For industrial coatings, the choice between thermoplastic and thermoset coatings can greatly impact the longevity, performance, and cost-effectiveness of your project. While often confused, thermoplastic and thermoset coatings serve different purposes based on their composition, curing technology, and properties. Thermoplastic coatings offer flexibility, repairability, and ease of application, while thermoset coatings offer unmatched durability, chemical resistance, and thermal stability. We take an in-depth look at the characteristics and applications of both coating types, detailing their fundamental differences and exploring their unique properties, application methods, and ideal use cases to help you make an informed decision.
What Are Thermoplastic Coatings?
Thermoplastic coatings are specialized protective coatings that do not chemically react during the drying process, providing exceptional durability, flexibility, and resistance to environmental stresses. Unlike thermoset coatings, which irreversibly cure and harden, a notable feature of thermoplastic coatings is that they can be reheated and reshaped multiple times without losing their inherent properties. This reversible process makes repairs and modifications easier, a unique property that makes them particularly valuable in industries where both performance and reprocessing potential are critical.
Thermoplastic coatings are essentially polymer-based materials that melt when heated and solidify when cooled. This melting and resolidification process allows these coatings to form a strong and continuous coating on a variety of substrates, including metals, plastics, and ceramics. The seamless nature of the coating ensures that the coated surface is well protected from corrosion, chemical attack, and mechanical wear.
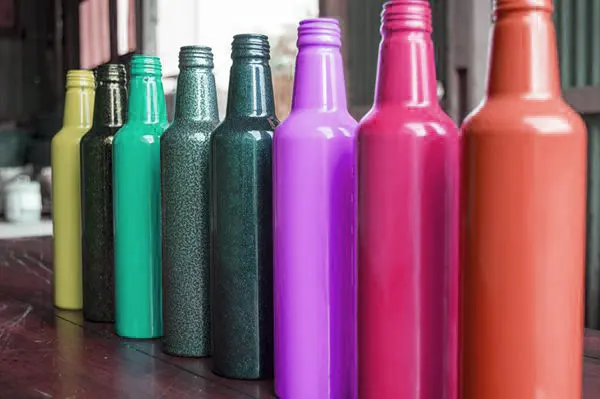
Applications of Thermoplastic Coatings
Thermoplastic coatings come in various forms, each with specific properties that make them suitable for different applications. Below is an overview of some common thermoplastic coating materials, along with their typical applications in various industries and on specific products or surfaces.
Material | Description | Application |
---|---|---|
Polyethylene (PE) | Known for its toughness, moisture resistance, and low friction coefficient. | Pipelines, cable coatings, automotive parts, and industrial equipment where surface smoothness is critical. |
Polyvinyl Chloride (PVC) | Offers excellent weather resistance, chemical stability, and affordability. | Used in automotive, construction, and marine industries for protective and decorative coatings. |
Polyamide (Nylon) | Prized for its abrasion resistance, high tensile strength, and low coefficient of friction. | Applied to mechanical components like gears, bearings, and fasteners. |
Polypropylene (PP) | Features chemical resistance and electrical insulating properties. | Electrical insulation, chemical storage tanks, and automotive components. |
Polystyrene (PS) | Offers rigidity and ease of processing, with moderate impact resistance. | Common in packaging, disposable containers, and laboratory equipment coatings. |
Polyoxymethylene (POM) | Noted for high stiffness, low friction, and excellent dimensional stability. | Used in precision parts such as gears, bushings, and automotive components. |
Polycarbonate (PC) | Combines toughness with high impact resistance and clarity. | Applied in optical discs, eyewear lenses, and bulletproof glass coatings. |
Polyphenylene Ether (PPE) | Exhibits high heat resistance and electrical insulation properties. | Used in electrical components and automotive parts exposed to high temperatures. |
Polysulfone (PSU) | Known for its toughness and ability to withstand prolonged exposure to high temperatures and chemicals. | Applied in medical devices, food processing equipment, and hot water fittings. |
Rubber | Provides excellent elasticity, impact resistance, and weatherproofing. | Common in protective coatings for tools, machinery grips, and automotive seals. |
This table illustrates the versatility and wide-ranging applications of thermoplastic coatings across different industries. By selecting the appropriate material, manufacturers can ensure their products receive the best possible protection and performance enhancement.
