic flow coating equipment to achieve the best coating results. Detailed flow coating equipment types CoatingsDirectory are explained in the following article.
- Drying and curing chambers: After the coating is applied, the substrate needs to be dried or cured to ensure that the coating material is properly cured. Heat, UV light or other evaporation methods using drying and curing chambers are integral to achieving this.
- Control systems:Modern flow coating systems are equipped with advanced control systems. Real-time monitoring of flow rate, temperature and other key parameters combined with a programmable logic controller (PLC) allows the operator to monitor and adjust various parameters for precise control of the coating process to achieve the best coating results.
- Filtration system: Filtration systems are essential for removing impurities and particles from the coating material to ensure a smooth and flawless surface. There are two types of filtration components that are often used: One type is located in the piping system to capture contaminants. The other type is located in the reservoir to maintain material purity.
Table of Components and Their Functions | ||
---|---|---|
Component | Function | Operation Suggestions |
Flow Coater | Applies coating material to the substrate. | Select the type (immersion, spray, curtain, tilt) based on application needs. |
Reservoir Tank | Stores coating material, maintaining consistency and purity. | Ensure material compatibility and maintain temperature control if needed. |
Pumps and Piping | Transport coating material from the reservoir to the coater. | Use high-quality pumps and design piping to minimize turbulence and clogs. Maintain flow control and avoid bubbles or splashing as the coating flows onto the parts. |
Dispensing Nozzles | Control precision and uniformity of coating application. | Adjust nozzles for desired spray pattern and flow rate. |
Conveyor System | Moves substrates through the coating process. | Maintain consistent speed and ensure substrates are securely held. |
Drying/Curing Chambers | Dry or cure the coated substrate. | Match drying/curing method to the coating material requirements. |
Control Systems | Monitor and adjust coating process parameters. | Use programmable logic controllers (PLCs) for precise automation. |
Filtration Systems | Remove impurities from the coating material. | Regularly check and replace filters to maintain material purity. Sufficient turnover should be provided to adequately filter the coating solution. |
Understanding the components and equipment that make up a flow coating system is crucial for appreciating the complexity and precision involved in the coating process. From the flow coater to the control systems, each component plays a vital role in ensuring that substrates receive a consistent, high-quality coating. By diving into the intricacies of these systems, we gain a deeper appreciation for the engineering and technology that bring flawless finishes to life.
What Are The Types of Flow Coating Equipment?
- Manual Flow Coating Machines Manual flow coaters are the simplest type and are typically used for small-scale operations or specialized applications. They require an operator to manually control the flow of coating material and the movement of the substrate. In a manual flow coater, an experienced operator carefully directs the coating material onto the substrate, ensuring that every inch of the coating is evenly covered.
- Semi-Automatic Flow Coating Machines Semi-automatic flow coaters combine manual control with automated features, balancing precision and efficiency. They typically have an automated conveyor that moves the substrate, reducing the operator’s workload. The operator adjusts the flow of coating material for optimal results. It’s like a sous chef assisting the head chef, automating repetitive tasks while still allowing for expert oversight.
- Fully Automatic Flow Coating Machines Fully automated flow coaters are designed for high-volume production lines. These machines handle the entire coating process, from loading the substrate, precisely applying the coating material, to curing the coated product – all at the touch of a button. Little to no human intervention is required.
- Specialized Flow Coating Machines Specialty flow coaters are designed for specific applications or unique substrates. These machines may have unique features such as temperature control, multi-layer coating capabilities, or the ability to handle high-viscosity materials. Imagine a tailor crafting a custom suit, meticulously adjusting every detail for a perfect fit. Specialty flow coaters are designed to meet the unique needs of a specific application, ensuring that the coating process is perfectly adapted to the substrate and material being used.
