Coatings have become a common substance in life to protect the surface of objects and increase their beauty. In order to make it easier to distinguish, professional coating industry practitioners often divide them into conversion and non-conversion types. But others are confused. How can normal people distinguish conversion and non-conversion coatings? In combination with everyone’s feedback, we have specially compiled this article. In-depth exploration of what conversion coatings are, study different types of chemical conversion coatings, compare them with non-conversion coatings, and provide guidance on how to choose the right coating for your specific needs. Understanding these coatings will help you make an informed decision to ensure that your products have the best performance and service life.
What is conversion coating?
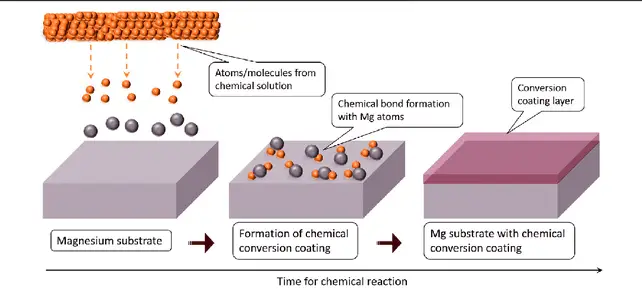
Chemical conversion coating principle
Conversion coatings are often viewed as a marvel of materials science. They generally refer to the process of converting the surface of a substrate (usually metal) into a corrosion-resistant and easily bonded coating. This conversion occurs through a chemical reaction, which results in a protective coating. Chemical conversion coatings are the backbone of many industrial processes. These coatings are formed through a chemical reaction between the metal surface and a solution containing specific compounds. The reaction produces a thin layer of adherent metal oxides or other compounds that enhance the properties of the metal. Coatings that work by changing the metal surface are usually inorganic coatings, and there is also an organic conversion coating.
Organic conversion coatings involve chemical interactions of resin molecules. These molecules undergo processes such as condensation, addition polymerization, or oxidative polymerization to form a cross-linked network. This network solidifies into a strong protective film. Imagine a spider weaving an intricate web, only here, the web is a durable protective shield covering the material.
Advantages | Disadvantages |
---|---|
Provides excellent corrosion resistance | May require precise control of application process |
Enhances paint adhesion | Some types involve hazardous chemicals |
Improves wear resistance | Can be less effective on certain substrates |
Can be applied to various metals and alloys | Inorganic coatings may be brittle |
Often cost-effective and easy to apply | Requires proper disposal of chemical waste |
Conversion coatings find applications across various industries due to their versatile properties. Here are some key applications:
- Automotive Industry: Used to protect car bodies and components from rust and enhance paint adhesion.
- Aerospace Industry: Critical for protecting aircraft parts from corrosion and wear.
- Electronics: Provides a corrosion-resistant layer on connectors and circuit boards.
- Construction: Used on structural components to prevent rust and improve paint performance.
- Medical Devices: Ensures long-lasting and durable coatings on surgical instruments and implants.
Conversion coatings are indispensable in modern manufacturing and industrial processes, providing essential protection and enhancing the longevity of materials. Understanding their types, applications, and benefits can help industries make informed decisions and leverage these coatings for optimal performance.
What Are the Types of Chemical Conversion Coating?
Comparison of Organic and Inorganic Conversion Coatings | ||||
---|---|---|---|---|
Type | Definition | Examples | Advantages | Disadvantages |
Organic Conversion Coatings | Resin molecules react and form a cross-linked, solid film. | Air-Drying, Curing Agent-Cured, Baking-Cured, Radiation-Cured | Provides aesthetic appeal, flexible application, and excellent protection. | Requires precise control of curing conditions and can be sensitive to environmental factors. |
Inorganic Conversion Coatings | Metal surface reacts to form oxides or mineral compounds. | Chromate, Phosphate, Oxide, Zinc Phosphate, Passivation, Phosphating, Nitriding | Offers excellent corrosion resistance and durability. | Some types involve hazardous chemicals and can be brittle. |
What Is an Organic Conversion Coating?
Organic conversion coatings involve chemical reactions of resin molecules and are known for their ability to provide strong protection and enhance the beauty of various substrates. These reactions undergo processes such as condensation, addition polymerization, or oxidation polymerization. The process usually requires heat to drive and accelerate the chemical reaction, so these coatings are often called thermosetting coatings. Phenolic paints, amino baking paints, polyester paints, acrylic baking paints, etc. are cured by condensation reactions; unsaturated polyesters, two-component epoxies, two-component polyurethanes, etc. are cured by addition polymerization reactions; oil-based paints, alkyd paints, and epoxy ester paints are cured by oxidation polymerization reactions.
