Article Chapters
In today’s manufacturing industry, painting is one of the key steps to ensure product quality and appearance. As an efficient and accurate coating method, roller coating equipment is increasingly favored by the industry. Ever wonder how a seemingly simple machine can transform ordinary surfaces into works of art? Whether you are new to the industry or a veteran, here coatingsdirectory will take you to understand the actual operation and maintenance of roller coating machinery, combining precision with productivity to help you achieve greater success in the field of roller coating.
How Does Roller Coating Machinery Improve Productivity and Quality?
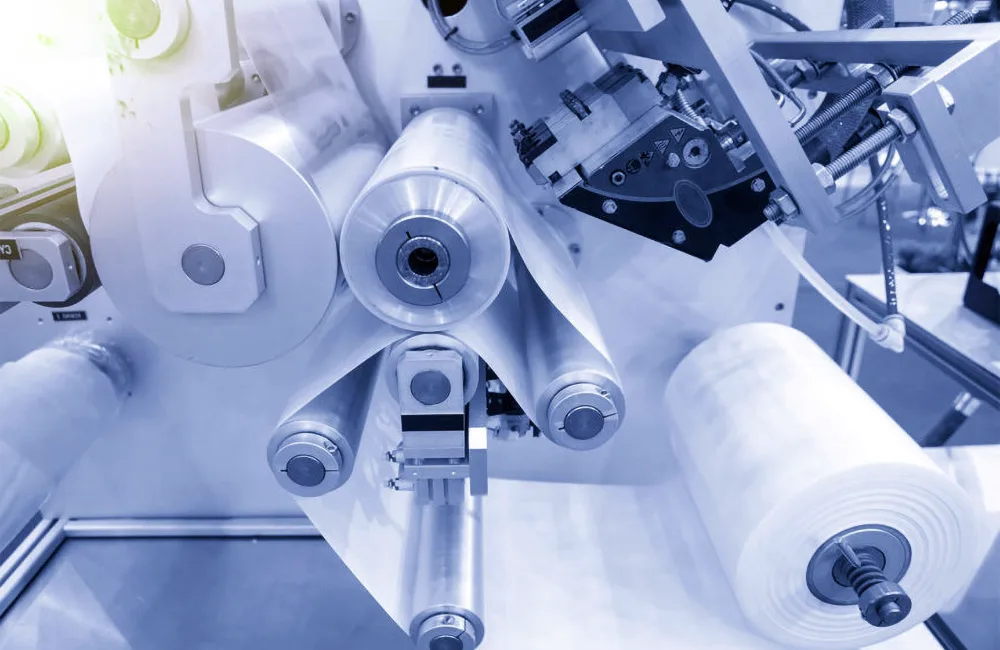
Roller Coater User Guide
Roller coating systems are mainly used to apply liquid Organic coatings. Generally speaking, roller coating equipment is used to coat relatively thin flat targets such as wood and metal. Of course, with the advancement of technology. Application goals are no longer so absolute. Wide and long substrates or non-flat objects can also be coated quickly on the roller coater. In some high-precision roller coating fields (optics, medicine, automotive, etc.), the roller coating process needs to be carried out in a clean room to prevent foreign matter from adhering to the wet surface before solidification.(Click here to read the detailed roller coating process knowledge) Next, let’s look at how roller coating machinery can improve productivity and the quality of coated products while making the entire process smooth and enjoyable.
- Maximizing Efficiency with Roller Coating Machinery:Roller coating machinery is specifically designed to coat flat surfaces with unparalleled precision and efficiency. The key to its success lies in its ability to apply coatings evenly and consistently across a wide range of substrates, from wood and metal to plastic and glass.
By utilizing a series of precisely engineered rollers, roller coating machinery ensures uniform coverage and thickness, minimizing material waste and maximizing productivity. This means fewer reworks and touch-ups, leading to faster turnaround times and increased output—a win-win situation for manufacturers and consumers alike. - Enhancing Quality Through Precision: But roller coating machinery isn’t just about speed; it’s also about quality. The controlled application of coatings results in smoother finishes, fewer defects, and enhanced durability, making the end products stand out in terms of both aesthetics and performance.