Features | Detailed |
---|---|
Precise Control | Operators have direct control over the coating process, allowing for precise adjustments. |
Flexibility | Ideal for small batches and custom coatings. |
Cost-Effective | Lower initial investment compared to automated systems. |
Features | Detailed |
---|---|
Increased consistency | Automated elements ensure a more uniform coating. |
Increased throughput | Faster than manual systems and suitable for medium-scale production. |
Ease of use | User-friendly interface for easy operation. |
Features | Detailed |
---|---|
Efficient | Able to quickly coat a large number of substrates. |
Consistency | Provides highly uniform coatings with minimal variation. |
Integrated | Can be integrated into existing production lines for seamless operation. |
Features | Detailed |
---|---|
Customized | Tailored to specific coating requirements. |
Advanced features | May include precise temperature control, multi-layer coatings, and more. |
Versatility | Can handle a wide range of materials and substrates. |
4 Main Types of Flow Coaters.
Flow coating machines, or flow coaters, are essential in various industries for applying uniform coatings. Among the diverse types of flow coating equipment, immersion flow coaters, spray flow coaters, curtain flow coaters, and tilt flow coaters each have unique characteristics and applications. Let’s delve into the specifics of these four types and understand how they work their magic.
- Immersion Flow CoatersImmersion flow coaters are designed for simplicity and effectiveness, particularly in applications requiring complete coverage. These machines are perfect for items that need a thorough, uniform coating, such as metal parts and electronic components. The immersion method ensures that every nook and cranny of the substrate is coated, providing excellent protection and durability.You can also learn all about immersion coating equipment in our corresponding blog.
Industrial dip Flow coating equipment in operation
How it works: Think of an immersion flow coater as a luxurious spa bath for the substrate. The process starts with completely immersing the substrate into a tank of coating material (similar to the dip coating process, right?). During the immersion process, the coating material envelops the entire surface. The substrate is then slowly lifted up to allow the excess coating to flow out, resulting in a smooth, even coating. This method is particularly effective for achieving consistent coverage on complex shapes and hard-to-reach areas. - Spray Flow CoatersSpray flow coaters are versatile and precise, making them ideal for applications that require controlled coating thickness and specific coverage patterns. These machines use nozzles to apply coating material, with adjustable spray patterns and flow rates to suit a variety of substrates and coating requirements. Get an inside look at the relationship between spray system machines, equipment, and parts.
Jet Spray Flow Coaters
How it works:Imagine a skilled painter meticulously applying a fine mist with a spray gun to achieve a perfect finish. In a spray flow coater, coating material is atomized through a nozzle and applied in a controlled manner to deposit an excess of liquid coating (usually water-based and solvent-based paints) onto the substrate. The spray can be adjusted to ensure even coverage and desired thickness, making it suitable for large areas and intricate details. Flow coaters, combined with spray methods, are ideal for achieving fine, smooth finishes. - Curtain Flow CoatersCurtain flow coaters are known for their efficiency and high-speed application, making them a popular choice in industries like furniture manufacturing and large-scale production lines. These machines create a continuous “curtain” of coating material that flows over the substrate, ensuring a consistent and uniform layer.
Curtain Flow Coaters
Working Principle: Visualize walking through a curtain of water at an amusement park—every part of you gets wet uniformly. In a curtain flow coater, the coating material flows from a reservoir and is spread evenly through a narrow slit, creating a continuous curtain. The substrate passes through this curtain, receiving a uniform coat as it moves along the production line. This method is highly efficient for coating flat or slightly contoured surfaces with speed and consistency. - Tilt Flow Coaters
Tilt flow coaters are specialized machines designed for substrates that benefit from controlled angle coating. By tilting the substrate during the coating process, these machines ensure an even application, particularly useful for items that need multi-angle coverage without pooling or uneven distribution.
Working Principle: In a tilt flow coater, the substrate is positioned at an angle and gradually tilted while the coating material flows over it. This controlled movement ensures that the coating spreads evenly across the surface without excessive buildup. This technique is especially useful for achieving uniform coverage on irregularly shaped or multi-dimensional objects.
