Industrial coatings are protective overcoats applied on materials to provide them durability, protection from various corrosion threats, and other environmental factors. They play a pivotal role in protecting the equipment, infrastructure, and facilities, as well as assist in the continued long-term service of products. While industrial coatings are more concerned with protection than decoration, have no fear, an industrial coating can still look good. Now let’s discuss the main industrial coatings which are in widespread use, and the technologies and trends we believe will continue to transform this innovative sector.
What are industrial Coatings?
Industrial coating is used to protect the surface from wear and corrosion. These coatings increase surface durability and aesthetic appearance. Industrial coatings are complex protective systems applied to industrial assets to protect and extend the service life of pipelines, heavy equipment, storage tanks, bridges and structural steel against extreme environmental and mechanical exposure conditions. For instance, together with the excellent durability and toughness, and other performance properties that are needed to survive harsh conditions, industrial coatings are multifunctional, unlike paints used in a house or architecture, which offer primarily aesthetic benefits and such uses have lower weather resistance characteristics.
Coatings are meant to survive challenging circumstances such as corrosive substances, chemicals, UV light, moisture, mechanical stress, along with quick changes in temperature from burning hot to cold. They are designed to do more than simply cover a surface; they are to protect and preserve the integrity of a structure from the effects of erosion and the hazards of operation that are ever-present in this beautiful Gulf of Mexico.
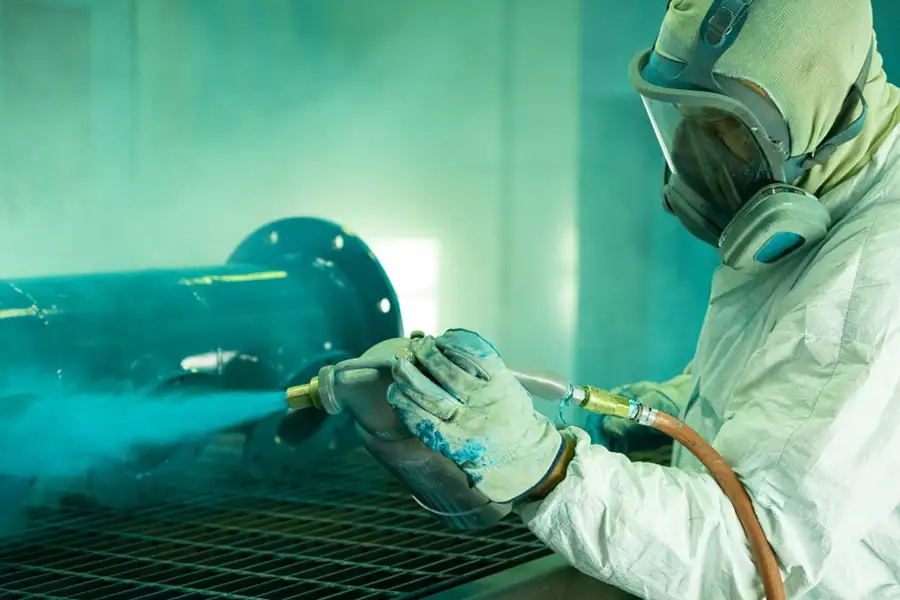
Powder Industrial Coating
With high-tech resins, higher-solid glass, and a multitude of additives, industrial coatings build thick and strong films on top of the surface. These coatings require surface preparation by cleaning, degreasing, blasting, and scheduling the application process to be done in a controlled environment. This method ensures the highest level of adhesion, perfect film buildup, and consistent performance over the entire substrate.
In contrast, architectural coatings are free of complexity, either water or oil-based and single-component products designed for ease of application. They are aesthetically deliberate, primary enhancers designed to tie all elements of colour together and give some basic protection to the surface at painted residential and commercial structures when applied by brushes or rollers. Unlike in industrial scenarios, these coatings don’t provide chemical durability, physical impact resistance, and the strength that is essential over a period. While low-gravity applications might benefit from economical architectural paints, those sectors would experience accelerated failure under load, leading to costly repairs, safety hazards, or equipment failure.
Industrial coatings may initially seem more expensive (due to complicated formulations designed for specific environments and the need for certified installers), but they provide far superior lifecycle value. Not only does their durability, adaptable nature to extreme conditions and low maintenance needs reduce downtime and repairs, but it also prolongs the life span of the asset, resulting in long-term savings.
In essence, industrial coatings are not merely a new layer on top of something. It safeguards and shines a light on vital treasures. From protecting a factory floor against spills, to shielding a bridge from corrosion keeping a chemical tank intact, industrial coatings are the keys holding today’s modern industry together when it comes to reliability and efficiency.
How They Differ from General-Purpose Coatings?