Thermoplastic coatings are widely used across various industries due to their unique properties and versatility. However, like any material, they come with both advantages and disadvantages. Understanding these aspects can help manufacturers and consumers make informed decisions when selecting the appropriate coating for their needs.
Advantages of Thermoplastic Coatings
- Reusability and Repairability: One of the most significant advantages of thermoplastic coatings is their ability to be reheated, reshaped, and reused without losing their properties. This characteristic makes them ideal for applications where repairability and recyclability are important, reducing waste and extending the lifespan of coated products.
- High Impact Resistance: Thermoplastic coatings are known for their exceptional toughness and ability to withstand physical impacts. This makes them particularly suitable for environments where mechanical stress is frequent, such as in automotive and industrial applications.
- Chemical and Corrosion Resistance: These coatings offer excellent resistance to a wide range of chemicals, including acids, alkalis, and solvents. This chemical resistance ensures long-term protection of substrates in harsh environments, such as chemical processing plants or marine settings.
- Flexibility and Elasticity: Thermoplastic coatings maintain flexibility even at low temperatures, reducing the risk of cracking or peeling. This property is especially beneficial for applications involving dynamic or moving parts, where coatings must adapt to changes in shape without compromising their integrity.
- Excellent Adhesion: Thermoplastic coatings adhere well to various substrates, including metals, plastics, and ceramics. This strong adhesion ensures that the coating remains intact under stress, providing long-lasting protection.
Disadvantages of Thermoplastic Coatings
- Thermal Sensitivity: While the ability to be reheated and reshaped is an advantage, it also means that thermoplastic coatings can be sensitive to high temperatures. In applications where excessive heat is present, these coatings may soften or deform, compromising their protective qualities.
- Limited UV Resistance: Some thermoplastic coatings, particularly those made from materials like polyethylene (PE), can degrade when exposed to prolonged UV radiation. This can lead to discoloration, brittleness, and a reduction in performance over time, making them less suitable for outdoor applications without UV stabilizers.
- Higher Cost Compared to Other Coatings: Depending on the specific material and application, thermoplastic coatings can be more expensive than alternative options like thermosetting coatings. The cost may include not only the material itself but also the specialized equipment and processes required for application.
- Lower Heat Resistance: While thermoplastic coatings excel in many areas, they generally have lower heat resistance compared to thermosetting coatings. This limitation can be a drawback in high-temperature applications, such as in industrial ovens or engines, where more robust coatings are required.
- Potential Environmental Concerns: The production and disposal of some thermoplastic coatings can raise environmental concerns, particularly if they are derived from non-renewable petrochemicals. Although many thermoplastics are recyclable, the environmental impact of their entire lifecycle may be greater compared to more sustainable alternatives.
Thermoplastic coatings offer a range of benefits, including reusability, impact resistance, and chemical protection, making them an excellent choice for various industrial and commercial applications. However, their thermal sensitivity, UV resistance, and cost considerations may limit their suitability for certain environments. By weighing these advantages and disadvantages, businesses can better assess whether thermoplastic coatings meet their specific needs, ensuring optimal performance and longevity for their products.
The Relationship Between Hot Melt Coatings and Thermoplastic Coatings.
Through the above content, I believe we all know the characteristics and definition of thermoplastic coatings. However, hot melt coatings and thermoplastic coatings are closely related in terms of composition and thermal behavior, which may confuse some people. Today, CoatingsDirectory will help you understand the relationship between them in an easy-to-understand way.