Flow coating equipment, from immersion to tilt flow coaters, each offers unique advantages tailored to specific coating needs. Understanding the characteristics and working principles of these machines helps in selecting the right type for your application, ensuring high-quality, consistent coatings every time. Whether it’s the thorough coverage of immersion coaters or the precise application of spray coaters, these machines play a vital role in the manufacturing process, bringing both efficiency and perfection to the art of coating.
How to Maintain and Troubleshoot Flow Coating Equipment?
Maintaining and troubleshooting flow coating equipment is essential to ensure its longevity and optimal performance. Whether you’re dealing with a flow coater, flow coating machine, or an entire flow coating system, following a comprehensive maintenance routine can prevent costly downtime and ensure consistent coating quality. From routine cleaning to upgrading components, keep your flow coating equipment in top condition.
Aspect | Details | Description |
---|---|---|
Daily Cleaning & Maintenance (Routine maintenance is fundamental to the proper functioning of your flow coating system) | Cleaning the Flow Coater | Clean at the end of each day with appropriate solvents to prevent clogs and ensure unobstructed nozzles and dispensing components. |
Inspecting the Reservoir Tank | Check for contamination or sediment buildup. Regularly drain and clean the tank to maintain coating material purity. | |
Checking Pumps and Piping | Inspect for leaks, cracks, or blockages. Ensure secure connections and clean/replace filters to maintain proper flow rates. | |
Verifying Conveyor Systems | Ensure smooth operation, free of obstructions or misalignments. Lubricate moving parts regularly to ensure consistent substrate movement. | |
Routine Inspections (Routine inspections are critical to catching potential issues before they become major problems) | Nozzle Inspections | Inspect nozzles for wear and tear. Replace damaged or worn-out nozzles to maintain precise and consistent coating applications. |
System Calibration | Periodically calibrate the system, checking flow rates, pressure settings, and temperature controls for optimal performance. | |
Software Updates | Keep control systems and software up to date with manufacturer-released updates to improve system performance, address bugs, and enhance features. | |
Troubleshooting Common Issues (Even with regular maintenance, problems can occur. Knowing how to troubleshoot common problems can reduce downtime) | Uneven Coating | Check for clogged or damaged nozzles, correct substrate positioning, and consistent flow rate. Adjust conveyor speed and inspect pump pressure settings. |
Coating Buildup | Thoroughly clean equipment, check for residues causing buildup, and ensure coating material viscosity is appropriate. | |
Pump Failures | Check for blockages, ensure the pump receives power, inspect internal components for wear, replace damaged parts, and lubricate regularly for smooth operation. | |
Upgrades and Component Replacement (Over time, it may be necessary to upgrade or replace components to maintain optimal performance and take advantage of new technologies) | Upgrading Nozzles | Consider upgrading to the latest nozzle technology for improved precision and reduced material waste. |
Replacing Worn Parts | Regularly replace worn-out parts such as seals, gaskets, and filters to prevent leaks and ensure consistent performance. | |
Integrating Advanced Control Systems | Upgrade to more advanced control systems for enhanced precision, efficiency, better monitoring, automation, and integration capabilities. |
Maintaining and troubleshooting your flow coating equipment is essential for ensuring long-term reliability and high-quality coatings. From daily cleaning to routine inspections and strategic upgrades, each step plays a crucial role in the overall performance of your flow coating system. By following these guidelines, you can keep your equipment running smoothly, reduce downtime, and achieve consistently excellent results. So, treat your flow coating system with care, and it will reward you with flawless finishes and reliable performance.
How to Choose the Right Flow Coating System?
Choosing the right flow coating system can revolutionize your manufacturing process. With so many options—immersion flow coaters, spray flow coaters, curtain flow coaters, and tilt flow coaters—how do you determine which flow coater is best for your needs? Let’s take a look at the key factors to consider when choosing the perfect flow coating system for your application.
Understand Your Application Needs
The first step in choosing the right flow coating system is to thoroughly understand your specific application needs. Here are some critical questions to ask:
- What is the substrate material?
