Article Chapters
Have you ever wondered how products achieve that flawless finish, as if touched by a master painter’s brush? Enter the world of roller coaters, the silent champions of coating application. Roller coating is a popular coating application process that combines precision and efficiency, innovation and quality. In this comprehensive guide, we’ll demystify roller coating equipment, from understanding what a roller coater is to exploring the different types available. Join us on this journey as we delve into the heart of roller coating technology and discover the key factors to consider when choosing the perfect roller coater for your needs.
What is A Roller Coater?
A roller coater, also known as a roll coater or coating roller, is a precision machine used to apply liquid paint to surfaces with unparalleled efficiency and consistency.
The working principle of a roller coater is simple yet very effective. It consists of a series of rotating rollers that transfer the paint to the substrate, ensuring even coverage and thickness. Paint is dispensed onto a series of rollers that are designed to control the amount and distribution of paint. The substrate travels between the soft coating roller and the steel roller, where it comes into contact with the coating drum. The coating roller will transfer the coating to the substrate surface (the application roller can be soaked in the coating liquid or extruded through a special die nozzle). This process causes a phenomenon called “film splitting”: the coating on the surface of the roller splits, with part remaining on the roller and part sticking to the surface of the substrate. Finally, a transfer system transfers the coated substrate to an oven where the coating is baked and cured.
Roller coaters can take many forms, from simple paint rollers to complex coaters with multiple rollers. This system is used to coat, print or laminate flat targets (substrates) through a combination of several different rollers to obtain the desired coating surface. One of the main advantages of roller coaters is the ability to achieve efficient, precise and uniform coating thickness. By controlling factors such as roll speed, pressure and coating viscosity, roller coaters ensure consistent coverage of the entire surface of the substrate, resulting in a high-quality coating. If you want to learn more about the professional technical knowledge of roller coating, you can jump to our corresponding blog.
With the development of science and technology, the coating system of the roller can support various coating viscosities and different coating thicknesses by combining a variety of different specialized technologies. Therefore, roller coaters have been widely used in various industrial fields including furniture, food, metal, electronic components, optics, and medicine.
The Importance of Roller Coaters in the Coating Industry:
Roller coaters play a pivotal role in the coating industry, offering unmatched efficiency, reliability, and versatility. Whether it’s applying protective coatings to automotive components, decorative finishes to furniture, or functional coatings to electronic devices, roller coaters excel in a wide range of applications.
Moreover, roller coaters help manufacturers streamline their production processes, reduce material waste, and improve overall product quality. By achieving precise and uniform coating thicknesses, roller coaters ensure consistent performance and aesthetics, enhancing the value and durability of coated products.
What Are the Different Types of Roller Coating Equipment Available?
Roller coating machines come in various types, each with its unique working principles and characteristics. The classification method of roller coating equipment can be classified according to the material state of the roller coating and whether the coating amount is determined before or after roller coating. We’ll delve into the intricacies of different roller coating equipment, providing readers with a detailed understanding of how each type operates and its distinct features.
The open roller coater is a universal method characterized by consisting of a paint reservoir (where the paint liquid is exposed to the atmosphere) and a roller. Let’s explore the intricacies of the open roller coater and how it is revolutionizing surface treatment in industries around the world.
- Gravure Roller Coater: Gravure roller coating equipment utilizes an engraved roller to transfer coating to the substrate. The engraved roller is etched with a precise pattern, allowing it to pick up controlled amounts of paint from the hopper and transfer it to the substrate as it passes through the machine. Gravure coaters are ideal for quickly applying thin, uniform coatings in batch industrial roll coating production; the speed can be adjusted to control coating thickness. Ideal for industries requiring high quality printing or surface finishing such as packaging and electronics.
Gravure Roller Coater principle
- Reverse roller coating equipment: Reverse roller coating machines usually consist of a support roller, a coating roller and a metering roller. The support roller and coating roller rotate in the same direction to transfer the coating fluid to the substrate web. The speed and gap at which the coating and metering rollers rotate determines the coating thickness.