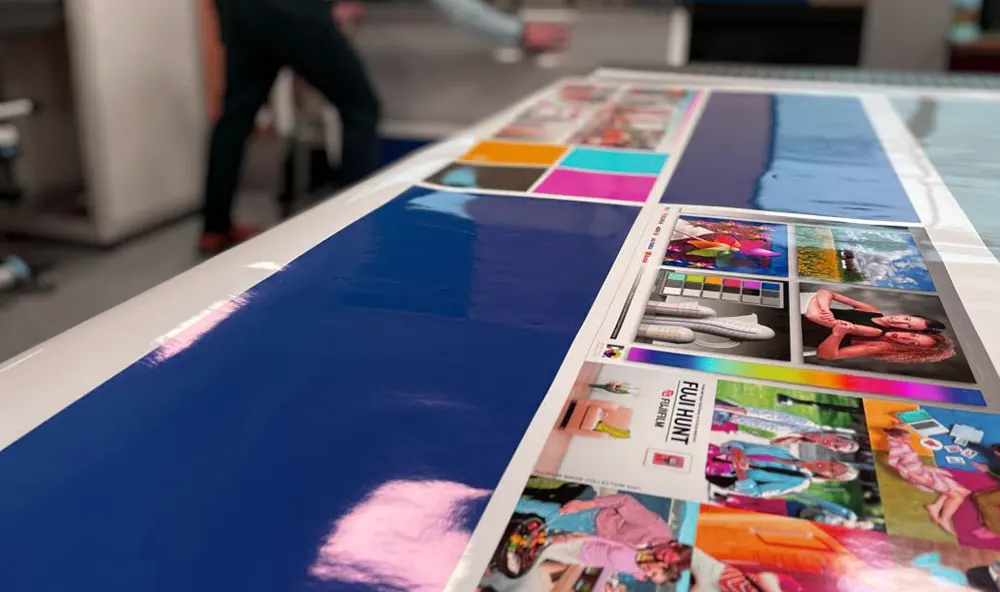
UV Hot Melt Coatings
Definition of hot melt coatings.
Hot melt coatings are a special type of thermoplastic coatings. They are solid at room temperature and become liquid when heated, so they can be used as coatings. Once applied, they quickly solidify when cooled to form a protective layer and bonding layer. This rapid cooling and solidification characteristics make hot melt coatings ideal for high-speed production environments where fast processing time is critical.
Relationship between hot melt coatings and thermoplastic coatings.
The key relationship between hot melt coatings and thermoplastic coatings lies in their common thermoplastic properties. Both coatings are based on polymers that have the ability to melt and reshape when heated.
Therefore, hot melt coatings can be regarded as a specific method and process in the field of thermoplastic coatings. All coatings used in hot melt coatings are thermoplastic. The process is widely used in industries such as packaging, textiles, and automotive manufacturing, which require strong adhesion and fast cure times.
By understanding the common thermoplastic properties of these coatings and their relationship, professionals can better evaluate which coating type is best suited to their project requirements, ensuring optimal performance and efficiency of the coating project.
What Are Thermosetting Coatings?
Thermoset coatings are protective coatings that consist of polymer strands that are highly cross-linked through strong chemical bonds. Once cured, they form a hard, inflexible protective coating that cannot be re-melted or reshaped. This irreversible transformation occurs during the curing process, where chemical reactions cause the material to cross-link, forming a strong, durable coating. These coatings are widely used in industries such as automotive, aerospace, and construction where long-term protection and resilience are critical.
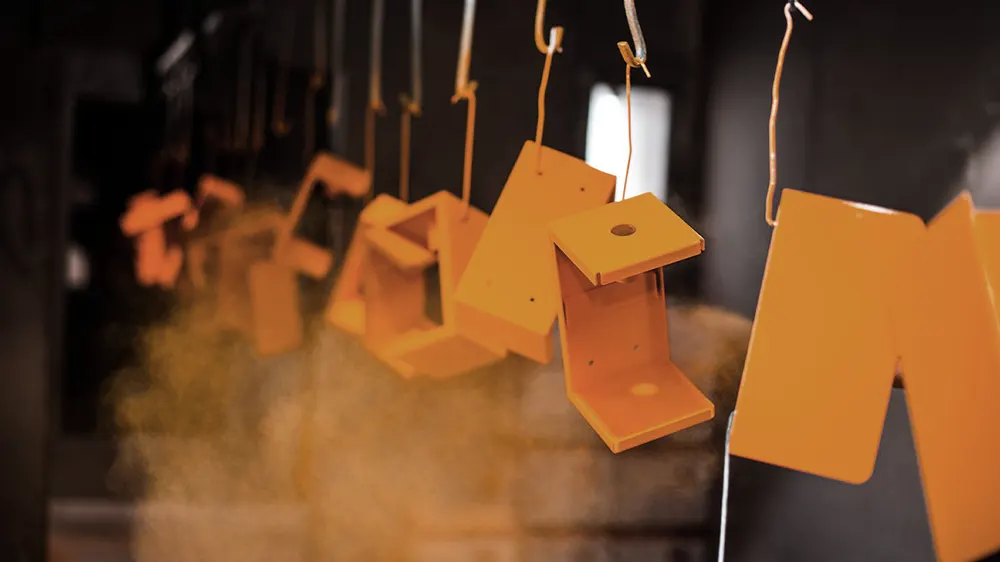
Thermosetting Powder Coating Line
One of the most notable features of thermoset coatings is their chemical resistance and structural integrity. Once cured, these coatings can withstand high temperatures, harsh chemicals, and mechanical stresses without degrading or losing their protective properties. Unlike thermoplastic coatings, which soften and reshape at high temperatures, thermoset coatings remain stable and do not melt. This makes them ideal for applications that are often exposed to extreme conditions. And thermoset coatings are more resistant to high temperatures than ordinary thermoplastics.