Different materials, such as metals, plastics, and ceramics, have distinct coating requirements. For instance, immersion flow coaters are ideal for complex metal parts, while spray flow coaters are great for delicate electronic components. - What is the desired coating thickness and uniformity?
If your application requires precise control over coating thickness, spray flow coaters might be your best bet. For uniform coverage over large, flat surfaces, curtain flow coaters are highly efficient. - What are the production volume and speed requirements?
High-volume production lines benefit from the speed and consistency of fully automatic systems like curtain flow coaters. On the other hand, smaller operations might find manual or semi-automatic systems more suitable.
Evaluate Coating Material Compatibility
The type of coating material you plan to use significantly influences your choice of flow coating equipment. Some materials (such as thick resins or adhesives) may require specialized equipment with robust pumping and dispensing capabilities.
So, always check the compatibility of the flow coater with your specific coating. Some machines are better suited for high-viscosity materials, while others excel with low-viscosity coatings.
Consider the Complexity of the Substrate
The shape and complexity of your substrate play a crucial role in selecting the right flow coating system.
- Immersion Flow Coaters are excellent for substrates with intricate shapes and hard-to-reach areas, ensuring complete coverage.
- Spray Flow Coaters offer flexibility and precision for substrates with complex geometries or fine details.
- Curtain Flow Coaters are perfect for flat or slightly contoured surfaces, providing a continuous, uniform coat.
- Tilt Flow Coaters are ideal for multi-dimensional substrates, ensuring even coverage without pooling.
Assess Automation and Control Features
The level of automation and control you need depends on your production scale and quality requirements. Fully automatic systems provide consistent results with minimal manual intervention, ideal for large-scale operations. Semi-automatic and manual systems offer more flexibility and control, suitable for smaller batches and custom applications. Advanced Features to Look For:
- Programmable Controls: Ensure precise control over coating parameters.
- Adjustable Nozzles and Dispensers: Allow customization of spray patterns and flow rates.
- Integrated Drying/Curing Systems: Enhance efficiency by streamlining the entire coating process.
Factor in Maintenance and Operational Costs
Consider the long-term maintenance and operational costs of the flow coating equipment. Machines with complex mechanisms might require more frequent maintenance, while simpler systems could be more cost-effective over time.
Choose equipment from reputable manufacturers who offer comprehensive support and readily available spare parts. This can significantly reduce downtime and maintenance costs.
Consider User Reviews and Testimonials
Real-world experiences from other users can provide valuable insights into the performance and reliability of different flow coating systems. Look for reviews and testimonials from businesses similar to yours to gauge the satisfaction and potential issues with specific equipment.
Pro Tip: Pay attention to both positive and negative feedback. Consistent praise for ease of use and reliability can be a strong indicator of a good investment, while recurring complaints might signal potential problems.
Examine Case Studies and Success Stories
Case studies offer detailed insights into how specific flow coating systems have been implemented in various industries. These success stories can highlight the practical benefits and potential challenges of different equipment, helping you make a more informed decision.
Let’s say you’re a furniture manufacturer. You’ve seen some of your peers increase productivity by 30% and reduce paint waste by 20% when they switched to curtain flow coaters. These case studies can give you specific insights into how this equipment will perform in your operation.
Plan for Future Scalability
Your flow coating system should not only meet your current needs but also accommodate future growth. Opt for equipment that allows easy upgrades and scalability, ensuring it can adapt to increased production demands or new applications.
Selecting the right flow coating system requires careful analysis of your specific application needs, substrate complexity, coating material compatibility, automation requirements, long-term costs, and future expandability potential. By understanding these factors and the previous understanding of the different types of flow coaters, you can make comprehensive, informed decisions that will improve production efficiency and product quality.
Whether you are a small flow coating shop seeking precise manual control or a large flow coating equipment manufacturer requiring high-speed automation. You can find the flow coater that is right for you through the CoatingsDirectory platform. I wish you happy coating!
