Article Chapters
Spin coating is a key technology across a wide range of industries. As a simple solution-based method (applicable to a wide range of organic and inorganic materials and their composites), it is used to create precise and uniform thin films with thicknesses ranging from nm to µm. This is essential for high-quality coatings in certain fields. Follow me today to take a look at the dip spin coating technique and the key parameters involved in performing dip spin coating. Whether you are new to the concept of spin coating or looking to complete your knowledge base, this guide provides valuable insights and practical tips to enhance your understanding of spin coating.
What is Spin Coating Method?

Spin coating process
Spin coating is a technique for coating a thin film on a substrate using non-vacuum deposition, and is used to obtain uniform, high-quality CZTS thin films at low cost. The centrifugal force generated during high-speed rotation is used to form a thin and uniform film on the substrate by the centripetal force and surface tension of the liquid.
The detailed working principle is to fix a uniform and flat substrate on the spindle, apply excess solution to the substrate (manually: using a syringe; automatically: using a dispensing device and a dispensing nozzle in the spin coater cover), and distribute the liquid coating solution to the center of the workpiece. When the substrate is rotated at high speed (usually >10 rpm = 600 rpm), the liquid coating material is forced to spread outward under the action of centrifugal force, forming a thin and uniform coating. The rotation continues until the desired film thickness is reached, and the excess material is thrown off the edge of the rotating substrate, leaving a uniform film on the surface.
The history of spin coat technology can be traced back to the middle of the 20th century. Spin coating was originally developed for the semiconductor industry, where the need for ultra-thin, uniform coatings on silicon wafers was critical. Over the years, advances in technology and materials science have refined the process, making it more versatile and efficient.
In the 1960s, spin coating became the standard method for manufacturing integrated circuits, contributing greatly to the miniaturization and performance of electronic devices. By the 1980s, spin coating had expanded into other fields such as optics and nanotechnology, proving its adaptability and effectiveness.
Today, spin coating continues to evolve, incorporating new materials and innovative techniques to meet the growing demands of advanced manufacturing processes. From creating anti-reflective coatings on lenses to depositing photoresist layers in micromachining, the applications of spin coating are varied and essential.
Advantages | Limitations |
---|---|
Uniform coating: Achieve highly uniform and thin coatings with a thickness variation of no more than 1% due to self-leveling. This is critical for high-precision applications. | Material waste: Can result in significant material waste due to excess coating being flung off. |
Speed: Fast processing speeds make it suitable for high-throughput production environments. | Substrate limitations: Best for flat, round substrates; less effective for large substrates and irregularly shaped substrates. |
Cost-effective for thin films: Suitable for very thin films, thereby reducing material costs for such applications. | Thickness control: Achieving very thick coatings is challenging due to the nature of centrifugal diffusion. |
Scalability: Can be easily scaled up for large-scale production. | Equipment cost: The initial investment in spin coating equipment is high. |
Versatility: Can be used with a wide range of coating materials, including polymers, metals, and nanoparticles. | Edge effect: Coating may not be uniform at the edges of the substrate. |
Easy to operate: The spin coating process is very simple to set up, which, combined with the ability to achieve thin, uniform coatings of varying thicknesses, makes it ideal for research and rapid prototyping. | / |
Easy to dry: Due to its high spin speed, drying times can be reduced (due to high airflow). | / |
What Are the Common Applications of Spin Coating?
Spin coating can be used to coat almost anything, from small items just a few square millimeters to substrates that may be a meter or more in diameter. Its ultra-high precision and versatility allow it to be used to coat a wide variety of substrates, from photoresists, insulators, organic semiconductors, synthetic metals, nanomaterials, metal and metal oxide precursors, transparent conductive oxides, and many more.