Thermoset coatings also have excellent adhesion to a variety of substrates, including metals, plastics, and composites. This strong adhesion, combined with the toughness of the coating, ensures long-term protection against corrosion, wear, and environmental abrasion.
Thermoset coatings are made from a variety of materials, each with specific properties that make them suitable for different applications. Below is a list of some common types of thermoset coatings and their typical applications in different industries and specific products or surfaces.
Material | Description | Application |
---|---|---|
Epoxy | Known for its exceptional adhesion, chemical resistance, and mechanical strength. | Used in industrial flooring, automotive parts, and protective coatings for pipelines and tanks. |
Polyester | Offers good weatherability, chemical resistance, and durability. | Common in outdoor furniture, automotive topcoats, and appliance finishes. |
Polyurethane | Combines flexibility with high impact resistance and chemical resistance. | Applied in coatings for wood flooring, automotive interiors, and marine environments. |
Acrylic | Provides excellent UV resistance, clarity, and color retention. | Used in automotive topcoats, outdoor signage, and architectural finishes. |
Polyester/Acrylic | Blends the durability of polyester with the UV resistance and gloss retention of acrylic. | Ideal for automotive finishes, exterior architectural coatings, and metal furniture. |
Acrylic/Epoxy | Combines the strong adhesion and chemical resistance of epoxy with the UV stability of acrylic. | Used in high-performance coatings for industrial equipment, marine applications, and concrete surfaces. |
Fluoropolymer | Known for its exceptional resistance to weathering, chemicals, and high temperatures. | Applied in high-end architectural coatings, aerospace components, and outdoor industrial equipment. |
Thermoset coatings are a key component in many industries, providing long-lasting protection and improving the performance of coated products. By understanding the properties and applications of these common thermoset materials, coating application leaders can make informed decisions to achieve the best results in specific use cases.
Thermoset coatings are widely used in various industries due to their excellent durability and longevity. However, like any material, they have both advantages and disadvantages. A full understanding of these can help everyone make an informed decision on when and where to effectively use thermoset coatings.
Advantages of Thermoset Coatings
- Exceptional Durability: One of the most significant advantages of thermoset coatings is their ability to withstand harsh environments. Once cured, these coatings form a hard, inflexible layer that resists scratching, impact, and abrasion. This makes them ideal for applications requiring long-term protection, such as in automotive and industrial equipment.
- Chemical and Corrosion Resistance: Thermoset coatings offer excellent resistance to a wide range of chemicals, including acids, solvents, and corrosive agents. This makes them particularly suitable for use in environments where exposure to such substances is frequent, such as chemical processing plants and marine environments.
- Heat Resistance: These coatings can maintain their integrity and performance at high temperatures without softening or melting. This property is crucial for applications in industries like aerospace and automotive, where components may be exposed to extreme heat.
- Strong Adhesion: Thermoset coatings adhere exceptionally well to a variety of substrates, including metals, plastics, and composites. This strong bond ensures that the coating remains intact and continues to provide protection over time, even under stressful conditions.