Aspect | Function‑Driven Industrial Coatings | Aesthetic‑Driven Architectural Paints |
---|---|---|
Core Objective | Shield against corrosion, chemicals, abrasion, heat, and fire | Provide colour, surface finish, and basic weather protection. |
Performance Requirements | Engineered for harsh exposures: marine, chemical, high‑traffic, high‑temp environments | Suitable for moderate indoor/outdoor use, weather and fade resistance |
Product Formulation | Complex, multi-component systems with specialised chemistries and performance modifiers | Simpler resin systems, typically single-component and user-friendly |
Durability & Longevity | Long service life under aggressive conditions; minimises maintenance intervals | Moderate lifespan, requiring periodic repainting |
Application Complexity | Requires industrial protocols (e.g., surface blasting, multi-layer systems) | Straightforward methods—brushing, rolling, spraying; DIY‑friendly |
Cost Profile | Higher initial cost → offset by long-term asset preservation | Lower upfront cost; shorter lifespan increases repaint frequency |
What are the Benefits Of Industrial Coatings?
Industrial coatings are essential across industries to protect investments by ensuring a seamless operation, aside from enhancing safety and sustainability programs. A closer look at these core benefits is as follows:
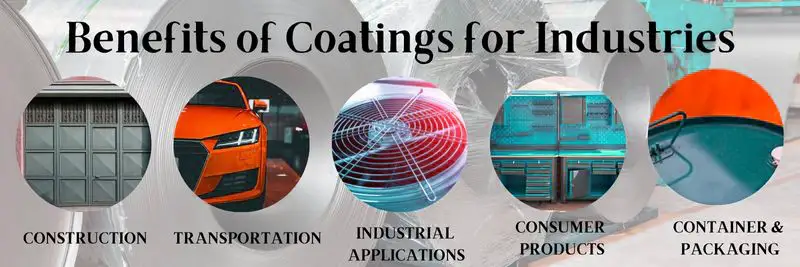
Benefits Of Industrial Coatings
Corrosion Protection
Epoxy and polyurethane coatings have been carefully engineered to absorb all mechanical impact and preserve machinery floors and structural components far and wide. Friction or impact present in heavy-duty industrial conditions demands protection against surface wear, so constant mechanical pressure acts on surfaces.
Abrasion and Wear Resistance
Surfaces in high-traffic and heavy-duty industrial applications are subject to constant friction, impact, and wear. Epoxy and polyurethane coatings are designed to endure these forces, as they keep the surface intact even under constant mechanical stress. That helps machines, floors, and a building structure to be durable, limiting downtime from subsurface deterioration or equipment breakdown
Chemical Resistance
It is important in factories or workplaces to protect workers as well as machinery from potentially hazardous substances and environments. The surfaces were designed to have layers of coatings that can provide a certain level of protection against acids, alkalis, polar organic compounds and hazardous residues. This protection encompasses the surface integrity and contamination prevention of critical sectors, including manufacturing, food processing, pharmaceutical production, and water treatment.
Temperature and Heat Resistance
Some industrial processes an extreme temperatures such as heat or cold, on various surfaces and equipment. Ceramic, silicone, and fluoropolymer-based coatings have high resistance to thermal degradation and can be used under high or changing temperature conditions. These surfaces are perfect for use in high-temperature manufacturing, energy production, exhaust ducts, and cold-storage spaces. Flame-retardant coatings also expand in high temperatures to create thermal insulation, providing an additional level of fire protection.
Enhanced Safety
Coatings represent a significant addition to workplace safety. Surfaces that are designed to be non-slip help to minimise slips in wet or greasy areas, whereas coatings that are flame-retardant slow down the spread of fires, which gives people time to evacuate when incidents occur. Low-visibility surfaces increase the risk of an accident; therefore, safety coatings improve hazardous awareness, and in marking walkways, exits, or dangerous hardware. These traits help achieve safety compliance and minimise crash-related exposure.
Improved Aesthetics and Branding
Coatings provide protection, but also contribute to the beauty of industrial places. By using a range of colours, finishes, whether that be gloss, matte or textured, and designs, companies can create a cleaner, more professional appearance to their assertion space. A company identity can be reinforced by incorporating custom colours and branding aspects into the coating style, which in turn can improve employee morale in the workplace.
Low Maintenance and Easy Cleaning
The surfaces that are coated are comparatively easier to maintain by resisting dirt, dust, oils, and contaminants. This means faster cleaning turnaround and less time spent closing the premises for sanitation or repairs. The ease of cleaning helps in regulated environments, such as food processing, healthcare, and pharmaceutical manufacturing, where hygiene standards and operational efficiency both need to be maintained.
Electrical Insulation and Low Friction
A certain type of coating is designed not just for protection but for functional performance. Electrical insulating coatings may prevent static electricity buildup and short circuits in sensitive equipment. Others reduce friction to provide low-friction, non-stick surfaces, something vital to components like conveyor belts and valves and many moving assemblies. Such functional improvements upgrade the safety and performance of automated or high-tech facilities.
Cost Savings and Operational Efficiency
Industrial coatings reduce total operating costs through minimisation of wear, corrosion, and maintenance. The equipment is durable, the output is high, and the downtime is less. Additionally, thermal barrier coatings can also help conserve energy due to better insulation, along with lesser heating or cooling expenditures, which is another type of coating that indirectly contributes to energy conservation. In the long run, these efficiencies stack up to a reduction in costs and greater ROI.
