Article Chapters
Ever wonder what gives your car that shiny exterior, or your phone that smooth, scratch-resistant finish? The answer lies in coatings, which come in a variety of ingredients and properties to help us achieve our desired effects. Coatings play an important role in a variety of industries, from protection to beautification. Let’s take a closer look at what coatings are, their basic ingredients, polymer types, and various application methods. With this information, you will have a better understanding of how to choose the coating that best suits your project needs.
What Are Coating Materials?
Coating materials are substances applied in a thin film to provide protection or decoration to a surface to enhance the properties of a substrate. They can even impart specific functionalities to the underlying substrate. From paints and varnishes to specialized polymers and metal conversion layers, coating materials come in many forms, both organic and inorganic. There are a variety of material types, each tailored for a specific application.
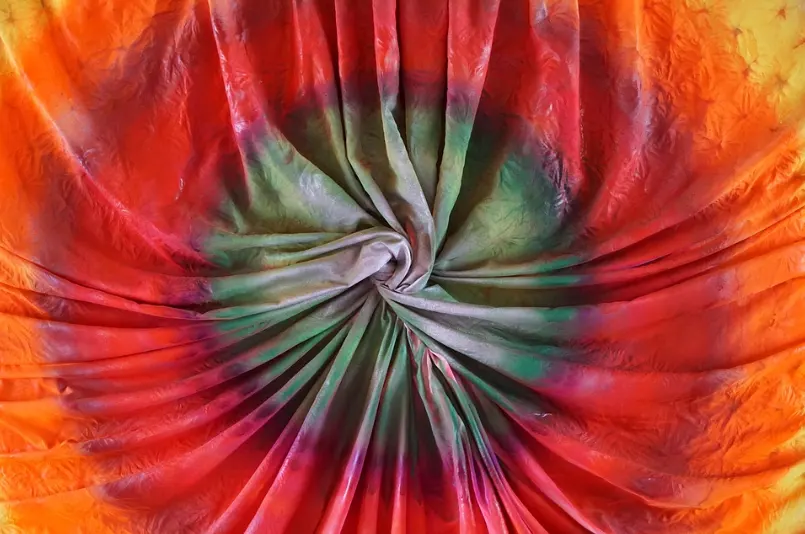
Coating Material Diversity
Coating materials are ubiquitous and play an important role in a multitude of industries. Let’s explore how these versatile materials contribute to everything from automotive to electronics.
- Automotive Industry: In the automotive sector, coating materials are essential for both beauty and protection. Think of the glossy, scratch-resistant paint on your car. Not only does it look beautiful; it also protects the metal body from corrosion and environmental damage.
- Electronics Industry: Is your smartphone screen smooth and fingerprint-resistant? That’s the result of advanced coating materials. These coatings not only improve durability, but also enhance features like anti-glare and touch sensitivity.
- Medical: In healthcare, coating materials play a vital role in ensuring the safety and effectiveness of medical devices. From antimicrobial coatings on surgical instruments to drug-eluting stents, these materials are lifesavers—literally.
- Construction: Architectural coatings protect buildings from the elements. Weather-resistant paints and coatings reflect heat or prevent moisture intrusion, extending the life of a building and improving energy efficiency.
- Industrial applications: In manufacturing, coatings improve the durability and performance of machinery and tools, reducing wear and tear and extending service life. Anti-corrosion coatings on pipes and industrial equipment are essential to maintaining operational efficiency.
- Optical industry: Coatings on lenses and optics increase light transmittance and reduce glare. Anti-reflective coatings on glasses and camera lenses are just a few examples of how these materials enhance optical properties.
- Research and development: Coating materials are used in cutting-edge research to develop new technologies and materials. For example, coatings in nanotechnology can create surfaces with unique properties, such as superhydrophobicity or enhanced electrical conductivity.
Understanding the multifaceted role of coatings helps us realize how indispensable they are. These materials do more than just cover surfaces; they transform them. Let’s take a closer look at why they are so important.
- Protection: Coatings act as a barrier to environmental factors such as UV rays, moisture and chemicals, preventing damage and extending the life of products.
- Aesthetics: They enhance the visual appeal of products, offering a range of finishes from matte to glossy.
- Functionality: Advanced coatings can add specific properties such as anti-corrosion, anti-microbial or self-cleaning features, making products more versatile and valuable.
Coatings may not always get the spotlight, but they are the unsung heroes that ensure the longevity, functionality and aesthetics of countless products we use every day. Understanding their role and importance helps us appreciate the technology and craftsmanship required to create high-quality objects that make our lives easier and more enjoyable.
What Are the Basic Ingredients of Coatings?