Disadvantages of Thermoset Coatings
- Inflexibility and Brittleness: While thermoset coatings are highly durable, their rigidity can be a drawback. They lack the flexibility of thermoplastic coatings, making them more susceptible to cracking under mechanical stress or when applied to substrates that expand and contract with temperature changes.
- Irreversible Curing Process: Once thermoset coatings are cured, they cannot be re-melted or reshaped. This means that any mistakes made during application are permanent and cannot be corrected by reheating or reforming the coating. This inflexibility can lead to increased material waste and costs if errors occur.
- Longer Curing Times: The curing process for thermoset coatings can be more time-consuming compared to other coating types. This extended curing time can slow down production processes, particularly in industries that require rapid turnaround times.
- Higher Initial Costs: The raw materials and application processes for thermoset coatings can be more expensive than those for thermoplastic coatings. This higher initial cost can be a limiting factor for some projects, especially in industries where cost efficiency is a primary concern.
Thermoset coatings provide a rugged and durable solution for many industrial applications, but their inherent limitations need to be carefully considered when using them. By weighing the pros and cons, we can determine the most appropriate applications for these coatings to ensure optimal performance and cost-effectiveness.
What Are the Main Differences Between Thermoplastic and Thermosetting Coatings?
Through the above understanding, you have learned the basics of thermoplastic coatings and thermosetting coatings in detail. Both coatings have unique properties and advantages, but their fundamental differences lie in chemical composition, curing process and performance characteristics under different conditions. In the field of protective coatings, understanding the difference between thermoplastic coatings and thermosetting coatings is essential to choosing the right material for your needs. Following the footsteps of CoatingsDirectory to understand these differences can help manufacturers and end users make informed decisions to achieve the best coating results.
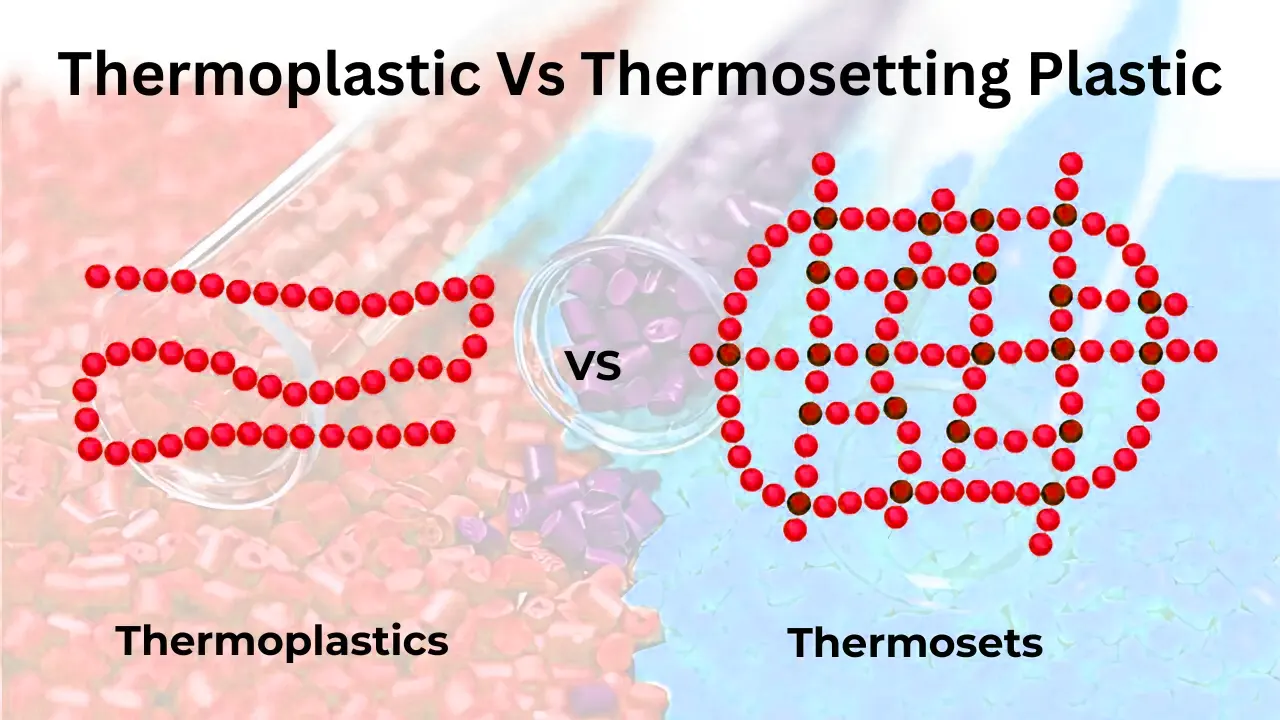
Thermoset vsThermoplastic Coatings
Drying and Curing Principles
Thermoplastic coatings are composed of polymers that do not undergo a chemical change during curing. They dry and solidify by physical means, typically through evaporation of solvents or cooling. This characteristic allows them to be re-melted and reshaped multiple times when heated, making them ideal for applications requiring repairability or flexibility.