- Electronics Industry:
Spin coating is a fundamental technology in microelectronics and semiconductor manufacturing. It is widely used to apply photoresist layers to silicon wafers, which is essential for the photolithography process of manufacturing integrated circuits and microchips. The uniform thin films obtained by spin coating are essential to ensure the precision and performance of these tiny electronic components. - Optics and Photonics:
Spin coating is used to apply anti-reflective coatings and other functional layers to lenses, mirrors, and optical fibers. These coatings improve the performance and durability of optical devices. - Biomedical Devices:
Spin coating is used to create biocompatible coatings to improve the interaction between medical implants and biological tissues. These coatings help reduce the risk of infection and extend the life of the implant, which can help improve patient outcomes. - Solar Cells:
Spin coating allows for the precise application of light-absorbing materials for the production of thin-film solar cells. By optimizing the coating process, manufacturers can increase the energy conversion efficiency of solar cells, making them more cost-effective and sustainable. - Nanotechnology:
Spin coating can be used to create thin films and coatings with nanometer-scale precision. Examples include nanoparticle coatings and nanocomposites, which can be used in areas such as sensors, catalysis, and advanced materials development. - Semiconductor Industry:
Spin coating plays an irreplaceable role in the current semiconductor industry, especially for the manufacture of microchips and integrated circuits. High uniformity and purity help deposit photoresist layers on silicon wafers during the photolithography process. This precision coating is essential for defining complex circuit patterns and achieving the miniaturization required for modern electronic devices.
How To Do Spin Coating?
The complete process of uniformly coating a substrate using spin coating is divided into 6 different stages: preparing the substrate, depositing the coating, spinning, evaporating, drying & curing, and inspecting. The step-by-step process of executing this series of precise techniques can help achieve a perfect, uniform coating. Step-by-step guide to spin coating:
- Substrate preparation:
Before you begin, the substrate (usually a silicon wafer, glass slide, or other solid surface) needs to be completely clean. Any dust, oil, or residue will ruin the uniformity of the coating. The cleaning method usually involves a solvent (such as acetone or isopropyl alcohol) followed by a drying process using nitrogen. Once cleanliness is determined, the substrate is placed on the spin coater chuck, which holds it firmly in place.
This process usually involves the following equipment and materials: clean room environment, solvent (acetone, isopropyl alcohol), nitrogen dust collector. - Depositing coating:
The coating solution is deposited onto the center of the substrate (wafer or other substrate) using a nozzle or pipette. Common polymers include PMMA (polymethyl methacrylate) and PVA (polyvinyl alcohol). Spin coating can be dispensed in two ways: static dispensing and dynamic dispensing.
The process typically uses equipment and materials such as pipettes, polymer solutions, etc. - Spinning:
The spin coater accelerates the substrate to the final desired spin speed (depending on the viscosity of the substrate and the coating fluid). As the substrate spins, centrifugal force spreads the polymer solution evenly over the surface. After the constant spin rate reaches a peak, excess fluid is thrown off to produce a thinner coating. This is why it is recommended to deposit excess coating on the substrate in the previous step.
The process typically uses a spin coater, a programmable controller, and a vacuum chuck. - Evaporation:
Once the target coating thickness is reached, the spin rate is controlled and the fluid flow is stopped. The solvent in the coating fluid evaporates to thin the film. The solvent evaporation rate depends on the solvent volatility, vapor pressure, and environmental conditions. - Drying/curing the coating:
After spinning, the substrate is moved to a dry drying oven, a UV curing station for curing, or a UV lamp for polymerization, depending on the coating material. Please note that the spin coating process may leave deposits on the edges of the substrate. The edges are usually removed when the coating is semi-cured. - Quality Inspection:
After curing, it is critical to check the uniformity and thickness of the coated substrate. Techniques such as profilometry or ellipsometry can be used to measure coating thickness and ensure it meets the required specifications.
Differences between dynamic and static dispensing techniques in spin coating.
In the field of spin coating, the application of the coating material is a key step. I believe you have also discovered above that there are two main techniques used to apply the coating material to the substrate: dynamic dispensing technology and static dispensing technology.
- Dynamic dispensing technology:In the dynamic dispensing technology, the coating material is applied while the substrate is spinning. This method is particularly useful for achieving highly uniform coatings.
Dynamic Dispense Technique
- Static dispensing technology:The static dispensing technology involves applying the coating material to a stationary substrate before starting the spinning process. This method is generally suitable for thicker coatings or when using high-viscosity materials.