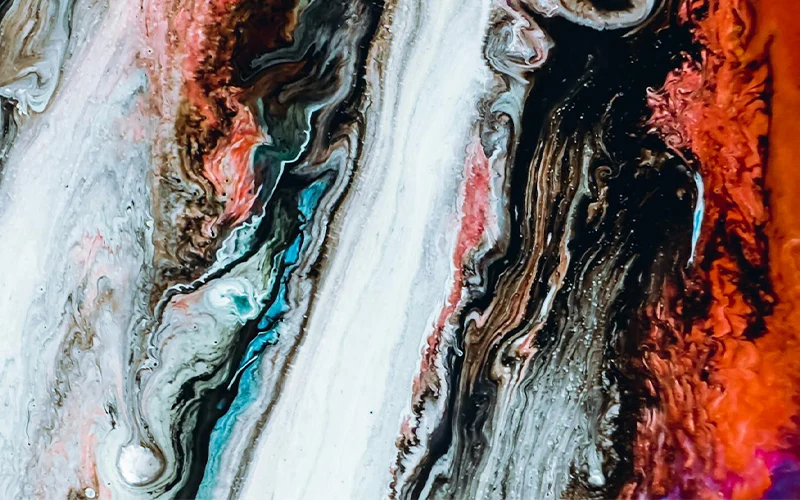
Organic coatings VS Inorganic coatings
Organic conversion coatings are usually divided into four types according to the curing method: air-drying coatings, curing agent-cured coatings, baking-cured coatings, and radiation-cured coatings.
- Air Dry Coatings:Air dry coatings cure by polymerization at ambient temperature with oxygen or moisture in the air. Oxidative polymers are formulated with resins that react with oxygen in the air to form a hard film. Moisture cure polyurethanes utilize the end isocyanates of the polyurethane resin to react with water molecules in the air.
This type of coating is easy to use and is ideal for applications where heat curing is not possible. They are commonly used for protective and decorative finishes on a variety of surfaces, including wood, metal, and plastic. - Curing Agent Cured Coatings:These coatings utilize a curing agent to initiate polymerization at room temperature. The curing agent (usually an amine, polyamide, or isocyanate) reacts with the resin to form a durable cross-linked network. The proportion of curing agent in the coating directly affects the coating performance and drying speed. The main types of coatings are: epoxy, polyurethane, and unsaturated polyester. Curing agent cured coatings are versatile and provide a strong and durable finish that can withstand chemical exposure and mechanical wear. They are widely used in industrial and automotive applications that require a strong protective layer.
- Bake Cure Coatings:Bake cure coatings are chemically weak on their own, so they require high temperatures to cure. Heat accelerates the polymerization process, forming a hard protective film. These coatings are often used in applications that require high durability and resistance to environmental factors. For example, automotive coatings, industrial coatings, and appliance coatings often rely on bake-cure coatings to achieve their outstanding performance characteristics. Representative coatings include: amino bake lacquers, acrylic bake lacquers, polyester paints, thermosetting polyurethanes, epoxy bake lacquers, and silicone coatings, among others.
- Radiation-cured coatings:Radiation-cured coatings use ultraviolet (UV) light or electron beams to initiate polymerization. These coatings cure quickly, offering significant advantages in production speed and energy efficiency. Radiation-cured coatings are often used in electronic, optical, and medical device applications because of their high performance and minimal environmental impact. They offer excellent abrasion resistance, chemical resistance, and adhesion.
What Is an Inorganic Conversion Coating?
Inorganic conversion coatings are formed by chemical reactions on the metal surface, converting it into metal oxides or mineral compounds. These coatings are highly valued for their excellent corrosion resistance and surface protection.