In contrast, thermosetting coatings undergo an irreversible chemical reaction during curing, typically involving heat, UV light, or a catalyst. This cross-linking process creates a hardened, infusible network that cannot be re-melted or reformed once set. This makes thermosetting coatings highly resistant to heat and chemicals but limits their adaptability after application.
Physical and Chemical Differences
The molecular structure of thermoplastic coatings is linear or slightly branched, which grants them high flexibility, impact resistance, and the ability to soften under heat. Because of this structure, thermoplastic coatings are more susceptible to softening or deformation under high temperatures, which may be a consideration for applications exposed to intense heat.
Thermosetting coatings, on the other hand, have a three-dimensional, cross-linked molecular structure. This structure provides superior hardness, thermal stability, and chemical resistance, making them ideal for applications that require a durable and permanent finish. However, once cured, these coatings cannot be remelted or reformed, limiting their repairability.
Representative Coating Products
Thermoplastic coatings include materials like polyethylene (PE), polyvinyl chloride (PVC), and nylon, each offering unique benefits such as flexibility, impact resistance, and ease of repair. These coatings are often used in applications where flexibility, ease of application, and potential for rework are valued, such as automotive components, pipes, and protective barriers.
Thermosetting coatings, such as epoxy, polyurethane, and polyester, provide exceptional hardness, chemical resistance, and heat tolerance. They are often chosen for applications requiring a durable, long-lasting finish, such as in industrial machinery, aerospace components, and marine equipment.
Performance Under Different Conditions
When considering performance, thermoplastic coatings excel in environments where flexibility, impact resistance, and the potential for easy repair are important. They are particularly effective in applications that require regular maintenance or where components may experience repeated physical stress.
Thermosetting coatings, however, are designed for conditions where high durability, chemical resistance, and heat stability are crucial. These coatings are ideal for environments exposed to harsh chemicals, high temperatures, or mechanical wear.
Differences in Application Processes
Thermoplastic coatings are commonly applied using methods such as dipping, powder coating, and spraying. They are heated to a liquid state, applied to the substrate, and then cooled and hardened. This flexibility in the application process allows a wide range of surface finishes and thicknesses to be achieved depending on the specific requirements. Common equipment includes: fluidized bed systems, powder coating guns, and hot dip coating tanks. These methods require equipment that can precisely control the temperature, as the thermoplastic coating needs to be heated to the melting point without degrading the substrate.
However, thermosetting coatings usually require specialized equipment that can manage both the application and the subsequent curing process, such as curing ovens or UV curing systems to facilitate the crosslinking process. Common application methods include electrostatic spraying (static or airless), dip tanks, or roller coaters. Once applied, thermosetting coatings must undergo a curing process to develop their full properties. This usually involves a curing oven that can reach and maintain a precise temperature, or a UV curing system that cures the coating by irradiating it with ultraviolet light to achieve optimal properties. There, the necessary chemical crosslinking takes place to form a hard, non-melting coating. The equipment setup is usually more complex and more expensive due to the need for a curing stage, but the result is a coating that is extremely durable and resistant to environmental stresses.