Furthermore, roller coating machinery offers unparalleled control over coating thickness and consistency, allowing manufacturers to meet even the most stringent quality standards with ease. Whether it’s achieving a flawless glossy finish or a textured matte effect, roller coating machinery delivers consistent results, time after time. - Empowering Industries Across the Board:From furniture and flooring to automotive and architectural components, roller coating machinery is the backbone of numerous industries, driving innovation and excellence every step of the way. Its ability to enhance productivity and quality has earned it a reputation as a game-changer in the world of coating technology.
In conclusion, roller coating machinery is not just a machine; it’s a catalyst for transformation, revolutionizing the way we coat and finish products. By combining precision engineering with unparalleled efficiency, roller coating machinery empowers industries to achieve new heights of productivity and quality, all while delighting consumers with impeccable finishes. Of course, in order to achieve high-quality roller coating surface effects, in addition to a reliable roller coating system, it is also inseparable from the correct installation and calibration settings of the roller coating equipment before the start of the project. Let’s read on.
How to Install and Set Up a Roller Coating System Correctly?
For some newbies who are brave enough to take up roller coating, getting started with installing and setting up a roller coating system can seem daunting, but have no fear! CoatingsDirectory will be your guiding light, guiding you through the process with expert advice and an easy-to-understand approach, ensuring your roller coating system is installed and set up seamlessly. So grab your tool kit, armed with the right knowledge and guidance below, and you’ll be on your way in no time.
- Step 1: Preparation before installation
Before starting installation, make sure you clearly understand the specifications and requirements of your roller coating system. Gather all necessary tools and equipment and select a suitable location that meets the requirements of the roller coating system. Make sure the equipment has enough space, is well ventilated, and is easy to maintain. - Step 2: Prepare the Surface
Prepare the installation area by ensuring a clean and level surface. Remove any debris or obstacles that may obstruct the installation process or interfere with the operation of the roller coating system. - Step 3: Assemble the Components
Assemble the individual components of the roller coating system, including the roller, frame, and control panel, according to the manufacturer’s instructions. Pay close attention to the alignment and connection of each component to ensure proper functionality. Get an in-depth look at several common roller coating equipment types and important components. - Step 4: Set up power and utilities
Next, connect electrical wires according to roller coating system specifications, making sure proper grounding and safety measures are in place. Verify that the power supply meets system requirements and tests the functionality of electrical connections. And ensure that the roller coating system is properly connected to other utilities such as electricity, air supply and exhaust systems. Verify that all connections are tight and meet safety standards to prevent any potential hazards during operation. - Step 5: Calibration and Adjustment
Once the roller coating system is assembled and connected, it can be calibrated and adjusted to meet your project requirements. Start by setting the roll gap and speed according to the desired coating thickness and coating speed. You can then fine-tune the settings as needed to get the best results. - Step 6: Commissioning Testing and Troubleshooting
Before using a roller coating system for actual production, conduct a thorough test run to ensure that all components are functioning properly and that the coating application meets quality standards. Testing is conducted using different coating materials and substrates to verify consistency and quality. Make necessary adjustments based on test results. - Step 7: Training and Safety Procedures
Train operators on the proper use of roller coating systems and familiarize them with safety procedures to prevent accidents and ensure efficient operations. Provide ongoing support and guidance to ensure smooth operation and maintenance of equipment. - Step 8: Ongoing maintenance and optimization
Finally, develop a routine maintenance schedule to keep your roller coating system in top condition. Regularly inspect and clean rollers, conveyor systems and other components to prevent buildup and ensure smooth operation. Continuously monitor system performance and make adjustments as needed to optimize efficiency and quality.
