Are you confused about porcelain coating, is it the same as enamel coating? The answer is: No. They represent two different coatings. Today, follow me to learn more about the characteristics and applications of porcelain coating to help you make the right choice.
What is porcelain coatings?
If you’ve ever admired the smooth, shiny finish of a bathtub, sink, or even some cookware, you’ve most likely seen porcelain coating. Porcelain coating is a borosilicate glass coating that can be applied in liquid or powder form and fused to metal or ceramic surfaces through a high-temperature process. More than just a decorative effect, this coating protects surfaces from wear, corrosion, and extreme temperatures.
An all-rounder in the coatings industry, porcelain coatings have a lot on their plate:
- Porcelain coatings form a tough, glass-like coating that resists scratches, abrasions, and impacts.
- These coatings can withstand temperatures up to 1000°F without cracking or breaking.
- Porcelain coatings resist rust and chemical reactions, and remain intact even in harsh, wet environments.
- Porcelain coatings are smooth and non-porous, making them less susceptible to stains, water spots, and bacteria.
- Beyond their technical benefits, porcelain coatings also have a lustrous, vibrant aesthetic appeal that adds a touch of sophistication to everyday items.
Porcelain coating is used in a variety of places in life due to its super high aesthetic appeal and durability.
- Cookware and cookware: Go to the kitchen and see mom’s favorite Dutch oven or cast iron skillet with a shiny and colorful surface. That’s where porcelain coating comes in. It’s safe for food, non-reactive, and ideal for withstanding high-heat cooking.
- Bathroom fixtures: The non-porous nature of porcelain coating makes sinks, bathtubs, and toilets stain-resistant and easy to clean after years of use.
- Home appliances: Porcelain coating can give appliances a smooth polish that matches the modern aesthetic while protecting metal parts from moisture and wear.
- Industrial equipment: In industries such as chemical processing and manufacturing, porcelain coating can improve the resistance of machinery to corrosion, heat, and wear.
- Art and design: Porcelain coating can also be used in artwork, jewelry, and high-end decorative items. Its smooth, shiny appearance adds a touch of luxury.
Color | Description | Common Uses |
---|---|---|
White | A classic, clean, and timeless color that enhances brightness and creates a hygienic appearance. | Bathtubs, sinks, toilets, cookware, and home appliances like stoves and washing machines. |
Black | A sleek and modern choice that conveys sophistication and durability. | High-end cookware, industrial tools, and luxury bathroom fixtures. |
Blue | Often used in shades like light blue or navy for a calming and elegant look. | Decorative sinks, vintage-style cookware, and artistic installations. |
Green | Typically in earthy or pastel tones for a natural, soothing aesthetic. | Retro-inspired appliances, eco-themed products, and artistic designs. |
Red | A bold, vibrant color that stands out and adds energy to designs. | High-end cookware, decorative items, and accent bathroom fixtures. |
Gray | A neutral, versatile option for modern and industrial aesthetics. | Appliances, industrial equipment, and minimalist decor. |
Yellow | Bright and cheerful, often used to add warmth and personality to spaces. | Retro cookware, artistic pieces, and vibrant bathroom accessories. |
Brown | Earthy and rustic, offering a traditional or vintage appearance. | Cookware, fireplaces, and decorative outdoor items. |
Gold | A luxurious, shiny color that adds a touch of elegance and exclusivity. | Premium cookware, decorative tiles, and high-end bathroom or kitchen fixtures. |
Multicolor | Often a blend of vibrant shades to create unique, eye-catching patterns. | Artistic designs, decorative items, and specialty cookware. |
How Does Porcelain Coating Differ from Enamel Coating?
We’ve found that quite a few people often confuse porcelain coating and enamel coating in daily communication. People use the two terms interchangeably, thinking they refer to the same coating. But here’s the thing: while they have some similarities (both create a smooth, durable surface that’s usually shiny and easy to clean), they are not the same substance. This confusion is understandable, especially since both coatings are widely used on cookware, appliances, and bathroom fixtures. However, there are clear differences in terms of materials, application methods, and performance. Now, follow me to break it down in detail so you don’t confuse the two again in the future.