When choosing between thermoplastic coatings and thermosetting coatings, it is necessary to carefully consider the differences we have listed above. Understanding these differences will not only help choose the right coating material, but also provide a reference for investing in the right application equipment and procedures. By combining the choice of coating type with specific application needs, environmental conditions and desired performance results, companies can ensure that their products receive the highest efficiency, cost-effectiveness and protection. In a rapidly evolving market, smart coating decisions can significantly affect the lifespan, safety and overall quality of the product, resulting in better value and satisfaction for manufacturers and end users.
How Do You Choose Between Thermoplastic and Thermosetting Coatings?
Understanding the differences between thermoplastic and thermosetting coatings is a crucial first step, but deciding which type to use depends on several key factors specific to your application. While both coatings offer unique benefits, selecting the most suitable one requires a careful evaluation of the conditions your product will face, the performance requirements, and the desired characteristics of the finished coating. By considering these factors, you can make a well-informed choice that aligns with your project’s goals and constraints.
Factors to consider when making your choice
- Environmental Exposure: Determine the environmental conditions the coating will be exposed to, such as temperature, UV light, chemicals, moisture, and mechanical stress. Thermoplastic coatings, which soften under high heat, might not be suitable for high-temperature applications, whereas thermosetting coatings offer better thermal and chemical resistance.
- Durability Requirements: Assess the level of durability needed for your application. If the coating must withstand harsh conditions, resist abrasion, or maintain structural integrity over a long period, thermosetting coatings may be the better choice due to their strong cross-linked structure.
- Flexibility and Impact Resistance: If flexibility and impact resistance are critical, such as in automotive or construction materials that experience constant movement or vibration, thermoplastic coatings are generally preferable because of their softer, more flexible molecular structure.
- Repair and Maintenance: Consider the ease of repair and maintenance. Thermoplastic coatings can be re-melted and reshaped, making them easier to repair or recoat compared to thermosetting coatings, which cannot be reprocessed once cured.
- Application Method and Equipment: Think about the application process and the equipment required. Thermoplastic coatings often require simpler application methods and equipment, while thermosetting coatings may need specialized equipment for precise curing.
- Cost and Economic Considerations: Evaluate the overall cost, including material costs, application costs, and potential maintenance expenses. Thermoplastic coatings might be more cost-effective for applications that don’t require the superior durability of thermosetting coatings.
Case Studies: Thermoplastic vs. Thermosetting Coatings
To illustrate how these factors play out in real-world scenarios, let’s consider two simple case studies:
- Case Study 1: Automotive Bumper Coating
An automotive manufacturer needs to choose a coating for car bumpers. The bumpers are subjected to frequent impacts and require a flexible coating that can absorb energy without cracking. They also need a coating that can be easily repaired or re-coated if damaged. Given these requirements, a thermoplastic coating such as polyethylene (PE) is a better fit. Its flexibility and impact resistance make it ideal for absorbing impacts, while its ability to be reheated and reshaped allows for easy repair and reapplication. - Case Study 2: Industrial Chemical Tank Coating
A chemical processing company needs a coating for the interior of steel tanks that will hold corrosive chemicals at high temperatures. The coating must be highly resistant to chemical attacks, have excellent adhesion to the substrate, and maintain its integrity under thermal stress. In this scenario, a thermosetting coating such as epoxy would be more suitable. Epoxy coatings provide exceptional chemical resistance, thermal stability, and a tough, durable finish that can withstand harsh conditions, making them ideal for protecting the steel surface of chemical tanks.Industrial Chemical Tank Coating
Looking at these cases, it can be seen that the choice between thermoplastic and thermoset coatings is not always simple and depends largely on the specific needs of the application. If you need flexibility, good electrical insulation, repairability, and a sustainable approach, thermoplastic coatings generally offer the best value. Conversely, for applications that require high durability, chemical resistance, thermal stability, and cost-effectiveness, thermoset coatings are generally the best choice.By carefully evaluating these factors and understanding the unique benefits and limitations of each type of coating, you can ensure that you select the most appropriate coating solution for your needs, optimizing both performance and cost-effectiveness.
By comparing the core differences between thermoplastic and thermoset coatings, you can better understand how each can meet your industrial needs. From their curing process and molecular structure to their application methods and performance characteristics, from flexibility and repairability to durability and chemical resistance, these coatings offer unique benefits that can significantly impact the success of your project. To find the right coatings product or service for your specific application, use the coatingsdirectory.com platform to connect with expert suppliers and service providers using our comprehensive search and filtering tools.