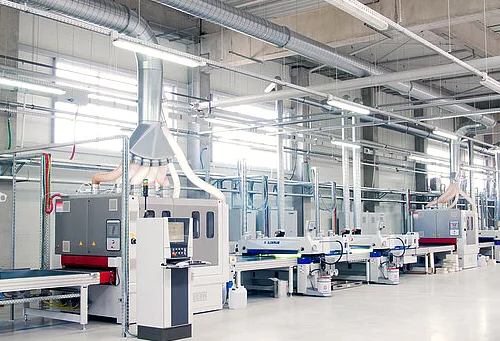
Roller coating system workshop
In summary, installing and setting up a roller coating system requires careful planning, attention to detail, and compliance with safety procedures. By following these steps and guidelines, you can ensure a smooth and successful installation process, allowing you to enjoy the benefits of an efficient, high-quality coating with a roller coating system. So weigh in and let your roller coating system take you on a journey to coating excellence!
How to Properly Calibrate Roller Coating Equipment?
Calibrating roller coating equipment is a critical aspect to ensure optimal performance and high-quality coating results. Whether you are setting up your equipment for the first time or making mid-cycle adjustments to accommodate changing coating requirements, understanding the calibration process is critical. CoatingsDirectory has previously described how to install a new roller coating system. Here we will discuss in detail the steps involved in calibrating roller coating equipment and address initial installation and mid-term modification issues.
Initial Installation Calibration | Mid-term Modification Calibration | ||
---|---|---|---|
Calibration Factors | Detailed Description | Calibration Factors | Detailed Description |
Roller Alignment | Ensure that all rollers are properly aligned and parallel to each other. Misaligned rollers can result in uneven coating thickness and poor quality finishes. | Review Process Parameters | Evaluate the performance of the roller coating equipment periodically to identify any deviations from the desired coating quality or production efficiency. |
Speed Adjustment | Calibrate the speed of the rollers according to the coating material and application requirements. Different coatings may require varying application speeds for optimal results. | Adjust Roller Speed and Pressure | Based on the specific coating requirements or changes in production conditions, recalibrate the roller speed and pressure settings to optimize coating application. |
Pressure Settings | Adjust the pressure exerted by the rollers to achieve the desired coating thickness. Too much pressure can cause excessive material buildup, while too little pressure may result in inadequate coverage. | Modify Coating Thickness | If the coating thickness needs to be adjusted due to changes in substrate material or product specifications, recalibrate the gap between the rollers accordingly. |
Coating Thickness Control | Fine-tune the gap between the rollers to control the thickness of the applied coating. This adjustment is crucial for achieving consistent and uniform coating thickness across the substrate. | Fine-tune Temperature Settings | If variations in ambient temperature or coating material properties affect the curing or drying process, adjust the temperature settings of the equipment to maintain consistent coating quality. |
Temperature Control | If applicable, calibrate the temperature settings of the roller coating equipment to ensure proper viscosity and flow of the coating material. | Conduct Test Runs | After making calibration adjustments, conduct test runs to verify the effectiveness of the modifications and ensure that the coating results meet the desired quality standards. |
Calibrating roller coating equipment is an ongoing process that requires attention to detail and a thorough understanding of the equipment’s capabilities. By following these basic steps, you can effectively adjust your roller coating equipment during initial installation and mid-term modifications, ensuring that your projects receive consistent, high-quality roller coating results.
How to Properly Maintain and Clean Roller Coating Machinery?
Maintaining the best performance of your roller coater is like breeding a precious racehorse. Only by caring for it can we go further. Attention to detail and regular care will be the secret to keeping your Roller coating machine in top condition, ensuring smooth operation and impeccable coating. Let CoatingsDirectory take you into the world of maintaining and cleaning roll coaters, where precision meets passion!