How Does Porcelain Coating Differ from Enamel Coating
Material Composition
Porcelain coating is made of glass powder that is fused to the metal or ceramic surface at high temperatures to form a smooth, non-porous, and hard glass-like coating.
Enamel coating also uses powdered glass, but includes other additives such as pigments, resins, and activators to help produce different colors and finishes (click to view enamel coating composition and types of knowledge).
Application Process
Porcelain coatings require extremely high heat (usually over 1500°F (800°C)) to melt glass powder into the surface, creating an even, glossy coating. View Guide to Applying Porcelain Coatings.
Enamel coatings, on the other hand, are more flexible in application and can be applied in layers by spraying or dipping and then baked in an oven. This method is suitable for uneven or complex surfaces and has a wide range of uses. While both coatings are thermoplastics, enamel coatings are slightly less durable than porcelain coatings in high-pressure environments.View Guide to Applying Enamel Coatings.
Durability:
Porcelain coatings are ideal for coating ovens, bathtubs, and industrial tools because of their hardness, heat resistance (withstanding temperatures over 1000°F without degradation), and resistance to scratches, stains, and chemicals.
Enamel coatings, while more durable than regular oil-based paints, are more likely to chip or wear over time than porcelain coatings, especially under impact or rapid temperature changes.
Appearance:
The smooth, glass-like surface of porcelain coatings offers an elegant look that is perfect for items that are both aesthetically pleasing and functional, such as sinks and high-end cookware.
Because enamel coatings are more diverse in composition, they can end up in a wide variety of colors and textures, ranging from glossy to matte. Therefore it is often chosen for decorative purposes.
Porcelain Coating vs. Enamel Coating Applications | ||
---|---|---|
Category | Porcelain Coating Applications | Enamel Coating Applications |
Cookware & Bakeware | High-heat cookware like Dutch ovens, broilers, and pizza stones. | Decorative plates, mugs, and lightweight cooking pans. |
Bathroom Fixtures | Durable sinks, bathtubs, and toilets with stain and water resistance. | Custom-colored fixtures for aesthetic appeal in less-used areas. |
Home Appliances | Ovens, stovetops, and grills with high-temperature requirements. | Refrigerators and washing machines with colorful, glossy finishes. |
Industrial Tools | Heat-resistant shields, chemical-resistant machinery components. | Machinery casings or tools requiring branding or color coding. |
Art & Design | Sculptures or installations needing a glossy, long-lasting finish. | Jewelry, decorative panels, and artistic items with vibrant colors. |
Architectural Use | Wall tiles, building facades, and surfaces exposed to extreme weather. | Interior design accents like custom wall art or signage. |
Medical Equipment | Sanitary equipment like sterilizers and diagnostic tool surfaces. | Color-coded instruments for easy identification. |
Automotive | Exhaust systems and engine parts requiring heat and corrosion resistance. | Car body panels with custom colors or branding designs. |
I believe that with such a detailed explanation, you can already tell the difference between porcelain coatings and enamel coatings. If you value long-term durability, heat resistance, and a clean, classic appearance, porcelain coatings are the first choice for you. If versatility, color options, and decorative appeal are more important in a century application, then enamel coatings may be a better choice. The next time you see someone arguing about the two, you’ll have the confidence to explain them correctly.
How to Choose the Right Porcelain Coating for Your Project?
Now that you have thoroughly understood the porcelain coating, it is time to make a choice. Oops, this can be an overwhelming part for those who have difficulty making choices, especially when there are so many options. I believe you have been like me before: staring at a large number of choices on the shelf, wondering which one is really suitable for my needs. In fact, we only need to focus on a few key factors to make an informed decision.