Static Dispense Technique
Dynamic Dispensing VS Static Dispensing | ||
---|---|---|
Technique | Dynamic Dispense Technique | Static Dispense Technique |
Procedure | Start spinning the substrate at low speed (around 500 RPM). | Place the substrate on the spin coater chuck and ensure it is securely held. |
While spinning, dispense the polymer solution onto the center of the substrate. | Deposit the polymer solution onto the center of the stationary substrate. | |
Gradually increase the spin speed to the desired rate. | Begin spinning the substrate at the desired speed. | |
Maintain the final spin speed to ensure any excess material is spun off, leaving a uniform coating. | Maintain the spin speed to allow the centrifugal force to distribute the coating material uniformly. | |
Tips and Tricks | Control the dispense rate to avoid overloading the substrate. | Ensure the coating material is precisely placed at the center of the substrate. |
Ensure a smooth and consistent increase in spin speed. | Start with a higher spin speed to quickly distribute the material. | |
Monitor the viscosity of the material; higher viscosity may require slower initial spin speeds. | Pre-warm the substrate if using highly viscous materials to aid in even spreading. | |
Considerations | Synchronize the dispensing and spinning actions for optimal coverage. | Use a precise amount of coating material to avoid wastage and ensure uniform coverage. |
Calculate the appropriate volume of coating material based on substrate size and desired thickness. | Adjust the technique based on the viscosity and drying properties of the coating material. |
The choice between dynamic and static dispensing techniques depends on the specific requirements of the spin coating process, including material properties and desired coating thickness. Both methods have their own unique advantages and considerations, and mastering them will help you achieve professional-grade results in your spin coating projects.
What Is Dip Spin Coating?
Spin coating techniques also include a unique process that combines dip coating and spin coating, dip spin coating. Dip spin coating begins by immersing the substrate into the coating solution (dip coating), followed by a conventional spin coating step to remove excess coating material and achieve a uniform coating. Traditional spin coating focuses primarily on planar substrates, but dip spin coating excels at coating three-dimensional objects with complex shapes. This method is particularly useful for coating objects with complex shapes and ensuring consistent coverage even in hard-to-reach areas. This makes dip spin coating ideal for applications where conventional spin coating has difficulty providing uniform coverage.
How Does Dip Spin Coating Work?
Dip-spin coating requires more steps than regular spin coating to create the desired coating result.
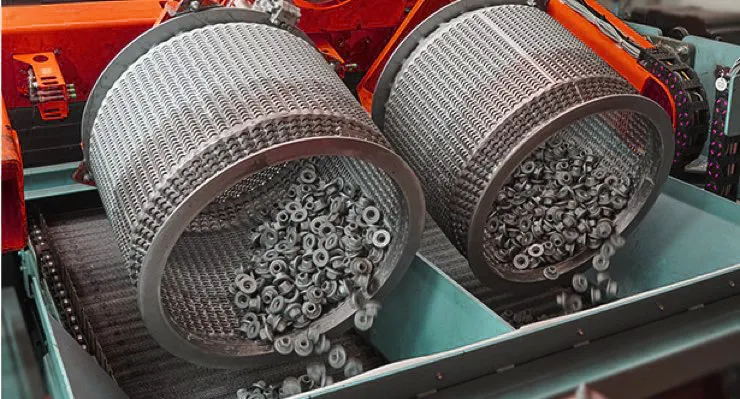
Industrial Automated Dip Spin Coating Equipment
- Preparation: Clean the substrate to remove any contaminants that may affect coating adhesion and quality.
- Dip coating: Dip the substrate into a bath of coating solution. This ensures that the coating material reaches all surfaces, including those that are difficult to cover with spinning alone.
- Spinning: After dipping, the substrate is quickly transferred to the spin coater. The spinning process begins, and centrifugal force is used to remove excess coating material and create an even coating. The speed and duration of the spin are carefully controlled to achieve the desired coating thickness.
- Drying/Curing: The coated substrate is then dried or cured to solidify the coating, ensuring it adheres properly and provides the desired properties.
Why Dip Spin Coating?
Dip spin coating offers many advantages over regular spin coating, which is why I’ve highlighted it in particular.
- Complex Geometries: Ideal for objects with complex shapes, such as fasteners, springs, and small parts.
