You may often be promoted by car washes to use ceramic coatings to enhance the brightness and durability of your car paint. Ceramic coating is indeed a good thing, but it is not limited to protecting car paint. Due to their unique composition, they can be made into ultra-strong protective coatings and are widely used in modern industry and everyday life.
What is Ceramic Coating?
Some people may think that ceramic coating is a fancy term or marketing gimmick to distinguish it from porcelain coating. In fact, it is more than that. Ceramic coating is a measurable layer of silicone, siloxane or other chemicals that can bond to the surface of various substrates to form a tough, glass-like protective coating.
Ceramic coatings are mainly made of nanotechnology materials, containing silicon dioxide (SiO₂), silicates (SiO₃) or titanium dioxide (TiO₂). The barrier formed by these compounds is hydrophobic, UV-resistant and anti-oxidant. Unlike wax or sealants, ceramic coatings do not just stay on the surface. Once cured, they will blend with the surface and provide excellent protection from scratches, heat, chemicals and environmental damage, which is used to improve the durability and performance of materials.
Due to their excellent properties, ceramic coatings have been widely used in surface modification over the past few decades. Ordinary people have heard of ceramic coatings the most for automotive use, but in fact their uses are much more extensive. From simple everyday applications (kitchenware and decorative items), to high-tech engineering applications (cutting tools, engines, turbines) to areas such as spacecraft and biomedicine, ceramic coatings can be valued as ideal materials.
According to the use or application conditions, ceramic coatings can be divided into protective coatings (corrosion resistance, wear resistance, high temperature resistance, antifouling/anti-fog electrical insulation coatings), process improvement & control coatings (thermal barrier coatings, neutron Absorptive coatings and performance optical coatings), structural coatings, recycled repair coatings. For example:
- Ceramic coatings can be applied to the exterior of vehicles to reduce the surface friction of vehicle paint and protect the paint from scratches, UV damage and road dirt.
- In manufacturing, ceramic coatings can improve the mechanical properties of metal substrates. Reduce wear and corrosion of base alloy tools and machinery.
- Protects sensitive electronic components from heat and moisture, ensuring optimal performance and extended life.
- Ceramic coatings can be used in spacecraft as coatings with special optical properties, as heat-insulating coatings on internal combustion engine components, and as neutron-absorbing coatings on nuclear components.
- Ceramic coatings are used in the marine industry to protect parts from salt water corrosion.
- Complex thin-walled parts for various applications are manufactured using independent structural coating methods.
- Ceramic coatings are used on non-stick pans, bakeware and even some household appliances to improve heat resistance, ease of cleaning and durability.
- Ceramic coatings protect solar panels and wind turbines from severe weather.
From the perspective of car paint protection, it seems to be similar to graphene coating and wax. But from the perspective of high temperature resistance, it seems to be similar to Teflon coating. But in fact, there are still huge differences between them. Click to see the difference between these coatings to eliminate your confusion.
Currently, as the properties of ceramic coatings develop, their functions become more diverse. It has been widely used in various fields, such as: petrochemical industry, industrial manufacturing, thermal power generation, food production, chemical processing equipment, textile, metallurgy, aerospace, etc. However, for targeted development for specific engineering applications, extensive studies are required to evaluate their microstructural, mechanical, chemical, optical, and biomedical properties.
As a high-performance protective layer, ceramic coating has many outstanding capabilities.
- Ceramic coating has the ability to repel water and any liquid dirt that stays on the surface of ceramic coating.
- Ceramic coating blocks harmful UV rays and prevents oxidation, especially when it comes to protecting surfaces such as car paint to look new for years.
- The ultra-smooth sealing surface of the ceramic coating prevents various salt and acid chemicals found in the natural environment from penetrating and damaging the underlying substrate.
- Strong and wear-resistant, it can protect the substrate from scratches and wear.
- High temperature resistance, can help internal combustion engine components achieve heat insulation.
- The non-stick properties make it harder for dirt to adhere and make cleaning easier.
How is Ceramic Coating Made?
The reason why ceramic coating has these excellent qualities is achieved by carefully mixing various chemical ingredients. In general, these ingredients include:
- Resin– the main polymer material of ceramic coatings, an essential hardening and functional component.
- Solvent– keeps the coating liquid, dissolves and evenly distributes active ingredients during application, and promotes adhesion between the coating and the substrate.
- Additives– any other ingredients added based on actual use requirements (fragrance, color, gloss, special effects).
Resins used in ceramic coatings are primarily silicon-based polymers. Polydimethylsiloxane (PDMS) is the most common resin in ceramic coating formulations because it is non-toxic, inert, non-flammable, optically clear, thermally stable, and UV stable.
