Break down the composition of liquid painted and powdered enamel coatings. See what types of enamel coatings it can make up.
What is porcelain enamel coatings?
Enamel coatings, also known as porcelain enamel coatings, are thin layers of ceramic or glass inorganic coatings applied to metal substrates. They are usually applied to the surface of the substrate in liquid or glass powder form, and then heated at high temperatures (above 850°C) until the glass melts and forms a smooth glass layer. After cooling, the layer becomes a hard glass-like shell that is resistant to corrosion, chemicals, and heat.
The specific definition of enamel coating depends on its composition. Porcelain enamel is usually made from natural inorganic raw materials and supports 100% recyclability, making it an environmentally friendly coating. The mineral mixture is melted in much the same way as ordinary window or container glass, but there is no similarity in composition because there is no glass component in enamel paint.
The production process of porcelain enamel.
The production of porcelain enamel involves a series of processes such as high-temperature melting, quenching and crushing. The raw materials for enamel are first completely melted in a furnace at temperatures exceeding 2000 degrees Fahrenheit. The molten mixture is then poured from the furnace and quenched between water-cooled rollers (a process called frit). The rapidly cooled solid enamel is then crushed into flakes or frits. The chemical composition of the frit can be tailored to the desired properties of the final coating and the metal substrate being used.
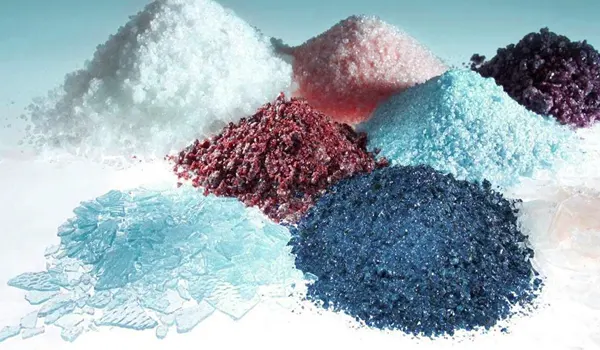
porcelain enamel
History of enamel coatings.
Porcelain enamel coatings have a long history. As early as around 1000 BC, ancient civilizations such as the Egyptians and Greeks applied porcelain enamel to metal objects such as jewelry and artwork.
By the 1840s, enamel paint was only a decoration for small items such as watches and jewelry. As industrial processes developed, enamel coatings were more efficient to apply, allowing for large-scale production, and enamel coatings emerged.
In the 1850s and 1860s, enamel began to be used for more practical purposes, such as cookware and building materials.
The early 20th century saw the enameling process gain momentum, with widespread use in the production of kitchen utensils, bathroom fixtures, and even architectural panels used on buildings.
Today, enameling steel is a high-tech process, and innovations in manufacturing techniques, such as automated spray systems and improved heating methods, have further expanded the range of applications for enamel coatings. Modern techniques allow for more precise control of thickness, color, and texture, making the coating more versatile and customizable than ever before.
Enamel coatings are usually available in two main forms – liquid enamel and powder enamel. Each type uses different ingredients, which directly determine how they work and are used.
Liquid enamel paint is usually made from a mixture of white spirit, white lead, pigments, oils and resin materials. The solvent helps the paint spread easily, while the resins and oils bind these ingredients together to form a hard surface. The pigments give the paint its color, and the white lead helps increase the opacity and durability of the paint. These ingredients work together to form a smooth and durable coating that dries to a hard and smooth coating.
- Finish: Glossy, durable, good color retention, scratch-resistant, heat-resistant, and waterproof.
- Application: Apply to the surface by brush, spray or roll.
Powdered enamel coatings (commonly called porcelain enamel) are composed of inorganic materials (such as silica), metal oxides, and glass-forming compounds. These materials fuse to the metal surface at high temperatures to form a hard, glass-like coating. The silica forms the basis of the glass layer, while the metal oxides provide color and increase the strength of the coating. In addition, ingredients such as pigments, opacifiers, and surfactants are carefully blended and ground as needed and for a specific surface finish.