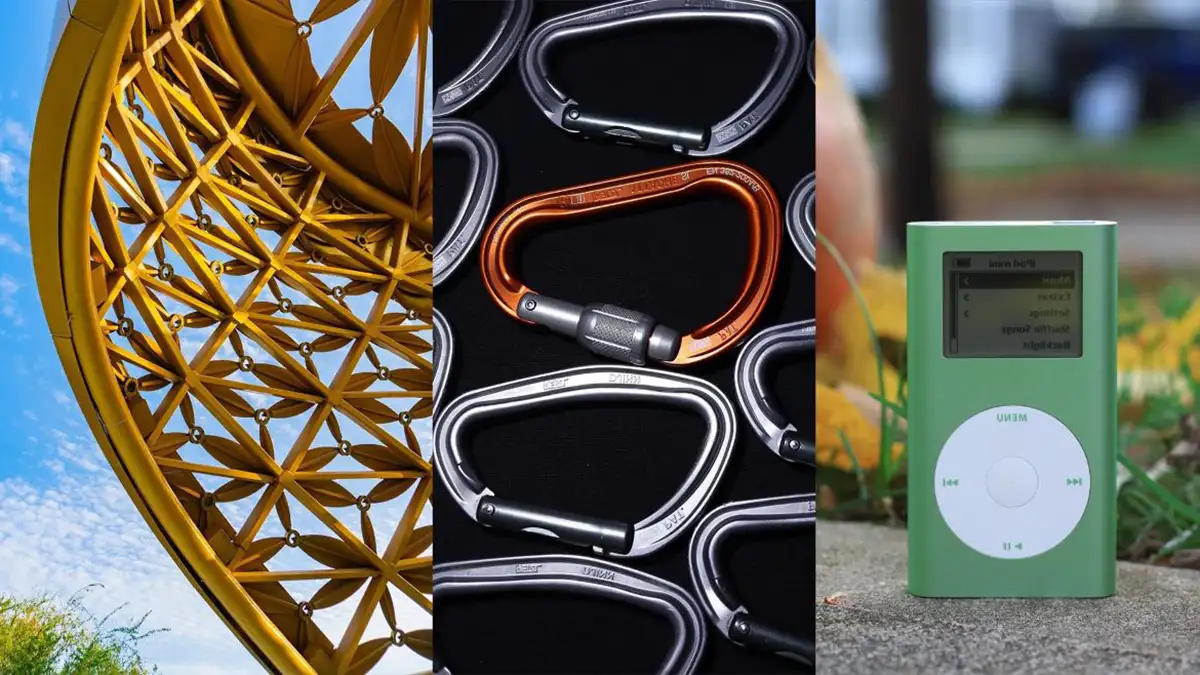
Application of inorganic chemical reaction conversion coating
- Chromate Coatings:Chromate coatings form a layer of chromate compounds on the metal surface, providing excellent corrosion resistance and paint adhesion. Despite their effectiveness, chromate coatings contain hexavalent chromium, which is highly toxic and environmentally hazardous. As a result, their use is being phased out in favor of safer alternatives. Nonetheless, they have been widely used in aerospace and military applications where superior corrosion protection is critical.
- Phosphate Coatings:Phosphate coatings are created by reacting phosphate salts with the metal surface to form a layer of metal phosphate. These coatings are commonly used for corrosion protection, paint adhesion, and as a lubricant base in cold forming processes. The three main types of phosphate coatings are zinc, iron, and manganese phosphates, each offering different levels of corrosion resistance and mechanical properties. Phosphate coatings are prevalent in automotive, heavy machinery, and construction industries.
- Oxide Coatings:Oxide coatings are formed by oxidizing the metal surface, creating a layer of metal oxide. Anodizing is a well-known process for aluminum, producing a durable and corrosion-resistant oxide layer. Other metals, such as titanium and zinc, can also be anodized. Oxide coatings enhance the corrosion resistance and wear resistance of the substrate. They are commonly used in aerospace, electronics, and architectural applications.
- Zinc Phosphate Coatings:Zinc phosphate coatings provide a robust barrier against corrosion and serve as an excellent primer base. The zinc phosphate layer improves paint adhesion and offers enhanced protection against environmental factors. These coatings are widely used in the automotive industry, heavy machinery, and industrial equipment to extend the lifespan of components and reduce maintenance costs.
- Passivation Films:Passivation films involve the treatment of stainless steel and other alloys to form a thin, protective oxide layer. The passivation process typically involves using nitric acid or citric acid to remove free iron from the surface, resulting in a passive oxide film that enhances corrosion resistance. Passivation is commonly used in the food processing, pharmaceutical, and medical device industries to ensure the longevity and cleanliness of stainless steel components.
- Phosphating:Phosphating involves treating the metal surface with phosphoric acid to create a protective phosphate layer. This process improves corrosion resistance and provides an excellent base for subsequent painting or coating. Phosphating is widely used in automotive, appliance, and construction industries for its ability to enhance the adhesion and durability of topcoats.
- Nitriding:Nitriding is a surface hardening process that involves diffusing nitrogen into the metal surface to form a hard, wear-resistant layer. This process is commonly applied to steel components to improve surface hardness, fatigue resistance, and corrosion resistance. Nitrided surfaces are used in aerospace, automotive, and tooling applications where high wear resistance and durability are essential.