Environmental and Regulatory Benefits
Industrial coatings are widely used, but more and more often, they are formulated with sustainability in mind. Low VOC (volatile organic compound) and powder coatings contribute to reducing harmful emissions to help businesses comply with environmental regulations. Innovations such as low solvent consumption and low energy curing, as seen within the launch of water-based or UV-cured nanocoatings, are now helping to ameliorate key points through reducing the solvent used alongside addressing energy consumption of industrial operation, creating a green initiative that aligns automation processes and increasing environmental impact score.
Industrial coatings are not merely a coating over steel or concrete; they are a first line of defence, a safety device, a performance enhancement and more and more a sustainability aid. When the right ones are selected and used correctly, they will do much more than just prolong the life of a building or a machine; they will prevent accidents, reduce downtimes, save energy and keep processes operating in the most rigorous conditions. Now, let’s look at some of the types of industrial coatings.
What Are The Types Of Industrial Coatings?
Industrial coating plays an essential role in preventing damage to equipment and infrastructure due to weather, chemicals, and normal wear and tear. Even the most robust structures can collapse early without proper coating, which translates into high repair costs, downtime, and safety hazards.
Industrial coatings are not only for aesthetics; they offer the necessary protection against environmental conditions. Our team’s examination of 37 coating failures last year revealed a striking pattern – 85% of cases resulted from three fundamental errors. First, many operators used generic coatings unsuitable for extreme environments, leading to premature breakdown. Second, proper surface preparation, like sandblasting, was frequently overlooked, compromising adhesion. Third, decisions are based solely on upfront cost rather than lifecycle analysis. Let’s look at the coatings that go beyond just doing the job and actually keep your assets safe and operational.
Epoxy Coating
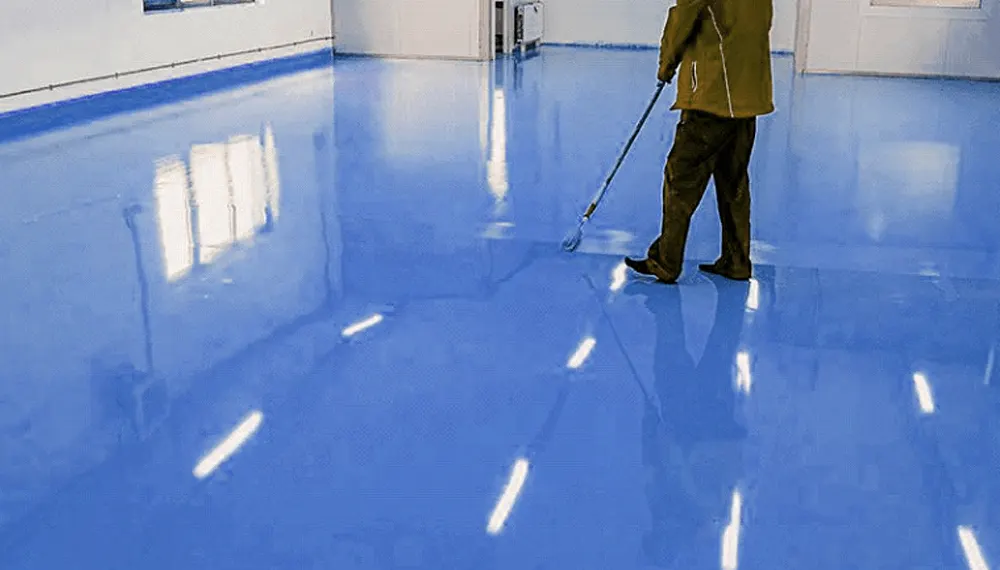
Epoxy paint
Epoxy coatings are made by mixing a resin with a hardener to create a very durable, chemical-resistant coating. When this coating is applied and cured, the epoxy will create a firm protective film that provides greater resistance against abrasion, corrosion, and chemical attack. It has good adhesion to metal, concrete, wood, and some plastics, but bad adhesion with silicones and vinyls. Many epoxies also provide for aesthetic variety with different colours and finishes. They are used for automotive parts, ship hulls, pipelines, and factory floors. But diligent surface prep and breakdown over long UV exposure are drawbacks.