Reverse roller coating equipment principle
Reverse coaters ensure complete coverage, reducing problems related to surface tension. Particularly suitable for substrates with high uniformity requirements and specific adhesion requirements, such as automotive and aerospace components.
Compared to open roller coating systems, closed roller coating systems provide a controlled environment for coatings. It prevents the coating liquid from being exposed to the atmosphere before roll coating, maximizing the consistency of coating quality and the accuracy of the process. Its representative equipment includes: slot die coater and Lip coater.
- Slot-die coater: Die-roller coating equipment uses a precision-engineered slot die through which the coating material is pumped onto the substrate. The slot die controls the flow rate and thickness of the coating to ensure precise application to the substrate surface. At the same time, since the paint is supplied from a sealed tank under pressure, the effect of air on the paint is zero. Slot die roll coating equipment provides unparalleled control over coating thickness and distribution and minimizes coating fluid waste. Ideal for applications requiring consistent and high quality coatings such as electronics, optics and pharmaceuticals.
Slot-die coater principle
- Lip roller coating equipment: Lip roller coating machines use a CNC lip or scraper to control the flow of coating material on the surface of the substrate. The blade gap and angle can be adjusted to achieve the desired coating thickness. Lip coaters are ideal for fine substrates and high-precision applications, and are often used in industries where surface quality and finish are critical, such as aerospace and automotive.
Lip roller coating equipment principle
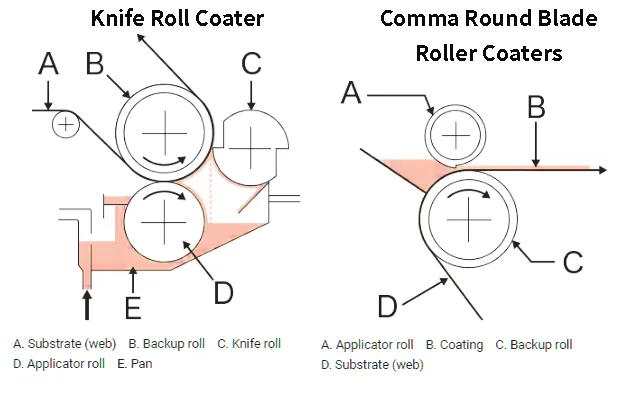
Post metering coater
Post-metered roller coating systems play a vital role in achieving precise coating thickness and uniformity, providing unmatched control of the coating process. Unlike “pre-metering” roller coating systems, where the coating amount is determined at the time of application, post-metering roller coating systems remove excess coating after the coating is applied to achieve the target thickness. The equipment that is widely used include knife roller coating equipment and blade roll equipment.
- Knife roll coater:
Knife roll coating machine uses a metering roller, doctor blade and container to apply coating. Metering rollers pick up coating material from the container and transfer it to the substrate surface, while doctor blades ensure uniform coating thickness by removing excess material. The coating thickness is determined by the gap between the metering roller and the knife roller, so the gap accuracy between different rollers is very important.
Knife coaters are suitable for a variety of coating materials and substrates, making them ideal for applications requiring high-quality finishes and functional coatings, such as woodworking and metal fabrication. - Comma round blade roller coaters:
Comma round blade roller coaters use a curved scraper to apply coating to a substrate and are so named because of their use of round blades or comma blades. The curvature of the blade ensures an even application of coating material, minimizing streaking and overlaying. The amount of removal is determined by the shape of the roller blade and the set gap, allowing precise control of coating thickness and coverage. Comma round knife roller coating equipment is generally suitable for high viscosity coating fluids or forming thick coatings, and is widely used in high-quality finishing industries such as plastics, textiles and packaging.
Others:
In addition to these traditional roll coating equipment types, a variety of other roll coating technologies offer innovative solutions to achieve the required coating performance and finish.