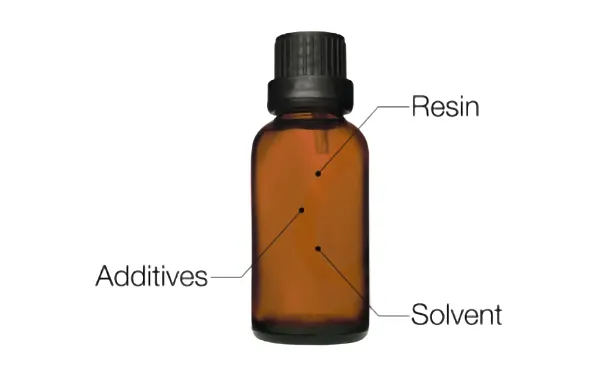
Ceramic Coating Composition
It is precisely because of the unique formula of the ceramic coating preparation process that there are many types of ceramic coatings. However, all ceramic coatings are inseparable from silicon dioxide (SiO₂). This compound is derived from sand or quartz and gives ceramic coatings the “ceramic” properties. SiO₂ particles are very small (nanoscale) and are a very durable material that accounts for a large proportion of ceramic coatings. It has a high melting point and excellent wear and scratch resistance. But SiO₂ alone is not enough, and some formulations also include the following 3 chemical polymer ingredients:
- Titanium dioxide:Titanium dioxide is another common ingredient in ceramic coatings. It provides UV protection and helps prevent the coating from yellowing over time.
- Zirconia:To increase the resistance of ceramic coatings to UV radiation, zirconia is often used in the composition of ceramic coatings along with titanium dioxide. It also helps increase the hardness of the coating, making it more resistant to damage.
- Aluminum Oxide:Aluminum oxide provides excellent wear resistance and also contributes to the hardness and overall durability of ceramic coatings.
It is through the careful blending of these chemical ingredients that ceramic coating products are made to perform in their application.
Making Ceramic Coatings.
Diverse ingredients are only the basis for making ceramic coatings, and the preparation process must be very meticulous. From raw material preparation to blending and post-testing, cutting-edge technology and strict quality control are required.
- Preparing raw materials:Start with sourcing pure SiO₂ and TiO₂, usually in powder form. These raw materials are broken down to the nanometer level by nanoparticle technology, which is very important to ensure that the ceramic coating fills the microscopic pores and adheres perfectly to the surface.
- Formulating the Blend:Once the ingredients are ready, manufacturers mix SiO₂ and TiO₂, solvents, polymers and other additives in precisely measured proportions until they find a formula that delivers a targeted level of shine and protection. The mixing process uses industrial mixers with high shear forces to ensure that everything is evenly dispersed.
- Testing and adjustment:Before the coating is ready, serious ceramic coating manufacturers will also have a dedicated testing department to check the hardness, hydrophobicity, UV resistance and durability of the coating under various conditions.
- Packaging:The formulated ceramic coating will be packaged in a sealed container to prevent oxidation.
Finished ceramic coatings are ready for delivery to the end user, and we can use these products to get the desired surface protection. When a ceramic coating is applied to a surface, the catalyst in the mixture begins to solidify with the help of air. Ceramic coatings made with a specific formula bond with the material at the molecular level to form a semi-permanent protective layer. More detailed information on the use of ceramic coating technology can be found in our corresponding blog.
What Types of Ceramic Coatings are There?
Each type of ceramic coating is designed to cope with different usage conditions. There are some for automotive paint protection, some for medical implants, some for industrial manufacturing… Due to the diversity of ceramic coating formulations, there are many names for them in the market. As a professional coatings industry practitioner, I don’t like to classify products by use like ordinary consumers. I am more likely to classify them by analyzing the core components and functions of ceramic coatings.
SiO₂-based ceramic coatings
Ceramic coatings with silica (SiO₂) as the main ingredient are the most common in daily life, especially in automotive paint protection and glass coating applications. These coatings form a strong bond with the surface and provide excellent hydrophobicity, stain resistance and UV protection.
TiO₂-based ceramic coatings
As the name suggests, the main active ingredient of titanium dioxide coatings is TiO₂. Its photocatalytic and self-cleaning properties are outstanding. Effectively decomposes organic pollutants when exposed to ultraviolet light, making it ideal for outdoor applications such as building exteriors and solar panels.
Nano Ceramic Coating
Nanoceramic coatings are made from ultra-fine ceramic particles that can fill microscopic surface defects. Some people in some areas like to call it “9H” ceramic coating. This coating can provide an extremely hard, scratch-resistant coating after curing.