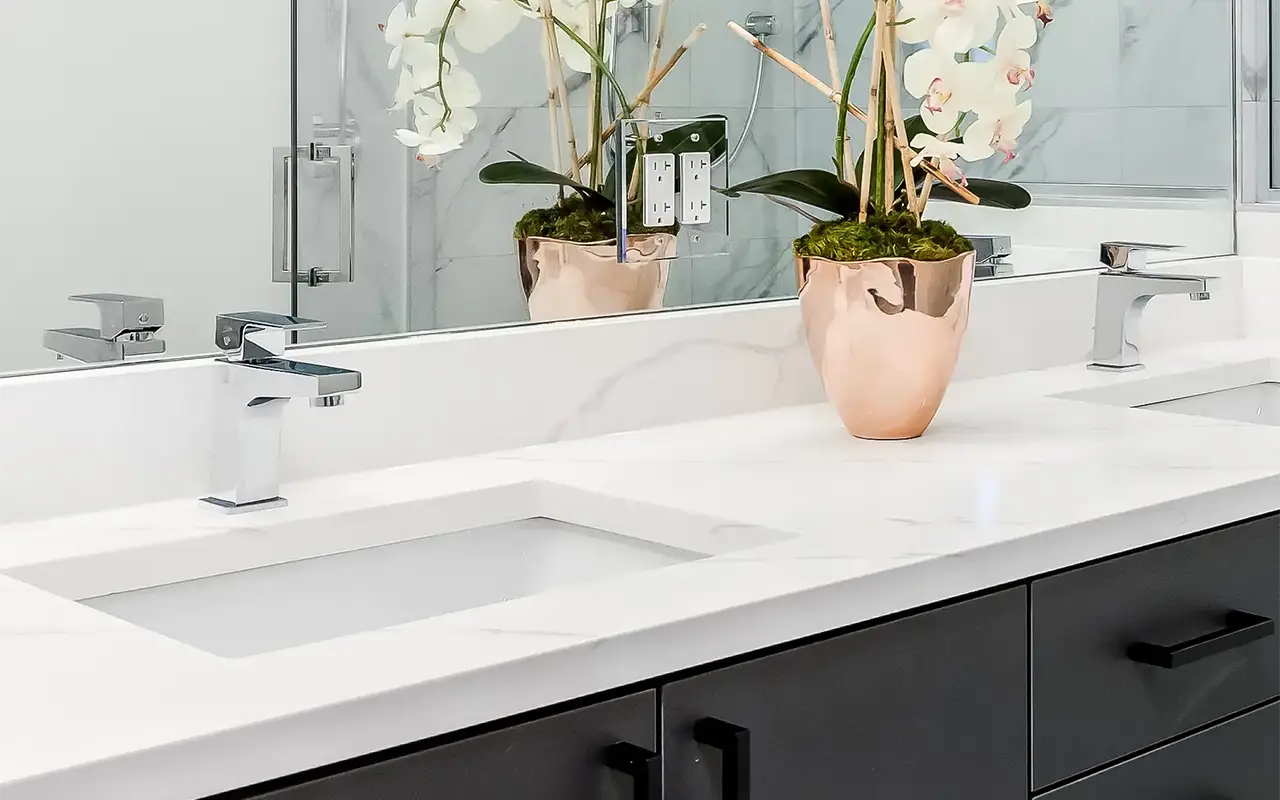
Porcelain coating applied to porcelain
First, ask yourself: what do I want to paint where, and what effect do I need to achieve? Determine the purpose of the coating to have a more specific direction. If you are coating cookware, you need a food-safe (FDA-compliant) and heat-resistant porcelain coating. For bathroom fixtures, prioritize stain resistance. For industrial projects, durability and chemical resistance should be the top considerations.
Once you have determined the purpose of the coating, you need to consider the type of substrate you are coating. If you are applying porcelain coating to metal surfaces such as steel and cast iron, adhesion and rust resistance are key. For ceramic or glass substrates, it is recommended to choose a porcelain coating that can enhance durability and will not crack under heat or pressure.
If you are unsure about the compatibility of the coating and the substrate, ask the salesperson standing next to you immediately. A quick question can save a lot of trouble.
If the environmental conditions you plan to paint are special, such as high humidity, high temperature, chemical exposure, etc., it is very important to fully consider the challenges that the coating will face in the future. Targeted selection of porcelain coatings with specific functional eccentricities combined with the environment can ensure a longer service life.
Don’t forget aesthetic preferences, which I think is the most interesting part. Porcelain coatings are available in a variety of colors, finishes and gloss levels for us to choose from. We can make a decision based on our own or our family’s preferences that everyone is satisfied with. It is worth noting that different gloss levels have different characteristics-
- Glossy finishes are easier to clean and highly reflective, but scratches may be more obvious.