Other roller coater types | ||
---|---|---|
Name Type | Image | Describe |
Bar Coaters | Bar coaters use a series of adjustable bars to apply coating to a substrate. The wand can be adjusted to control coating thickness and distribution, ensuring even coverage of the substrate surface. Bar Coaters offer flexibility and customization of coating applications for a variety of substrates and coating materials. Commonly used in printing, packaging and textile industries. | |
Air knife coating machine | Air knife roller coating equipment uses compressed air to form a thin and uniform film of coating material on the surface of the substrate. The air knife controls the thickness and distribution of the coating, ensuring precise application. Air knife coaters are less affected by substrate thickness or surface unevenness, allowing precise control of coating thickness and coverage. Often used in water-based coatings. | |
Chamber doctor coater | The coating material in the chamber doctor coater is pumped into the chamber (Paint is less volatile and helps maintain the viscosity of solvent-based paints), and is evenly distributed across the entire width of the substrate. A scraper then removes excess coating material, ensuring precise control of coating thickness. The chamber method can be combined with a gravure coater and is commonly used in industries such as flexible packaging, label printing and paper converting. |
The world of roller coaters is diverse and dynamic, with each type of roller coating machine offering unique advantages and capabilities to meet different industry needs and applications. By understanding how each type works and its characteristics, manufacturers can make informed decisions to optimize their coating processes and achieve superior results. Whether it’s the precision of gravure roller coating or the versatility of slot die coaters, roller coating equipment continues to drive innovation and efficiency in the coating industry, shaping the future of surface treatment and product performance. By understanding the different types available, roller coating providers can make informed decisions to optimize their coating process and achieve superior results.
What Are the Main Components of a Roller Coating Systems?
Ever wonder what makes a roller coating system work? Join us on a behind-the-scenes journey to uncover the key components that power these versatile machines. The key components of a complete roller coating system include:
- Components such as rollers,
- Pressure rollers,
- Scraper blades,
- Reservoirs & fluid pumps,
- Slot die nozzles,
- Controllers,
- Conveyor belts.
In addition, some special roller coating equipment may require more unique components.
From the roller to the scraper, each component plays a vital role in achieving a precise and even coating. Let’s take a closer look at how the key parts of a roller coating system work, elucidating its key components and how they contribute to a seamless coating application.
- Rollers: At the heart of every roller coating system lies the rollers themselves. These cylindrical components serve as the primary means of transferring coating material onto the substrate. With their smooth surfaces and precise rotation, rollers ensure consistent coverage and thickness across the entire surface of the substrate.
- Pressure Rollers: Working in tandem with the main rollers, pressure rollers exert uniform pressure on the substrate, ensuring proper adhesion of the coating material. By applying controlled pressure, these rollers help to smooth out any imperfections in the coating and ensure optimal contact between the substrate and the rollers.
- Scraper blade: The scraper blade plays a vital role in controlling the thickness of the coating on the substrate. These blades sit close to the roller and scrape away excess coating material, ensuring that only the required amount is transferred to the substrate. This precise control helps achieve consistent coating thickness and minimizes material waste.
- Reservoirs & Fluid Pumps: Behind the scenes, reservoirs and fluid pumps work together to supply the coating material to the rollers. Reservoirs store the liquid coating material, while fluid pumps regulate the flow rate and pressure, ensuring a steady supply to the rollers. This ensures uninterrupted operation and consistent coating application throughout the process.
- Slot die nozzle: For closed roller coating systems, the slot nozzle (some may be lipped) plays a vital role in controlling the flow and distribution of the coating. These precision-engineered nozzles direct the coating material onto the substrate, ensuring uniform coverage and thickness.
- Conveyors: Last but not least, conveyors provide the substrate with a smooth and stable surface to travel along during the coating process. By ensuring precise movement and alignment, conveyors help to maintain consistent coating application and prevent substrate misalignment or damage.