Polyurethane Coating
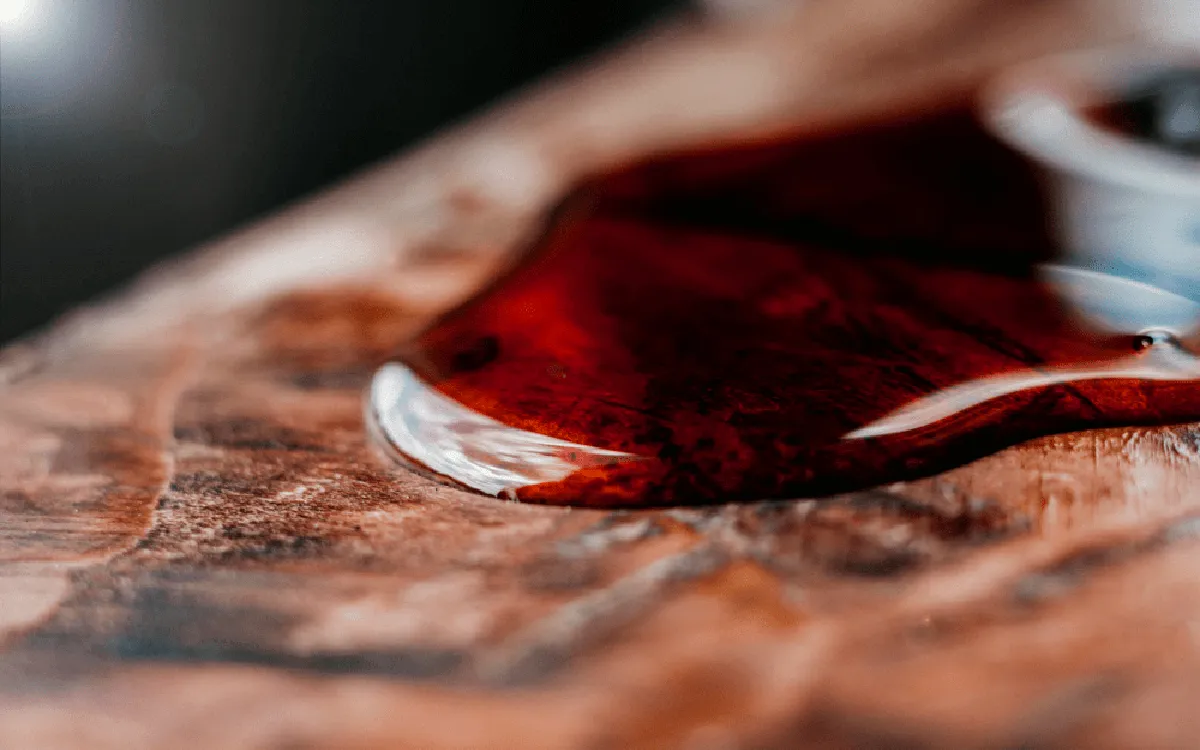
Polyurethane polymer paints type
These types of coatings harden by means of a chemical reaction between a polyol or polyamine and an isocyanate, typically a relatively small body polymer. For example, such coatings supply a tough yet pliable film, exhibiting excellent chemical, abrasion, and environmental resistance. The composition of the paints also adds flexibility to the surface, allowing it to expand and contract with the underlying material which leads to less cracking or peeling. On a positive note, polyurethane is much better than epoxy with UV, which is much higher in quality, and will not fade or degrade outside. It’s extensively applied in automotive, aerospace, construction, and marine industries. Polyurethane may be harder than conventional varnishes, but the right recipes will also hold less impact and yellow over time.
Polysiloxane Coating
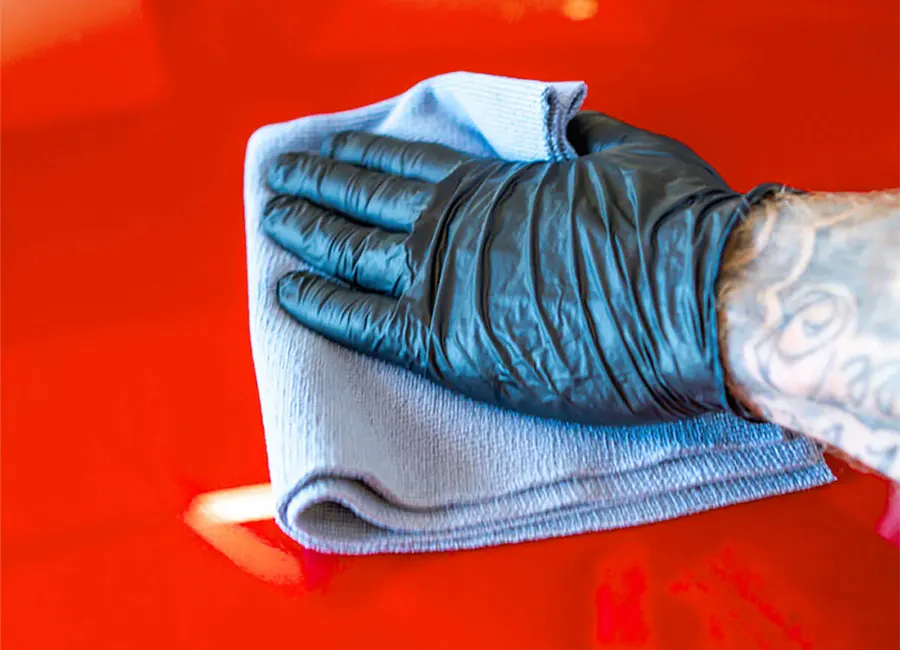
Polysiloxane Coating
Polysiloxane coatings are advanced hybrid coatings, combining the best characteristics of epoxy and polyurethane systems with exceptional UV and weathering performance. They consist of silicon-oxygen chemical structures that form a strong, flexible, and permanent barrier film. The resist is coated with, resist that can withstand chemical attack, moisture and thermal variations, enabling it to perform very well in hot conditions like spans, platforms offshore and wind turbines. Their adaptive nature and heat resistance till about 300°C make them a top choice for bodies subjected to varying environmental forces. But because of their advanced makeup, they are pricier than conventional coatings and will become brittle over time.