Conversion coatings, whether organic or inorganic, play a critical role in protecting and enhancing metal surfaces. By understanding the various types and their specific applications, coating specialists can make informed decisions to optimize performance and durability. Organic coatings offer versatility and aesthetic appeal, while inorganic coatings provide robust protection against corrosion and wear. Together, they ensure that the products we use daily remain durable, functional, and visually appealing, showcasing the brilliance of chemical conversion technology.
The Opponent of Conversion Coatings: Non-Conversion Coatings.
In the field of coatings, we often hear about the complex chemical reactions involved in forming a strong protective layer on a surface. But there is another important player in the field that relies entirely on physical conversion: non-conversion coatings. So, what exactly are non-conversion coatings? You can go to our corresponding blog to understand in detail, and I won’t go into details here.
How to Choose Between Conversion and Non-Conversion Coatings?
Selecting the right coating for your project is a critical decision that can impact the longevity, performance, and appearance of the coated substrate. Conversion and non-conversion coatings each offer distinct advantages and are suited for different applications. To help you make an informed decision, let’s explore the key factors to consider when choosing between conversion and non-conversion coatings.
- Understand Your Application Requirements
Conversion coatings are ideal for industrial and high-performance application needs that require high durability, excellent corrosion resistance, and superior adhesion. Especially if your project involves exposure to harsh chemicals, acids, or bases, conversion coatings such as chromate or phosphate coatings provide superior protection due to their chemical bonding layer.
Non-conversion coatings are ideal for aesthetic and decorative project applications where visual appeal is a priority. These coatings are available in a variety of colors, finishes, and textures for architectural, residential, and artistic applications. If your project requires a simple application process without specialized equipment, non-conversion coatings are a better choice. - Evaluate Environmental Conditions
Conversion coatings are designed to withstand extreme conditions, including high humidity, salt spray, and temperature fluctuations. For outdoor applications, especially in industrial or marine settings, conversion coatings provide a durable barrier that protects underlying materials in challenging environments.
Non-conversion coatings are suitable for environments with moderate exposure to weather and chemicals. They perform well in residential, commercial, and indoor environments where environmental stresses are not as severe. - Consider Application and Maintenance Costs
The application of conversion coatings generally involves a higher initial cost due to the need for specialized equipment, precise process control, and sometimes more expensive materials. However, their durability can reduce long-term maintenance expenses.
The initial cost of non-conversion coatings is generally more affordable. They do not require complex equipment or rigorous application conditions, so they can be used on a wider range of projects. - Evaluating Performance and Functional Properties
Conversion coatings offer superior performance in adhesion, corrosion resistance, and mechanical strength. They are designed to meet the stringent requirements of industrial applications. Some conversion coatings offer additional functional benefits, such as improved conductivity, lubricity, or heat resistance, making them suitable for specialized applications.
Non-conversion coatings offer a wide range of aesthetic options, from glossy to matte finishes and a variety of colors. They are ideal for projects where appearance and customization are critical.
By considering these factors, you can make an informed decision that ensures the longevity, effectiveness, and visual appeal of your coated substrates.
With this article, I believe you have a clear understanding of conversion coatings. Whether you choose organic or inorganic conversion coatings, they can provide superior protection and performance for your industrial applications. If you need to learn more or find a professional coating supplier and conversion coating service factory, please use our “coatingsdirectory.com” filter function to find the best partner for you.
What is chemical conversion coating?
Chemical conversion coating is a process that transforms the surface of a metal into a corrosion-resistant and adhesive-friendly layer through chemical reactions. Think of it as giving your metal a durable armor to protect it from rust and wear. This transformation can result in either organic or inorganic coatings, each with its own set of properties and applications.
What is chromate conversion coating?
Chromate conversion coating is a type of inorganic conversion coating where the metal surface reacts with chromate compounds to form a protective layer. It’s like giving your metal a superhero shield against corrosion and oxidation. This coating is particularly effective for aluminum and its alloys, providing excellent corrosion resistance and a good base for subsequent painting or coating.
What Industries Commonly Use Conversion Coatings?
Conversion coatings are used in a variety of industries due to their protective properties. From automotive to aerospace, and electronics to construction, these coatings are everywhere! They help in preventing rust on car parts, protecting airplane components, and ensuring durability in electronic devices. Essentially, any industry that deals with metal surfaces can benefit from conversion coatings.
Can Conversion Coatings Be Applied to All Metals?
Not all metals are created equal when it comes to conversion coatings. While many metals like steel, aluminum, and zinc respond well to these treatments, some might not. It’s always best to consult with a coating specialist to determine the suitability of a conversion coating for a specific metal. Generally, if it’s a common industrial metal, there’s likely a conversion coating that will work for it.