In summary, roller coating systems are complex and efficient machines that rely on a variety of components to achieve precise and even coating. From rollers and pressure rollers to scrapers and controllers, each component plays a vital role in ensuring optimal coating application. By understanding the inner workings of these systems, the application of the roller coating process can maximize efficiency, minimize waste, and achieve superior coating results.
How to Choose A Roller Coater?
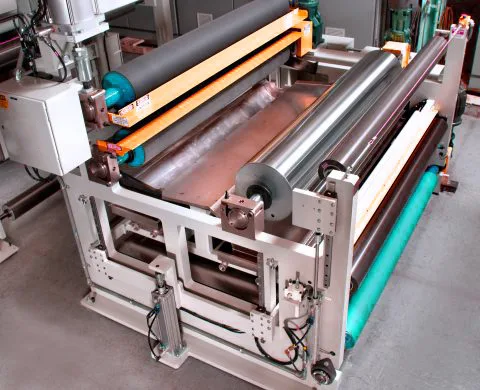
Lip coater live show
Choosing the right roller coater is like finding the right assistant—it requires compatibility, precision, and skill. Careful planning, attention to detail, and a thorough understanding of your needs for a roller coating project will aid in making your choice. Let’s take a look at the key factors to consider when choosing a roller coater to help you find the ideal solution for your roller coating needs.
- Coating Requirements:
Before diving into the world of roller coaters, it’s essential to define your coating requirements. Consider factors such as the type of coating material, desired coating thickness, substrate material, and production volume. Whether you’re applying thin films or thick coatings, understanding your coating needs is the first step towards selecting the right roller coater. - Roller Configuration and Material:
The heart of any roller coater lies in its rollers. Pay close attention to the roller configuration, including the number of rollers, their diameter, and surface material. Choose rollers that are compatible with your coating and substrate, ensuring optimal coating quality and performance. Additionally, consider factors such as roller hardness, surface finish, and temperature resistance to meet specific application requirements. - Coating Patterns and Designs:
Beyond mere functionality, some roller coaters offer the capability to create intricate patterns and designs on coated surfaces. If your application demands decorative finishes or textured coatings, look for roller coaters equipped with specialized pattern rollers or customizable design options. These features add a touch of creativity and versatility to your coating process, opening up new possibilities for product aesthetics and differentiation. - Substrate Size and Compatibility:
Size matters when it comes to substrate compatibility. Before selecting a roller coater, assess the size and dimensions of your substrates to ensure compatibility with the coater’s roller width and clearance. Whether you’re coating small parts or large panels, choose a roller coater that accommodates your substrate size range without compromising coating quality or efficiency. - Application-Specific Requirements:
Different industries and applications have unique coating requirements that demand specialized solutions. Consider factors such as temperature sensitivity, curing methods, and material compatibility when selecting a roller coater. For niche applications such as automotive coatings, food packaging, or electronic components, prioritize roller coaters designed specifically to meet the stringent requirements of these industries. - Precision control and automation:
In the world of roller coating, precision is crucial. Look for roller coaters with advanced control systems and automation features. These include adjustable roll speed, nip pressure and coating thickness control mechanisms. The ability to fine-tune these parameters ensures that the roller coater supports a wide range of coating materials, including solvent-based, water-based and UV-curable formulations. To easily and accurately ensure a consistent and even coating, even on complex or irregular surfaces. - Versatility and Flexibility:
Flexibility is the key to roller coating versatility. Choose a roller coater that offers versatility in coating application techniques, substrate compatibility, and coating material options. Whether you are coating flat surfaces, curved contours or three-dimensional objects, choose a roller coater that can easily adapt to your diverse coating needs. - Ease of maintenance and service:
Smooth operation requires regular maintenance and reliable service support. Choose a roller coater from a reputable manufacturer with a track record of quality workmanship and responsive customer service. Prioritize roller coaters with user-friendly maintenance features such as quick-change rollers, convenient cleaning mechanisms and comprehensive training resources. Click to explore the guide to daily use of a roller coater. A well-maintained roller coater ensures consistent performance and extends equipment life, minimizing downtime and maximizing productivity.