What are the Environmental Considerations of Flow Coating?
We have looked at the types of flow coating equipment that are common in everyday life and how to choose the right flow coater for your needs. As we strive for a more sustainable future, it is crucial to consider the impact of the manufacturing process on the environment. So, what environmental awareness should be possessed when implementing the flow coating process? Let’s explore how to make this process greener and more environmentally friendly.
- Eco-friendly coating options:
First and foremost, choosing the right flow coating coating material can significantly affect the environmental footprint of flow coating. Choosing eco-friendly coatings, such as water-based or low-VOC (volatile organic compound) coatings, can reduce harmful emissions and improve air quality. These flow coatings are like the environmental warriors of the paint world, fighting pollution layer by layer! - Waste management and disposal:
Effective waste management is another important aspect of eco-friendly flow coating. Implementing a recycling system for excess flow coating materials can minimize waste. In addition, properly disposing of hazardous waste ensures that harmful materials do not enter our landfills or water systems. Think of it as giving your waste a second chance instead of letting it become a villain for the environment. - Regulatory compliance and standards:
Complying with environmental regulations and standards is not only a legal obligation, but also a commitment to sustainable development. Regulations such as the EPA guidelines on hazardous waste and volatile organic compound emissions set the benchmark for responsible practices. By complying with these standards, companies can ensure that they are not only compliant with legal regulations, but also environmentally conscious. It’s like playing by the rules in the green manufacturing game. - Energy Efficiency:
Reducing energy consumption during the flow coating application process is another important environmental consideration. By adopting energy-efficient equipment and practices, the flow coating process can be optimized to reduce energy consumption. For example, using advanced drying systems that require less heat can reduce energy consumption. It’s like upgrading from a gas-guzzling car to a sleek, efficient electric car. - Other Environmental Considerations:
In addition to these major factors, companies involved in the flow coating industry can also explore sustainable product packaging, reduce plastic use, and implement more environmentally friendly transportation methods to transport flow coating products. Every small step of progress will have a greater impact, just like adding a drop of water to an ocean of positive change.
In summary, environmental considerations for flow coating include a range of factors, from choosing environmentally friendly coatings and handling waste to complying with regulations and improving energy efficiency. By adopting these practices, we can ensure that our flow coating process is not only effective, but also environmentally responsible. So let’s apply our products with care and with every coat, we can make a step towards a greener future. After all, the planet deserves a smooth, even coat of love and respect!
In summary, understanding the types and components of flow coating equipment as well as proper maintenance and troubleshooting practices are essential to achieving the best results. By considering environmental impacts, you can make sustainable choices. For more information and to find industrial flow coating service providers and equipment manufacturers, visit coatingsdirectory.com and use our filter tools to simplify your search.
Can you paint over flowcoat?
Yes, you can paint with any paint system over flowcoat. But proper surface preparation is key. To apply flowcoat, clean the surface thoroughly, sand lightly with fine sandpaper, apply a primer, and then paint as usual. This ensures good adhesion and a smooth surface.
Can you sand and polish flowcoat?
Of course, you can sand and polish flowcoat to achieve a glossy finish. Sanding and polishing flowcoat requires using increasingly finer sandpaper, followed by a polish. This process removes imperfections and enhances the gloss.
How thick is flowcoat?
Flow coating is typically applied at a thickness of 0.3 – 1.5mm.
The thickness of the flow coating depends on the specific requirements of the application and the type of coating material used. For most uses, a thickness of approximately 300 microns provides adequate coverage and protection. For heavy duty or highly exposed surfaces, thicker coatings may be required to ensure maximum durability and performance.
What factors affect flow coating thickness?
Several factors affect flowcoat thickness, including viscosity, pull-off speed, and environmental conditions. Flowcoat thickness depends on the viscosity of the paint, the speed of the substrate being pulled out, ambient temperature, humidity, substrate surface, and the flow rate of the paint. Proper control of these factors ensures that the desired coating thickness is achieved.