- Consistent Quality: Combining the thoroughness of dip coating with the precision of spinning ensures an even, high-quality coating.
- Material Efficiency: Reduces waste by efficiently removing excess coating material during the spinning process.
A practical example: Imagine you are coating a batch of heterogeneous metal parts. Dipping ensures that the coating reaches every nook and cranny, while spinning afterwards removes excess coating and smooths the coating.
Dip spin coating combines the thoroughness of dip coating with the precision of spin coating. We can apply it to complex objects.
What Are the Key Parameters in Spin Coating?
We already know the process of performing the spin coating process. But to truly master this technique and achieve perfect results, you must understand the 10 key factors that influence the results. Slight changes in each factor will directly affect the final coating effect.
- Spin Speed:
Spin speed, usually measured in revolutions per minute (RPM), is one of the most critical parameters in spin coating. The higher the spin speed, the thinner the coating, while the lower the speed, the thicker the coating. The key is to find the right balance. - Spin Time:
Spin time determines how long the substrate is spun during the coating process. The longer the spin time, the more time the coating material has to spread and dilute, resulting in a more even coating. - Dispense Amount:
The amount of coating material applied initially, called dispense amount, is critical. Too much material results in waste and a coating that’s too thick, while too little may not adequately cover the substrate. - Viscosity of the Coating Material:
The viscosity, or thickness, of the coating material affects how it spreads during the spin process. Materials with lower viscosities spread more easily, resulting in thinner coatings, while materials with higher viscosities produce thicker coatings. - Acceleration:
Acceleration refers to how quickly the spin coater reaches the desired rotational speed. Smooth acceleration ensures that the coating material is evenly distributed, preventing defects such as streaks or bubbles. - Substrate Preparation:
A clean, well-prepared substrate is essential for successful spin coating. Any dust, oil or impurities will affect the adhesion and uniformity of the coating. A clean surface ensures the best results. - Environmental Conditions:
Temperature, humidity and airflow can significantly affect the spin coating process. Consistent environmental conditions ensure repeatable and uniform coatings. - Drying Speed:
The drying speed of the coating material affects the quality of the final film. Controlled drying prevents defects such as cracks and ensures a smooth surface. It’s like letting paint dry at the right speed to avoid bubbles and streaks. - Percent Solids:
The solids content of the coating solution determines the thickness and properties of the final film. Generally, high-solid coatings produce thicker coatings due to significantly lower evaporation losses after curing. Click here to learn more about high solid coatings. - Surface tension of the substrate:
The surface tension of the substrate affects the spreading behavior of the coating material.
Mastering these key parameters is crucial for achieving consistent and high-quality spin coatings. By carefully adjusting spin speed, time, dispense volume, viscosity, acceleration, environmental conditions, drying rate, solid content percentage, and ensuring proper substrate preparation, you can fine-tune your process to achieve the perfect coating every time. Keep these key factors in mind the next time you set up your spin coater – each one is a step towards spin coating mastery, creating a perfect, uniform surface with precision and finesse.
What Are the Challenges of Spin Coating?
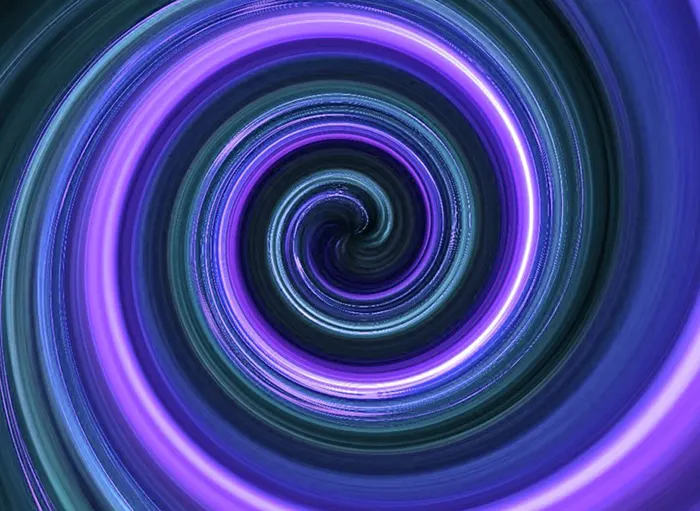
Spin coating
Spin coating, like any complex process, has its challenges. A good understanding of some of the common challenges in spin coating and the potential defects that can occur can help us avoid them.