- Roller Maintenance:
Just like a well-oiled engine, the rollers of your roller coating machine require regular maintenance to keep them rolling smoothly. Inspect them for any signs of wear or damage, and clean them regularly to prevent buildup of coating material. A simple wipe-down with a mild solvent can work wonders in preserving the integrity of your rollers and ensuring consistent coating application. - Pressure Roller Care:
The pressure roller is the backbone of your roller coating system, providing the necessary force to ensure uniform coating thickness. Keep it clean and free from debris, and check for any signs of misalignment or uneven wear. Regular lubrication of the roller bearings will help maintain smooth operation and extend the lifespan of your equipment.Offset gravure roller coating machine
- Reservoirs & Fluid Pumps:
The heart of your roller coating system lies in its reservoirs and fluid pumps, which deliver the coating material to the rollers with precision. Regularly inspect these components for leaks or blockages, and clean them thoroughly to prevent contamination of the coating material. Proper calibration of the fluid pumps is essential for consistent coating application, so ensure they are adjusted correctly as part of your routine maintenance. - Slot Die Nozzles:
Slot die nozzles play a crucial role in controlling the flow of coating material onto the substrate. Inspect them regularly for any signs of clogging or damage, and clean them thoroughly using specialized cleaning solutions. Proper alignment and adjustment of the slot die nozzles are essential for achieving uniform coating thickness, so take the time to fine-tune them as needed. - Controller Calibration:
Your roller coating machine’s controller is its brain, governing the speed and pressure of the rollers with precision. Regular calibration of the controller ensures accurate coating application and prevents costly errors. Schedule periodic checks to verify the calibration settings and make adjustments as necessary to maintain optimal performance. - Doctor Blades:
Doctor blades are responsible for removing excess coating material from the rollers, ensuring a smooth and uniform coating application. Inspect them regularly for wear or damage, and replace them as needed to maintain optimal performance. Cleaning the doctor blades with a solvent and ensuring they are properly adjusted will help prevent streaks and uneven coating thickness. - Conveyor Belt Maintenance:
Last but not least, don’t forget about your roller coating machine’s conveyor belt—the unsung hero that keeps the process moving smoothly. Check for any signs of wear or damage, and clean the belt regularly to remove any buildup of coating material. Proper tensioning and alignment of the conveyor belt are essential for smooth operation, so take the time to adjust them as needed during routine maintenance.
In conclusion, proper maintenance and cleaning of your roller coating machinery are essential for ensuring consistent and high-quality coating application. By taking the time to inspect and care for each component—from the rollers to the conveyor belt—you can prolong the lifespan of your equipment and achieve superior coating results. So, roll up your sleeves and embrace the art of maintenance—it’s the key to keeping your roller coating operations running smoothly and efficiently!
How to Operate Roller Coater Safely and Effectively?
Getting started with a roll coating job requires not only technical knowledge, but also a keen sense of safety. Like a skilled captain navigating a boat in rough waters, operating a roller coater requires precision, caution, and safety first.
- Creating a Safe Operating Environment: Before diving into operation, it’s crucial to establish a safe working environment. This includes ensuring adequate ventilation to dissipate fumes, maintaining a clutter-free workspace to prevent trip hazards, and securing the machine to prevent accidental movement during operation.
- Implementing Necessary Safety Measures:Safety should never be an afterthought—it should be ingrained into every aspect of the operation. Prior to operating the roller coating machine, ensure all personnel are equipped with appropriate personal protective equipment (PPE), such as safety goggles, gloves, and aprons, to shield against potential hazards.
- Preventing Roller Coating Accidents:Accidents can often be prevented through proactive measures and careful attention to detail. Regularly inspect the roller coating machine for any signs of wear or damage, and promptly address any issues to prevent malfunctions during operation. Additionally, establish clear protocols for emergency situations, including procedures for shutting down the machine and evacuating the area in the event of an accident or malfunction.
- Maintaining Focus and Concentration:Operating a roller coating machine requires unwavering focus and concentration. Avoid distractions and refrain from multitasking while the machine is in operation. Stay vigilant and attentive to the task at hand, monitoring the coating process closely to detect any abnormalities or irregularities that may indicate potential safety hazards.