Graphene ceramic coating
Graphene-based ceramic coating is a cutting-edge solution that arranges single-atom-thick carbon layers in a lattice structure. Combining the superior strength and thermal conductivity of graphene with the properties of ceramic, it provides superior durability and water spot resistance. Often used for luxury car paint and electronic product protection.
Ceramic spray paint
Ceramic spray coatings are a fast-applied alternative to traditional ceramic coatings, with liquids loaded with SiO2 or other ceramic nanoparticles. Although not as durable as traditional ceramic coatings, the advantages are that it is economical, easy to apply, and can provide a temporary protective layer.
By classifying ceramic coatings according to their main components, its properties and advantages can be distinguished at a deeper level. Of course, if you don’t want to know too much technical knowledge, you can also classify them according to their functions. As follows:
Differences in Ceramic Coatings Types | |||
---|---|---|---|
Ceramic Coating Type | Functional role | Common Materials | Applications |
Aesthetic Coatings | Smooth, glossy, colorful | Porcelain, Al₂O₃, ZrO₂ | Jewelry, pottery, decorative surfaces |
Wear/Abrasion-Resistant Coatings | Abrasion-resistant, friction-reducing | Al₂O₃, ZrO₂, TiO₂, Al₂O₃-TiO₂ | Industrial tools, machinery |
Corrosion-Resistant Coatings | Corrosion-resistant | Al₂O₃, ZrO₂, MgO, Cr₂O₃ | Marine equipment, pipelines |
Thermal Barrier Coatings(TBC) | Thermal insulation, oxidation resistance | Al₂O₃, ZrO₂, YSZ | Turbines, engines, exhaust systems |
Refractory/Emissive Coatings | Chemically inert, high thermal efficiency | Cr₂O₃, CoO, Fe₂O₃, NiO | Kilns, furnaces, heat shields |
Electrical Insulation Coatings | High dielectric strength | Al₂O₃, SiO₂, Al₂O₃-TiO₂ | Circuit boards, power systems |
Biomedical Coatings | Tissue compatibility, biocompatibility | TiO₂, porcelain | Implants, surgical tools |
When actual consumers purchase ceramic coatings, it is not enough to simply understand the type of ingredients in the coating. It is also necessary to fully consider the actual required coating thickness, performance, price and other aspects to select a suitable ceramic coating.
Future Outlook and Emerging Applications for Ceramic Coatings.
Ceramic coatings are used in a variety of dressings and healing materials in various places and industries, and the future development is also bright. Although it is challenging to develop new ceramic coating materials, developers have been systematically evaluating the possibility of any potential improvements in ceramic coatings.
In recent years, researchers have achieved certain results in innovative ceramic coating materials for biomedical applications. It is believed that ceramic coatings will bloom in medicine in the near future.
Thanks to ceramic coatings, power plant maintenance has become easier and less time-consuming. Ceramic inserts and ceramic-coated cutting tools have increased productivity in machining applications.
Ceramic coatings provide an efficient and easy-to-apply method for decorating the exterior of your vehicle. More protective and cost-effective technologies are still being researched.
I have high hopes for this coating as more and more ceramic coatings are developed for specific applications. If you are ready to find the perfect ceramic coating supplier or industrial partner, our coatingsdirectory.com platform can help you. Whether you need a ceramic coating supplier, industrial batch application ceramic coating services or a specialist factory, our platform is designed to get you connected quickly. If this article has sparked your curiosity, please share your thoughts, experiences or questions in the comments section.
FAQs
Is Ceramic Coating Worth It?
If you value long-term protection and a polished look, ceramic coatings are worth it. Take car paint, for example. Applying a ceramic coating can help the paint resist the elements, including UV rays, dust and corrosive rain. Although there is an upfront cost, it is a smart investment in the long run.
Can ceramic coating prevent scratches?
Ceramic coating can resist minor scratches, but it does not mean that the surface can withstand deep gouges and impacts. They act as a protective barrier to minimize damage from minor abrasions.
Can Ceramic Coatings Be Removed?
Since ceramic coatings are chemically bonded to the surface, they cannot be completely removed by simple cleaning. Ceramic coatings can be 100% removed with the help of polishing or grinding. For more detailed instructions on refurbishing and removing ceramic coatings, please refer to the corresponding blog.
Are Ceramic Coatings Heat Resistant?
Of course! High heat resistance is one of the characteristics of ceramic coatings, which can withstand temperatures as high as 1200°F (650°C) to 2192°F (1200°C), depending on the formulation.