- Uniformity Issues:
Achieving a perfectly uniform coating can be tricky. Variations in spin speed, substrate flatness, and dispensed volume can all lead to uneven coating. Any slight miscalculation can result in unevenness! - Over-thickness at the edge:
The coating material is extremely susceptible to bubbling in the peripheral area of the substrate (common when spin coating thicker polymer and photoresist films). This is caused by centrifugal forces pushing the material outward, with excess coating collecting at the edge. - Bubbles:
Trapped bubbles can mar the coating surface, causing defects that affect its quality. These bubbles can be introduced when dispensing the coating material or due to improper substrate preparation. - Particle Contamination:
Inadequate initial cleaning can cause dust particles and other contaminants to become trapped in the coating, causing imperfections. Even the tiniest dust particles can create noticeable defects. - Improper Evaporation:
Rapid evaporation of solvents can cause problems such as streaking or marbling in the coating. This is particularly problematic when using volatile solvents. - Adhesion Issues:
Ensuring that the coating adheres properly to the substrate is critical. Inadequate substrate cleaning or incompatible materials can lead to poor adhesion. - Large Substrates:
The biggest concern with spin coating is oversized substrates. As substrate size increases, high-speed spinning becomes difficult and thinning the film while maintaining uniformity becomes difficult. This requires finer control.
While spin coating is a powerful technique for achieving high-quality coatings, it requires careful attention to detail to overcome challenges. So how can you address these challenges? Read on.
How to Optimize Spin Coating Performance?
Achieving optimal spin coating performance is a delicate engineering exercise that requires fine-tuning equipment, perfecting techniques, and selecting the right materials. CoatingsDirectory has put together a comprehensive guide to help you master the art of spin coating, ensuring consistent, high-quality results every time.
- Gear Adjustment:
Setting up your spin coater is the most important part of the entire spin coating process.
Calibrate the Spin Coater: Regularly calibrating your spin coater ensures it’s running at the right speeds and times.
Keep it Clean: Keep your equipment spotless. Even tiny particles can affect results, just like a speck of dust on a camera lens can ruin a perfectly good photo.
Monitor Environmental Conditions: Control the temperature and humidity in your spin coating environment. Think of it as creating the perfect greenhouse for your plants. - Substrate Preparation:
A clean and well-prepared substrate is the foundation for a successful spin coating process.
Thorough Cleaning: Remove all contaminants using solvent or plasma cleaning. A clean surface ensures optimal adhesion.
Surface Treatment: Depending on the substrate, silanization. Treatments such as sanding can improve adhesion. It’s all about getting the coating to adhere better. - Coating Material Selection:
Choosing the right coating material is critical to achieving the desired properties and performance.
Viscosity Control: Choose a coating with the right viscosity for your application. Materials with lower viscosities spread more easily and vice versa.
Solvent Selection: Choose a solvent with the right evaporation rate to avoid defects such as streaking. Don’t go too fast or too slow. - Spin Coating Technique:
Perfecting your technique involves mastering the steps and sequence of the spin coating process.
Dispensing Amount: Apply the right amount of coating material. Too much or too little will result in defects, just like adding too much or too little frosting to a cake.
Spin Speed and Duration: Adjust the spin speed and duration to achieve the desired coating thickness. The faster the speed, the thinner the coating.
Smooth Acceleration: Ensure smooth acceleration to the desired spin speed to avoid splattering. Smooth acceleration determines coating uniformity. - Post-Coating Treatment:
The final steps are critical to curing and perfecting the coating.
Drying and Curing: Control the drying and curing process to prevent defects. It’s like baking a cake – you need the right temperature and time to achieve the perfect result.
Inspect and Test: Regularly inspect the coating for uniformity and defects. Constant inspection ensures a top-notch product.