- Embracing a Safety-First Mindset: Above all, cultivating a safety-first mindset is paramount to ensuring a secure and productive work environment. Encourage open communication among team members regarding safety concerns and provide regular training and refresher courses on safe operating practices. Remember, safety is not just a priority—it’s a responsibility that we owe to ourselves and our colleagues.
In conclusion, operating a roller coating machine safely and effectively requires a combination of technical proficiency, attention to detail, and a steadfast commitment to safety. By creating a safe working environment, implementing necessary safety measures, preventing accidents through proactive measures, maintaining focus and concentration, and embracing a safety-first mindset, we can ensure a smooth and secure journey towards achieving flawless coatings. So, let’s navigate the roller coating machine with confidence, knowing that safety is our guiding star on this voyage.
Troubleshooting Common Problems with Roller Coating Equipment.
Roller coating equipment is renowned for its efficiency and precision in coating application. However, encountering problems with this equipment can disrupt production and affect product quality. In this guide, we’ll explore common issues with roller coating equipment, along with their symptoms, potential consequences, and practical solutions to keep your operations running smoothly.
Troubleshooting Roller Coating Equipment | ||
---|---|---|
Symptom | Consequences of Failure | Solutions |
Uneven Coating Thickness | Irregular coating appearance | Check roller alignment and pressure settings. Adjust substrate feeding mechanism for uniformity. |
Uneven substrate feeding | Ensure consistent roller pressure and alignment. Regularly inspect and maintain substrate feeding mechanism. | |
Worn or damaged rollers | Replace worn or damaged rollers to ensure even coating. | |
Coating Material Issues | Poor coating adhesion | This problem often occurs with over-thinned water-based coatings. Check coating material viscosity and composition. Ensure proper mixing and application parameters. |
Coating material buildup | Clean rollers and reservoirs regularly to prevent buildup. Use appropriate cleaning solvents and methods. | |
Equipment Malfunctions | Roller slippage or jamming | Lubricate rollers and inspect for obstructions. Adjust tension and alignment of roller components. |
Electrical or mechanical faults | Conduct routine maintenance and inspections. Repair or replace faulty components as needed. | |
Excessive noise or vibration | Tighten loose components and ensure proper calibration. Address underlying mechanical issues promptly. |
By addressing these common issues promptly and effectively, you can minimize downtime and maximize the efficiency of your roller coating equipment. Remember, a well-maintained system ensures consistent and high-quality coating application, keeping your operations on track and your customers satisfied.
Okay, thanks for reading this far. You’ve learned how to properly install and maintain roller coating equipment, as well as how to solve common problems. Now you can confidently apply this knowledge to improve your painting efficiency and quality. If you don’t want to implement the roller coating process yourself, you can also use the filtering function of our website coatingsdirectory.com to find roller coating service providers and factories that suit your needs. By working with a professional, you’ll have an easier time achieving your painting goals and be more successful in the industry.
Find XXX service provider
Find XXX manufacturer
How to Store Paint Roller Between Coats?
Properly storing your paint roller between coats is essential to prevent drying and maintain its effectiveness. After use, wrap the paint roller in plastic wrap or aluminum foil to seal out air and keep the roller moist. Alternatively, store the roller in a resealable plastic bag or container to prevent drying.
Do i Need to Wash Paint Roller Between Coats?
While washing the paint roller between coats is not always necessary, it depends on the type of paint being used and the desired finish. For water-based paints, rinsing the roller with water between coats can help prevent paint buildup and ensure a smoother finish. However, for oil-based paints, you may need to use paint thinner or mineral spirits to clean the roller between coats.
What is the best way to clean paint rollers?
Cleaning paint rollers effectively ensures their longevity and maintains their performance. Start by scraping off excess paint from the roller using a putty knife or scraper. Then, rinse the roller with warm, soapy water until the water runs clear. For stubborn paint residue, use a roller cleaner tool or brush to remove it. Finally, rinse the roller again and allow it to air dry thoroughly before storing or reusing.