- Matt finishes are sophisticated and modern, but are more difficult to keep spotless.
It is important to know that choosing porcelain coatings is not just about choosing the “best” coating, but choosing the coating that is best for you. Don’t rush, take a moment to consider the purpose of your project, the substrate, the environment, and your hobby style. Ask for help when necessary, coating manufacturers and suppliers usually have a wealth of knowledge that they will be happy to share. Or you can go to forums like Reddit or Quora to find people’s experiences summarizing the above.
Even if you are new to porcelain coating, don’t worry too much. Feel free to try it, because porcelain coating supports renovation, even if you are not satisfied with the first coating effect, you can always start over.
What Factors Affect Porcelain Coating Cost?
When I first got quotes from porcelain coating service companies, my biggest question was, “Why do costs vary so much?” It turns out there is no one-size-fits-all answer. The cost of porcelain coating is determined by a variety of factors, including the type of coating, coating thickness, surface prep, coating process, complexity of the item being coated, quantity, special features, etc. Only by considering them can you calculate a specific cost.
- Material Quality: Higher-quality porcelain coatings are more durable, heat-resistant, and more beautiful, but they also cost more. If durability is not a primary concern, you can save money by choosing a standard-grade porcelain coating.
- Coating Thickness: Thicker coatings provide better protection, but they require more material and take longer to process. The corresponding costs also increase because they consume more resources and time.
- Surface Preparation: Before applying porcelain, the substrate needs to be cleaned, treated and even sandblasted to ensure proper adhesion of the coating. The complexity of this preparation stage varies: smooth metal surfaces can be prepared in a short time, while rusted or uneven surfaces require additional care.
- Application method: Depending on the project requirements, porcelain coatings can be applied using different methods, such as electrostatic spraying or dipping. Different processes have their own costs.
- Objects to be painted: The size and complexity of the items being painted directly affects the cost. Larger items require more materials and time, while intricate shapes or details may require additional precision and labor.
- Production volume: Do you need to paint one item or 1,000? Benefiting from economies of scale, industrial painting service providers can control individual costs lower in batch painting projects.
- Special features: If you have additional unique requirements for porcelain coating effects, such as color customization, high-gloss finishes, or added durability features, costs will increase.
- Labor costs: The labor costs of applying porcelain coatings vary by country, region, and even specific company. For example, painting in high-cost areas may charge more. It is recommended to compare quotes from different suppliers, but don’t be too obsessed with chasing the lowest price. Balancing cost and quality is the most important thing.
Understanding the factors that affect the cost of porcelain coating can help you make more informed decisions for your project. Whether it is balancing quality and budget, choosing the right application method, or simplifying the design, there is always a way to optimize costs without sacrificing performance.
Are you surprised by what you learn! This is what we have learned during our time in the coatings industry. Stay tuned for more professional guidance. If you are planning a porcelain coating project, you can use the CoatingsDirectory platform to filter out the coatings companies that best meet your desired goals for subsequent cooperation negotiations.
What are porcelain coatings used for?
Porcelain coatings are great for cookware, utensils, bathroom ceramics, architectural panels, and signage. They are often used to protect surfaces from wear, corrosion, and heat while adding a smoother, glossier finish.
Can I repair or reapply damaged porcelain coatings?
Yes, but it’s tricky. Small breaks can be repaired, but large-scale damage usually requires a complete refinish. Porcelain coating damage is often accompanied by some chipping of the underlying porcelain. If you want to repair the underlying chipped porcelain as much as possible, you’ll need caulk, porcelain filler, or touch-up paint to replace the lost material. Click here for more detailed instructions on repairing porcelain coatings.
Is porcelain-coated cookware safe?
Yes, modern porcelain-coated cookware is safe as long as it is used properly. Porcelain coatings create a non-reactive surface, so they won’t leach chemicals or metals into food. But be careful with scratches – damaging the coating can expose the metal underneath, which can affect safety.
How do you tell the difference between porcelain coatings and enamel coatings?
Porcelain coatings tend to be smoother and glossier, while enamel coatings may be slightly textured or matte. If you are still unsure by eye, check the product details or consult the manufacturer.