- Finish: Hard, waterproof, glass-like, usually glossy or semi-gloss.
- Purpose: Powder is fused to metal at high temperature.
Widely valued for its versatility and durability, enamel coatings adhere to many surfaces, including glass, aluminum, galvanized steel, stainless steel, wood, plastic, porcelain, and ceramic. Whether it’s a smooth surface like metal or a porous surface like wood, enamel paint forms a strong protective layer.
- In domestic applications, we can see enamel coatings on appliances such as ovens, stoves, refrigerators, and bathtubs. These coatings form a smooth and durable surface that resists scratches, heat, and even moisture. Take your stovetop, for example: Even after years of cooking and high temperatures, enamel will keep its appearance like new. Its easy-to-clean surface is a big reason why it is a preferred finish in kitchens and bathrooms, where hygiene and aesthetics are top priorities.
- In the industrial sector, factories and workshops often rely on enamel to coat machines and tanks that come into contact with aggressive chemicals or high temperatures. Enamel’s non-porous surface also makes it ideal for environments where cleanliness is critical, such as food processing plants or medical device manufacturing. Here, enamel ensures that the surface remains hygienic and can be easily disinfected.
- Enamel coatings are also popular in building panels, outdoor furniture, grills and road signs because of their ability to withstand the elements. Its strong resistance to UV rays, moisture and extreme temperatures ensures that these surfaces are not easily worn, making enamel-coated products a long-term investment.
What types of enamel coatings are there?
Enamel coatings are generally divided into painted enamels and porcelain enamels (or glass enamels), which are available in a variety of finishes and applications. Each type has a formulation for a specific use.
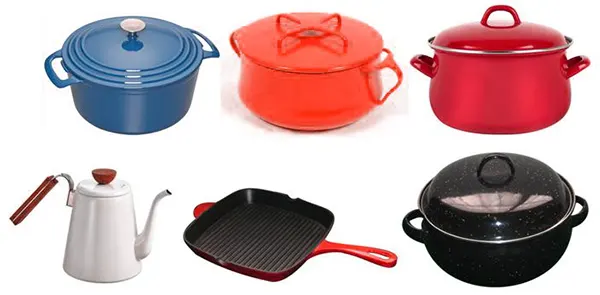
Application of enamel coating
Types of enamels
Porcelain enamels, also known as glass enamels or powdered enamel coatings. Applied in powder or liquid form and fired at high temperatures, porcelain enamels provide an extremely hard, glass-like surface, primarily for metals. Its composition and characteristics have already been described above, so we will not repeat them here.
- Standard enamels:These enamels consist of a mixture of silica (SiO₂), which forms the base glass matrix, and other oxides such as boron, aluminum, and alkali oxides. Metal oxides such as cobalt, chromium, or iron oxide are often added to give the enamel different colors or enhance its durability or corrosion resistance.
- Specialized functional enamels:Some enamels are designed for more demanding applications, such as those exposed to extreme temperatures or corrosive chemicals. These formulations may contain higher concentrations of refractory oxides such as titanium or zirconium to improve heat resistance or chemical durability. These enamels are often used in industrial applications, such as lining pipes, tanks or furnaces. There is no particularly clear classification at present, as its composition may vary due to its specific application and required properties.
Painted enamel types
Painted enamels are presented in liquids, making them easier to apply. Unlike porcelain enamels, which need to be differentiated by specific application, painted enamels can be clearly classified based on their chemical composition formula. Each subtype has unique properties for different application scenarios.
- Acrylic enamel:It combines the durability of traditional enamels with the flexibility of acrylic. It dries faster than oil-based enamels and is more environmentally friendly. Because it is water-based, it is easy to clean with soap and water, which is perfect for DIY projects, such as painting furniture or interior walls.