Zinc-Rich Coating
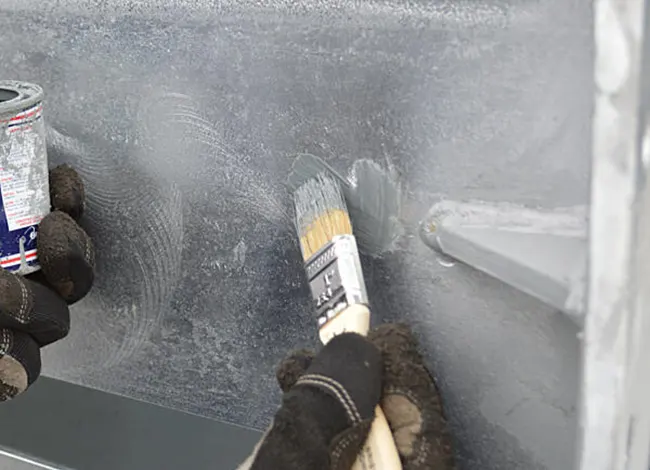
Zinc-Rich Coating
A further level of sacrificial corrosion protection is achieved by combining high levels of zinc particles in the formulation against galvanised coatings. The zinc, when applied to metal substrates like steel sheet, acts as a sacrificial anode and oxidises instead of the substrate. So, even if the coating does get scratched, you still have protection from the film below. Galvanised coatings are frequently utilised as primers for other covered systems in addition to the coatings alone in marine, construction, and automotive environments. These types provide decent electrical conductivity and average heat resistance. They are strong and cost-effective, but need maintenance in harsh environments, and as they oxidise, they may become dull and take on a lesser quality aesthetic appearance.
Ceramic Coating
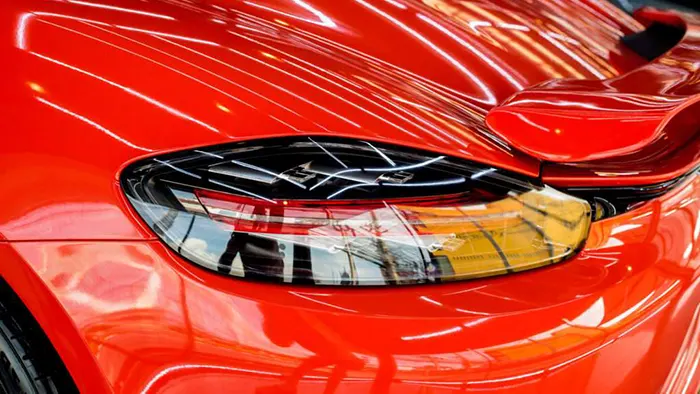
Ceramic coating on car lights & glass
Ceramic coatings are high-performance finishes that are able to withstand very high temperatures (in most cases, over 1000°C), especially when applied through thermal spraying or by spin coating, producing an inert hard surface with wear, corrosion, and chemical resistance. Ceramic coatings are most commonly used to help efficiency by reducing friction and thermal conductivity (used in automotive, aerospace, medical, and food industries). These hydrophobic traits prevent oxidation and accumulation on surfaces. However, they are generally costlier to apply and need specialised, accurate instruments. Moreover, ceramic coatings may also crack under special mechanical stresses or impacts.
Metal Surface Treatment
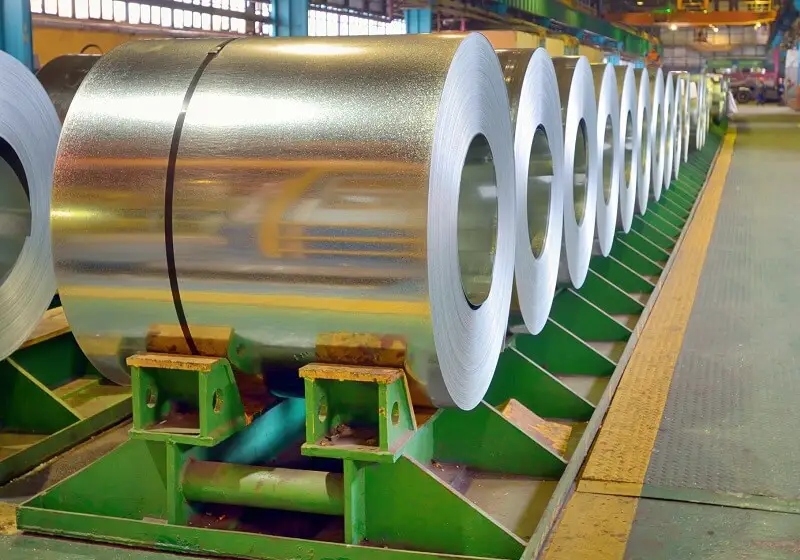
Metal Surface Treatment
Surface treatments, where one or more layers of protective metal like aluminium, nickel or chromium, for instance, are deposited over the bulk material, can create surface properties with improved corrosion resistance, emissivity, microhardness or electrical conductivity, to name a few advantages. The metallurgical film is generally firmly adhered using high-velocity oxy-fuel spraying or electroplating techniques. However, these surface modifications are typically leveraged in harsh industrial environments, such as gas turbines, boilers, and jet engines, which subject materials to arduous high-temperature conditions. Similar metallurgical surface treatments are also used for electronic devices, medical instruments and spacecraft. Though as durable and functional as metal coatings are, these may need to be reapplied from time to time. The ability to adhere to specific substrates is also an issue in materials (still an open question/challenge).