A coating is a fluid that forms a solid, continuous, adherent film or barrier when applied to a surface through some physical or chemical process. You may not think about the complex science behind a perfect coating. The secret lies in the basic ingredients of the coating. Whether the coating is water-based, solvent-based, high-solids or powder coating. Its formulation consists of six basic ingredients: binder, pigment, extender or filler, carrier liquid (usually organic solvent or water), rheology modifier and special additives. Let’s take a look at them one by one!
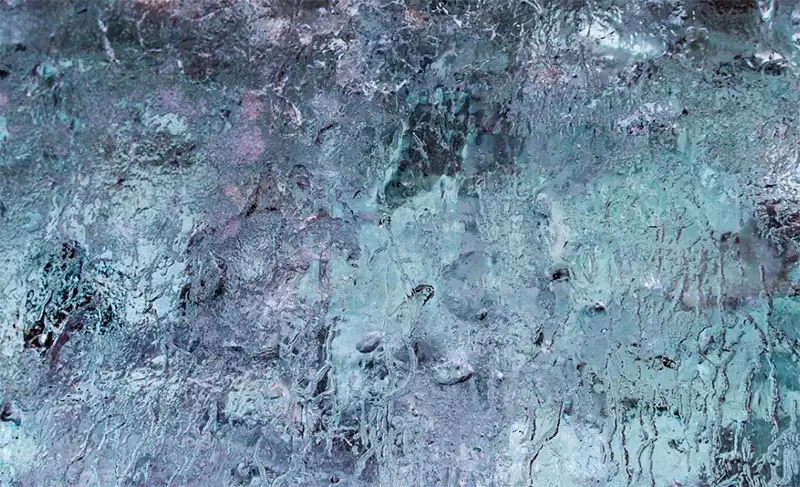
Coatings Basic Ingredients
- Fluid Carrier (Solvent or Water):
Fluid carriers are like the taxi drivers of paint. They carry all the other ingredients to the surface being painted. Solvents can be organic compounds or simply water, depending on whether the paint is solvent-based or water-based. Their main role is to adjust the viscosity of the paint, making it easy to apply. After application, the fluid carrier evaporates, leaving a smooth solid layer. The choice between solvent and water affects drying time, odor and environmental impact. - Pigments:
Pigments are the artists in paint formulations. They provide color, opacity and even protection. There are two main types of pigments: organic pigments, which provide bright, vivid hues, and inorganic pigments, which are known for their durability and UV resistance. In addition to aesthetics, pigments can also provide functional benefits such as corrosion and UV protection, ensuring that the coating not only looks good, but also performs well in harsh conditions. - Binders (Polymers):
Binders are the glue that holds everything together, providing coatings with their basic universal properties. They form a film that adheres to the substrate and encapsulates the pigments and other additives. Depending on how they form a film, they are classified as either thermoplastic or thermosetting. Common types of binders include acrylics, polyurethanes, and epoxies, among others. These polymers determine the durability, flexibility, and resistance to environmental factors of the coating. Think of them as the backbone of the coating, providing structure and strength. - Additives (Extenders or Fillers):
Additives, especially extenders or fillers, are the unsung heroes that improve the performance and cost-effectiveness of coatings. They serve as the secret weapon for fine-tuning the properties of the coating. Extenders are usually inert materials such as calcium carbonate or silica that improve the mechanical properties of the coating, such as hardness and wear resistance. Fillers improve the texture of a coating and fill minor surface imperfections, and can also help reduce the overall cost of a coating by replacing more expensive ingredients without compromising quality. - Rheology Modifiers:
Rheology modifiers are the conductors of the coating symphony, controlling flow and application properties. These ingredients ensure that the coating is evenly distributed and maintains the desired thickness. They prevent sagging on vertical surfaces and ensure a smooth, uniform surface. Types of rheology modifiers include cellulose derivatives and fumed silica, each bringing unique properties to the mix. - Miscellaneous Additives:
Miscellaneous additives, often referred to as specialty additives, bring additional properties to a coating, making it more versatile. This category includes additives such as defoamers to prevent bubbles, UV stabilizers to prevent sunlight degradation, brighteners to enhance gloss and visual appeal, stabilizers to extend shelf life and adhesion promoters to improve bonding to the substrate. Each additive has a specialized role, and each specialty additive is like a pinch of spice in a formulation, tailored to specific performance requirements to enhance specific properties of the coating, ensuring it meets the desired performance standards.
Understanding the basic components of paint reveals the complexity and precision behind every brush and spray application. Fluid carriers, pigments, binders, additives, rheology modifiers, and other specialized ingredients all play a vital role in creating a high-quality, durable, and beautiful finish.
What Are the Types of Coating Polymer Material?
Polymers (binders) are the magicians of coatings, using unique properties to transform surfaces. Whether providing durability, flexibility or resistance, coating polymer materials are indispensable in various industries. Generally, polymers are divided into two types based on the film-forming method: thermoplastic binders and thermosetting binders. Different application requirements and intended functions determine the film-forming method that should be selected.