- Alkyd enamel:This enamel is ideal for areas with high traffic or exposed to outdoor environments, such as doors, trim, and even machinery. It provides a smooth, durable coating and resists wear and tear.
- Epoxy enamel:This is the most common type of enamel used in industrial settings, especially for surfaces that need to withstand heavy use or harsh environments, such as floors or factory equipment. It bonds well to metal and has excellent chemical resistance, toughness, and moisture resistance.
- Oil-based enamel:Oil-based enamel offers excellent durability and a smooth, high-gloss finish. It is widely used to paint metal surfaces, such as railings or gates. While it is long-lasting, it has a slow drying time and a strong odor.
- Water-based enamel:Modern water-based enamels combine the strength of oil-based enamels with the easy cleanability of water-based products. They are ideal for interior spaces such as kitchens or bathrooms where low odor and fast drying are important.
- High-temperature enamel:Designed to withstand high temperatures, it is often used on engines, exhaust systems, or any metal surface exposed to high temperatures. It can withstand temperatures up to 1,200°F (650°C), ensuring that the coating remains intact in extreme conditions.
Understanding the differences between them can help you choose the right type of enamel coating for your project. A detailed guide to purchasing enamel paint can be found in our other blog.
6 common misunderstandings about enamel coatings.
I’ve found that many fans of coatingsdirectory don’t know much about enamel coatings, and even have some misunderstandings. Today, let me clarify the six most common misunderstandings that fans ask the most.
1. Enamel paint is just ordinary paint with a fancy name
Some people think that enamel is just a marketing term for ordinary paint. In fact, enamel coatings are designed to provide a harder and more durable finish than standard paint. Although they may look similar to other paints in the can, their chemical composition is different.
2. Enamel coatings are only suitable for metals
Many people think that enamel coatings are only suitable for metal surfaces, which is wrong. Enamel coatings are indeed more common on metals, but that doesn’t mean it can only be used on metals. Enamel paint can also be applied to wood, masonry or plastic with great results.
3. All enamel coatings are glossy
Not all enamel coatings have to be glossy. While most enamel coatings are designed to have a high-gloss appearance, enamel products also offer matte and satin finishes.
4. Enamel Paint and Porcelain Enamel are the same thing
This misunderstanding often occurs. Although they are both called “enamel”, enamel paint and porcelain enamel are two very different products. Enamel paint is a liquid, oil-based or water-based coating that hardens into a durable coating. Whereas porcelain enamel is a glass-like coating made by fusing powdered materials to metal at high temperatures.
5. Enamel coatings are difficult to handle
Due to their high strength, people tend to think that enamel paints are too difficult to apply and remove. In fact, as long as you follow the correct steps, enamel paints are very easy to use. You can go to our corresponding guidance blog for a practical guide to using enamel paints.
6. Enamel coatings do not require maintenance
Everyone always thinks that enamel coatings never need maintenance. Although enamel coatings are indeed durable, they are not indestructible. Over time, even the hardest enamel paint or porcelain enamel will scratch, chip or fade, especially when exposed to harsh environments. Regular cleaning and occasional touch-ups are necessary.
Is enamel paint waterproof?
Yes, oil-based or lacquer-based enamel paint is waterproof. It forms a strong protective layer that can handle water and humidity. However, water-based enamel paint is not waterproof. Over time, excessive exposure to water can cause damage. To be completely waterproof, especially for exterior applications, an additional sealer or primer may be required.
Is enamel coating safe?
Yes, enamel coating is safe once it is fully cured. But personal protection is still required during the application process. Water-based enamel paint contains fewer harmful chemicals, while oil-based enamel paint may emit stronger fumes during the application process. Always apply enamel coating in a well-ventilated area and use protective gear.
Is enamel paint oil based or water based?
Enamel paint can be oil-based or water-based. But most traditional enamel paints are oil-based. Nowadays, with the upgrading of enamel paint formula, popular water-based enamel paint has been born, becoming the choice of many environmentally friendly applications.