Intumescent Coating
Intumescent coatings are special fire-protection finishes which swell up more than one hundred times their original thickness when exposed to flames or intense heat. When it expands, it creates a dense, foamy insulating layer that protects the steel skeleton, as well as other materials, from the high temperatures. It acts as a thermal barrier and allows for the preservation of the component bonding through fire. These types of coatings are of utmost importance when it comes to building construction, like fire-rated walls, ceilings, and steel skeletons. Best of all, they will typically be applied with ordinary spray (or brush) techniques to the wear areas and be matched to the architectural design aesthetic. Their superior fire protection properties are invaluable (though unfortunately can require up to yearly inspection and environmental control to prevent degradation of intumescent coatings from the elements).
Teflon Coatings
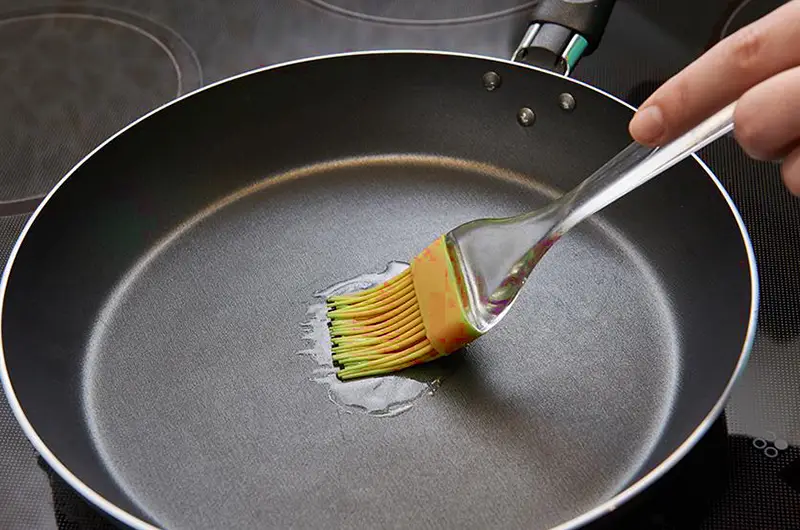
Teflon Coatings
Teflon (PTFE and other fluoropolymers) coatings are well-known for their non-stick, low-friction properties and resistance to chemicals and high temperatures (up to 260°C or 500°F). They are suitable in situations where lubrication is unwanted or where deposition should not be allowed, e.g. cookware, moulds, bearings, and processing equipment. Teflon coating is also of very good dielectric strength and therefore can be utilised in electrical applications.
Powder Coatings
Powder coatings are dry, free-flowing powders, electrostatically applied and cross-linked by heat to form a hardened coating. They are environmentally friendly as they are VOC-free and have high chipping, scratching, corrosion, and fading resistance. Powder coatings, which are widely applied on metal surfaces, such as the bodies of automobiles, outdoor furniture, and home appliances, are available in an array of colours, finishes, and textures, and are extremely durable in the long term.
Nitrocellulose Coatings
Nitrocellulose lacquer is a fast-drying lacquer-type coating commonly found in the wood and musical instrument industries. They give a high gloss, transparent or colored finish that brings out the beauty of wood grain. Although they can be easily applied and repaired, they are not as durable as modern coatings, as they are vulnerable to heat, moisture, and solvents. They are also less environmentally safe due to their flammability and VOC content, and therefore, proper ventilation and safety precautions are necessary.