Common Issues and Solutions for the Spin Coating Process | ||
---|---|---|
Issue | Cause | Solution |
Non-Uniform Coating | Uneven spin speed, improper substrate leveling | Ensure spin coater is properly calibrated and substrate is level before starting the process. |
Edge Bead Formation | Centrifugal force causing material to accumulate at edges | Use edge bead removal techniques or adjust dispense volume to minimize excess material. |
Air Bubbles | Trapped air during dispensing, contaminants on substrate | Degas the coating solution before use and thoroughly clean the substrate. |
Particle Contamination | Dust or particles in the environment or on the substrate | Maintain a clean environment, use cleanroom protocols, and clean the substrate thoroughly. |
Streaks and Striations | Rapid solvent evaporation, inconsistent spin speed | Adjust solvent composition and spin parameters to ensure even evaporation. |
Pinholes and Voids | Air bubbles, contaminants, or improper drying | Filter the coating solution, improve substrate cleaning, and control drying conditions. |
Thickness Variations | Inconsistent dispense volume, uneven spin speed | Calibrate the dispense system and ensure uniform spin speed throughout the process. |
Wrinkling and Cracking | Excessive coating thickness, improper curing | Apply thinner layers and adjust curing process to ensure even and gradual drying. |
Poor Adhesion | Contaminated substrate, incompatible materials | Clean the substrate thoroughly and use adhesion promoters or surface treatments as needed. |
Solvent Evaporation Issues | Volatile solvents causing rapid drying | Choose solvents with appropriate evaporation rates and control ambient conditions. |
By understanding these common problems and their corresponding solutions, you can fine-tune your spin coating process to improve the reliability and consistency of your spin coating process. Regularly monitoring and adjusting spin coating equipment, substrate pretreatment, selecting the right materials, perfecting techniques, and ensuring proper coating post-treatment are key to overcoming these challenges to ensure consistent performance and superior results.
In summary, spin coating is a versatile and precise method for applying uniform coatings, with applications across a wide range of industries. We have covered the basics of dip spin coating, key parameters, challenges, optimization strategies, and the latest technological advances. If you have some personal insights on the spin coating process, you are welcome to share your experiences and questions in the comments below. In addition, make full use of our search and filter functions on coatsdirectory.com to connect with top spin coating service providers and equipment manufacturers. Let’s continue the conversation and deepen our collective understanding of spin coating.
How thick can a spin-coated layer be?
Sure, spin coating can create very thin coatings, but how thin or thick can it really be? Typically, spin coatings range in thickness between 2 and 10 micrometers. This thickness is largely determined by the viscosity of the coating solution and the spin speed. High speeds of spin and low viscosity solutions generally produce thinner coatings, while slower spins and thicker solutions produce thicker coatings.
What factors affect thickness of spin coating?
Several factors affect spin coating thickness. Key factors include the viscosity of the coating material, spin speed and time. Additionally, environmental conditions such as temperature and humidity, and the surface characteristics of the substrate also come into play. Essentially, a delicate balance between these variables determines the final thickness.
How to estimate spin coat thickness?
Estimating the thickness of a spin coating requires some calculations and experience. Typically, you start with empirical formulas or spin coating models that relate spin speed and solution viscosity to film thickness. These models, such as the Cauchy model or Newtonian fluid equations (film thickness after spin coating is determined by five parameters: angular velocity, spin time, viscosity, density of the coating material, and initial thickness of the material before spin coating). However, for precise control, actual measurement using tools such as ellipsometers or profilometers is usually required.
What is speed important in spin coating?
Speed is a critical factor in spin coating because it directly affects the degree of centrifugal force applied to the resin and the turbulence of the air immediately above it, which in turn affects the final thickness and uniformity of the coating. Higher speeds generally produce thinner, more uniform coatings because excess solution is more efficiently spun off the substrate. On the other hand, lower speeds can produce thicker coatings but may compromise uniformity.
Can spin coating be used for all types of coatings?
Spin coating is very versatile, but it is not a one-size-fits-all solution. It works best with materials that form a uniform, stable solution and need to be applied in thin, uniform layers. Common examples include photoresists, polymers, and certain types of inks and coatings. However, for very thick coatings or materials with very high viscosities, alternative methods such as dip coating or spray coating may be more appropriate.