In summary, choosing the right roller coater requires a balance between technical considerations and practical needs. By carefully evaluating factors ranging from coating pattern and substrate compatibility to specific application requirements and maintenance considerations. By taking a comprehensive approach and carefully evaluating every aspect of the coating process, you can confidently select a roller coater that meets your needs and drive your coating operations to new heights of efficiency and excellence. So lace up your shoes and move forward with confidence, knowing that your journey to coating success is guided by the perfect roller coater assistant.
As we conclude our exploration of roller coating, it’s clear that this technology holds immense potential for enhancing coating applications across various industries. By understanding the types of roller coating equipment, the components of roller coating systems, and the factors to consider when choosing a roller coater, you’re well-equipped to make informed decisions for your coating projects. Remember, for further assistance and to connect with reputable roller coating service providers and roller coating manufacturers, visit coatingsdirectory.com and utilize our advanced filtering options. Here’s to rolling towards coating success with confidence and clarity!
What is the difference between slot die coating and blade coating?
Slot die coating and knife coating are both methods of applying thin films to substrates, but there are significant differences in their mechanics and application techniques.
Blade coating (also called blade coating or doctor blade coating) utilizes a blade or scraper to apply coating material to a substrate surface. The blade acts as a barrier, controlling the thickness of the coating as it passes over the substrate. Blade coating is versatile and cost-effective for a variety of applications including paper and packaging, textiles and adhesive coatings.
In contrast, slot-die coating involves the use of narrow slot-shaped orifices close to the substrate surface. The coating material is pumped through a slot die and flows onto the substrate by gravity or pressure. The slot-die does not influence the thickness of the wet coated layer via any form of destructive physical contact or scraping, and the method allows precise control of coating uniformity, making it suitable for high-precision applications such as electronics manufacturing and thin film deposition.
How Do Roller Material and Nap Length Impact Coating Performance?
The roller material and nap length play crucial roles in determining the coating performance of roller coaters.
Roller material refers to the material composition of the rollers used in the coating process. Common roller materials include rubber, stainless steel, and various polymer compounds. Each material offers different properties such as hardness, resilience, and chemical resistance, which can affect coating adhesion, uniformity, and durability. Selecting the appropriate roller material is essential to achieve the desired coating quality and performance.
Pile length refers to the length of fibers or bristles on the surface of the drum. The thicker the nap or length of fabric, the more paint a roller will hold. The result is a thicker coating, but also a slightly rougher surface. On the other hand, the shorter the nap, the less paint the roller can hold and the finer the coating thickness control, making it suitable for precision coating applications. Selecting the appropriate pile length depends on the coating requirements and the desired coating thickness.
What Are the Latest Advances in Roller Coating Machinery and Systems?
The roller coating industry is witnessing continuous advancements in machinery and systems aimed at improving efficiency, precision, and sustainability.
- One notable advance is the integration of digital technologies such as automation, data analytics, and machine learning into roller coating systems. These technologies enable real-time monitoring and control of coating parameters, resulting in enhanced process optimization, reduced material waste, and improved quality control.
- Another trend is the development of eco-friendly coating solutions and equipment. Manufacturers are increasingly focused on reducing environmental impact by utilizing water-based coatings, solvent-free formulations, and recyclable materials. Advanced filtration and recovery systems further minimize waste and promote sustainability in roller coating operations.
- Furthermore, innovations in roller design, such as precision-engineered rollers with customizable surface properties, are enhancing coating performance and versatility. These advancements allow for precise control over coating thickness, surface finish, and adhesion, enabling manufacturers to meet the diverse needs of their customers across various industries.
Overall, the latest advances in roller coating machinery and systems are driving industry progress towards more efficient, sustainable, and high-quality coating solutions, paving the way for continued innovation and growth in the field.