Fluoropolymer Coatings
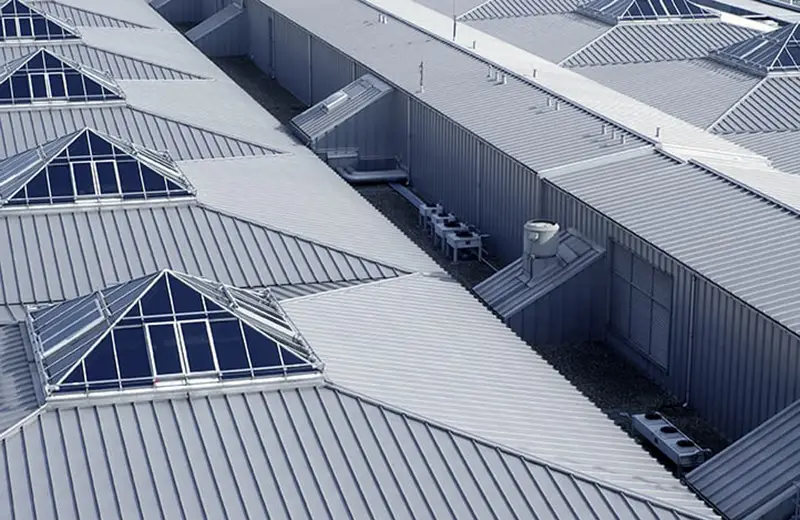
Roofs coated with fluoropolymer coatings
Coatings such as fluoropolymer (PTFE, FEP, PFA) are highly prized due to their chemical inertness, UV resistance, low surface energy, and high weatherability. These coatings are used in architectural panels, offshore structures, pipelines and aerospace applications where long-term performance in aggressive environments is necessary. They are very stable in colour, corrosion resistant and have minimum surface build-up, even under extreme conditions.
Classification of Industrial Coatings by Composition, Application, and Performance.
Coating Type | Material Composition | Application Scenarios | Characteristics & Performance |
---|---|---|---|
Epoxy Coating | Epoxy resin + hardener (amine or polyamide) | Industrial floors, marine vessels, pipelines, machinery, and automotive chassis | High chemical and abrasion resistance, excellent adhesion, moisture-proof, not UV-stable, rigid and requires detailed surface preparation |
Polyurethane Coating | Polyol/polyamine + isocyanate | Automotive exteriors, aircraft surfaces, concrete floors, and marine structures | UV-resistant, flexible, chemically stable, available in glossy finishes; may yellow over time; does not absorb heavy impact |
Polysiloxane Coating | Silicone-based hybrid polymer (silicon-oxygen backbone) | Offshore platforms, bridges, tanks, wind turbines | Excellent UV and weather resistance, long service life, flexible, low VOC; higher cost; can become brittle over time |
Zinc-Rich Coating | High zinc content (powdered zinc + binder) | Structural steel, ship hulls, bridges, automotive underbodies | Sacrificial corrosion protection (galvanic action), adheres well to metal; limited UV and chemical resistance, may require touch-ups |
Ceramic Coating | Inorganic ceramic powders + polymer or thermal spray matrix | Turbines, high-speed machinery, circuit boards, medical tools, food-grade surfaces | High-temperature resistance (up to 1000°C+), chemical and scratch resistance, hydrophobic; brittle and expensive, needs specialised application methods |
Metallic Coating | Pure or alloyed metals (e.g., aluminium, nickel, chromium) via plating/spraying | Gas turbines, medical implants, electronics, reflective components | High conductivity, strong corrosion resistance, surface hardness; not suitable for non-metals; requires regular maintenance in harsh conditions |
Intumescent Coating | Carbon-rich polymers with intumescent agents (e.g., ammonium phosphate) | Fire-rated building elements, structural steel in commercial and public buildings | Expands up to 100x under high heat, forms an insulating char layer, delays structural failure in fires; must be maintained; sensitive to moisture and damage |
Teflon (PTFE) Coating | Fluoropolymers (PTFE, FEP, PFA) | Cookware, moulds, bearings, processing equipment, and electrical components | Non-stick, low-friction, chemical/high-temp resistant (260°C), excellent dielectric strength; limited mechanical durability. |
Powder Coating | Dry thermoplastic/thermoset powders | Automotive bodies, outdoor furniture, and appliances | VOC-free, high chip/scratch/corrosion/fade resistance, wide colour/finish options; durable but requires heat curing. |
Nitrocellulose Coating | Nitrocellulose + solvents | Wood furniture, musical instruments | Fast-drying, high-gloss transparent/colored finish; highlights wood grain; flammable, poor heat/moisture/solvent resistance, high VOC. |
Fluoropolymer Coating | PTFE, FEP, PFA, etc. | Architectural panels, offshore structures, pipelines, aerospace | Chemically inert, UV/weather-resistant, low surface energy, colour-stable, minimal buildup, high cost. |
Industrial Coating Market Trends.
The industrial coatings industry is rapidly evolving, driven by increasing societal demands for sustainability, advances in technology, and new trends in the global economy. While market forces may evolve as manufacturers and consumers adjust to environmental policies, functional demands, and geopolitical instability, certain defining tendencies are taking shape to characterise the market through 2025 and beyond.
The Shift Toward Sustainable Solutions
Support for eco-friendly options is driving a shift across the board to avert volatile organic compound emissions and dangerous substances. As a result, waterborne, high-solids, and powder coatings are becoming increasingly popular.