What is the cost difference between thermoplastic and thermoset coatings?
In general, most thermoplastics are generally less expensive than thermosets. This cost difference stems primarily from the tooling, materials, processes, and labor involved. Thermoset coatings require a curing process involving specialized equipment and controlled conditions, which increases their overall cost. Materials such as epoxies and polyurethanes also tend to be more expensive because of their superior durability, chemical resistance, and thermal stability.
On the other hand, thermoplastic coatings, such as polyethylene (PE) or polyvinyl chloride (PVC), are generally more affordable. They do not require the same complex curing process and are easier to apply, often resulting in lower labor costs. However, choosing these coatings should not be based solely on price. The specific application needs must also be considered, as thermoset coatings may provide longer-term value in harsher environments.
Can thermoplastic and thermosetting coatings be used together?
Yes, but with some considerations. In certain cases, thermoplastic and thermosetting coatings can be layered to combine the benefits of both types. For example, a thermosetting base coat, like epoxy, can provide a hard, durable foundation, while a thermoplastic topcoat, such as PVC, can offer additional flexibility and UV protection.
However, compatibility between the coatings is crucial. The substrate and the application method must also support both types. Additionally, differences in thermal expansion and adhesion properties between the two materials should be evaluated to ensure the coatings work well together without delamination or cracking over time.
Are there safety issues with using thermoplastic or thermoset paints?
Yes, there are some safety considerations. With thermoplastic coatings, there is a risk of inhaling fumes during application, especially when using high-heat processes to melt the material. Appropriate ventilation, personal protective equipment (PPE), and adherence to safety protocols are essential to prevent inhalation of hazardous substances.
Thermoset coatings, particularly those containing chemicals like epoxies or polyurethanes, can pose health risks if not handled properly. The curing process may release volatile organic compounds (VOCs) or other toxic substances, which can irritate the skin, eyes, or respiratory system. Proper PPE, ventilation, and safety measures are crucial for handling these coatings safely.
Always refer to the safety data sheets (SDS) for both types of coatings to understand the specific hazards and recommended safety practices before application.
Can you put duck thermoplastic roof coating on a porch?
Yes, you can use Duck Thermoplastic Roof Coating on a porch, but it’s important to consider whether it is the right choice for your specific needs. This type of coating is designed primarily for roofing applications where it provides a waterproof barrier and UV resistance. If your porch has a similar requirement — like a flat roof or a surface that needs protection from water and sun exposure — then Duck Thermoplastic Roof Coating can be an effective solution.
However, if you are looking to coat a high-traffic area, such as a porch floor, a different product may be more suitable. Thermoplastic coatings can be less durable against foot traffic and may become slippery when wet, which could pose a safety risk. Be sure to choose a coating that matches the surface requirements for optimal performance.
How do thermoplastic coatings cure?
Thermoplastic coatings do not cure in the traditional sense, but rather harden by cooling. At the time of application, these coatings are heated until they become a liquid or semi-liquid state. Thermoplastic powder coatings melt and flow into an even layer, but can be reshaped. After application, they are allowed to cool, at which point they solidify into a durable protective layer. Unlike thermoset coatings, which harden by chemical reaction, thermoplastic coatings return to a solid state after losing heat.
This unique curing process means that thermoplastic coatings can be melted and reshaped multiple times without changing their chemical structure, providing a high degree of flexibility and repairability. It also means that they require specific temperature control during application to ensure a smooth, even surface.
Where to buy thermoplastic powder coating?
You can buy thermoplastic powder coatings from a variety of suppliers, both online and in-store. Many hardware stores and paint stores carry a variety of thermoplastic coatings for different applications. For a wider selection, consider a specialty dealer or manufacturer that focuses on industrial coatings, such as PPG Industries, Sherwin-Williams, or AkzoNobel. Online platforms such as Amazon, Grainger and McMaster-Carr also offer a variety of thermoplastic powder coatings. You can also find the right thermoplastic powder coating supplier for you through the CoatingsDirectory platform.