- Waterborne coatings: The minimal solvent content and better convenience make waterborne coatings a favourite for both architectural painting and general industrial use.
- Powder coatings: Powder coatings are becoming increasingly popular in heavy machinery, home appliances, and automotive components as they are entirely solvent-free and mostly recyclable while remaining thermally durable and environmentally friendly, ideal for a sustainable assembly line.
- High-solids coatings: High-solids coatings, which strike a balance between application and environmental concentration, regularly allow for a thicker film build along with a reduction in applications and a decrease in operational energy consumption costs.
While this pattern emerges the most in Europe and North America, where restrictions are often the most complex, India and other industrialising countries are among the fastest rising markets for these applications.
Smart Coatings and Functional Innovation
One of the most important developments involves smart and overall functional coatings designed to respond adaptively to environmental changes or to better protect beyond the general performance.
These coatings are being developed with features such as:
- Self-healing capabilities that automatically repair microcracks,
- Antimicrobial and anti-corrosive properties for healthcare and marine sectors,
- Anti-icing and anti-fouling surfaces for aerospace and offshore use,
- Embedded sensors or colour-changing mechanisms for structural health monitoring.
Such innovations are revolutionising product lifespans, maintenance protocols, and safety standards, particularly in high-value sectors like aerospace, defence, automotive, and critical infrastructure.
Growth Trajectory and Market Realignment
The ever-expanding global industrial coatings domain persists in moderate advancement for traditional segments, contrasted by swiftly proliferating smart and eco-friendly formulas powered by invention and incentives.
Asia-Pacific remains the growth engine for the industry, underpinned by massive infrastructure projects, urbanisation, and rapid manufacturing growth in countries like China and India. However, markets in Europe and North America are leading in terms of technological adoption and regulatory frameworks.
Digitalization and Supply Chain Evolution
Industry 4.0 is reshaping how coatings are developed, tested, and delivered. Digital tools—from AI-driven R&D platforms to lab automation and predictive analytics—are reducing time-to-market and enhancing product performance consistency.
On the supply chain side, the industry is navigating post-pandemic volatility, material shortages, and global geopolitical instability. Companies are investing in regional sourcing, digital inventory tracking, and flexible logistics models to ensure supply chain resilience and responsiveness.
Advanced Materials and Next-Gen Applications
We are still pushing the limit every day around coatings by materials science. The novel addition of the nanomaterials, graphene, biopolymers and composite additives leads to advancements in strength, conductivity, chemical resistance and sustainability. This is important in applications where every gram really matters, like aerospace or manufacturing electric vehicles, because these materials are enabling thinner, lighter, and more functional coatings. The business model landscape of industrial coatings is gradually shifting from a commodity-driven paradigm to a high-performance, cutting-edge ecosystem. Whether it is going for zero-VOC emissions, smart coatings, or digitising production pipelines, we are at the edge of the technology cliff in this industry. While sustainability, digitisation and R&D are now more stringent than ever, only stakeholders to use these drivers will be the greatest best held in rein over the past decade of industrial coatings evolution.
The right industrial coating is more than a protective layer; it makes the difference between short-lived assets and those that last for decades. Wang Jian, Operations Director at Shandong Sunrise Chemical (Qingdao), discovered severe pitting corrosion in their ethylene storage tanks during a 2023 safety audit. The uncoated steel showed 2.4mm/year material loss – triple the industry safe limit. Also, we’ve 200+ installations documenting these outcomes in the real world. As coatings evolve from self-healing polymers to carbon-absorbing smart film, the gap between cutting-edge solutions and outdated methods widens. Don’t let your equipment become a cautionary tale. To find the right solution, it starts with the right supplier. Use our website directory, which will help you find those solutions. Browse the supplier listings, compare expertise, and connect directly with coating providers who meet your technical and operational needs and which partners are best equipped to protect what matters most in your next project.
FAQs
What is the meaning of industrial coating?
An industrial coating is a paint or coating defined by its protective, rather than its aesthetic properties, although it can provide both.
What is the purpose of a coating?
Most coatings, to some extent, protect the substrate, such as maintenance coatings for metals and concrete. A decorative coating can offer a particular reflective property, such as high gloss, satin, matte, or flat appearance. A major coating application is to protect metal from corrosion.
How many types of coatings are there?
There are many types of coatings, broadly categorised into architectural, industrial, and special-purpose coatings. Within these categories, specific types include epoxy, polyurethane, acrylic, zinc-rich, alkyd, ceramic, and intumescent coatings, among others. See more coating type classification rules.
What is the best industrial coating?
There’s no single “best” industrial coating; it all depends on the application, environment, and substrate. Epoxy coatings can be easily preferred because of their durability and chemical resistance, yet other coating types, such as polyurethanes, zinc-rich primers, or polyureas, might be more appropriate in certain conditions.
What is industrial ceramic coating?
Industrial ceramic coatings are specialised coatings that are applied to metal surfaces so as to improve durability and resistance to wear and corrosion. The term “industrial ceramic coating” can refer to various kinds of coatings, each with its unique set of properties.