- Thermoplastic Polymers:These polymers soften when heated and harden when cooled. They can be reshaped many times, so they are widely used. Examples include latex, polyethylene and polyvinyl chloride (PVC).
- Thermosetting Polymers:These polymers undergo chemical changes when heated to form rigid structures that cannot be reshaped. Once solidified, they retain their shape and properties permanently. Examples include epoxy resins, phenolic resins and polyester resins.
Now that you know how polymers form films, follow CoatingsDirectory to see what are the common natural and synthetic binder substances in the coatings industry.
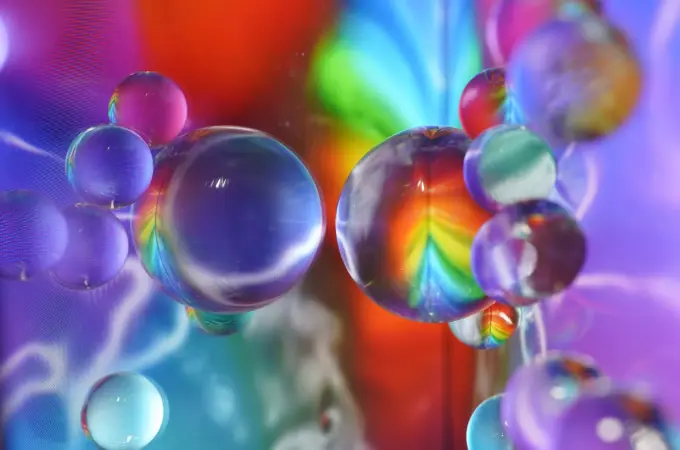
Coating polymer types
Natural Resins:
- Rubber: Known for its excellent elasticity and waterproof properties, rubber coatings are ideal for protective applications in harsh environments.
- Linseed Oil: Derived from flax seeds, linseed oil is a traditional polymer used in wood finishing, providing a natural and durable finish.
- Tung Oil: This oil penetrates deeply into wood, creating a hard and water-resistant finish. It’s a favorite among woodworkers.
- Safflower Oil: Similar to linseed oil, it’s used in coatings for its non-yellowing properties, ideal for preserving light-colored woods.
- Walnut Oil: Valued for its rich, deep finish on wooden surfaces, walnut oil also offers protective benefits.
- Fish Oil: Historically used in marine coatings for its water-repellent properties, fish oil is still found in some traditional coating applications.
Synthetic Resins:
- Alkyd Resins: These are widely used in paints and coatings for their excellent durability and glossy finish. They are often modified with natural oils.
- Epoxy Resins: Known for their exceptional adhesive strength and chemical resistance, epoxies are used in industrial and protective coatings.
- Phenolic Resins: These provide superior hardness and heat resistance, making them suitable for high-temperature applications.
- Latex: As a water-based polymer, latex is popular in household paints for its easy application and quick drying properties.
- Silicone: Silicone coatings offer outstanding temperature stability and water resistance, ideal for automotive and electronic applications.
- Polyester: These resins are used in powder coatings for their durability, UV resistance, and high gloss finishes.
- Polyurethane: Known for their flexibility and abrasion resistance, polyurethane coatings are used in a variety of protective and decorative applications.
- Silicone: Silicone resins provide excellent heat resistance and flexibility, used in applications ranging from bakeware coatings to high-temperature industrial uses.
- Acrylic: Acrylic polymers are prized for their clarity, UV resistance, and weatherability, commonly used in outdoor coatings and automotive finishes.
- Vinyl (PVC): PVC coatings offer excellent chemical and abrasion resistance, making them suitable for flooring and protective applications.
- Polyolefins: This group includes polyethylene and polypropylene, known for their chemical resistance and flexibility, used in industrial coatings.
- Silicone Resins: Providing exceptional heat and weather resistance, silicone resins are used in coatings for high-temperature environments.
- Enamels: Enamel coatings, typically made from alkyd or acrylic resins, offer a hard, glossy finish suitable for appliances and metal surfaces.
- Powder Coatings: These are dry powder polymers like polyester or epoxy that are electrostatically applied and cured under heat, providing a tough, durable finish.
- Plastic Sols: These are suspensions of PVC or other polymers used in dip coatings for their flexibility and resistance to wear.
- Amino Resins: Often used in combination with other resins, amino resins (like melamine and urea) provide hard, durable finishes.
- Fluoropolymers (PTFE): Known for their non-stick properties and chemical resistance, PTFE coatings are used in cookware and industrial applications.
- Polyamide (PA): Also known as nylon, polyamide coatings offer excellent abrasion resistance and mechanical strength, making them suitable for industrial applications.
- Polyether: Known for their flexibility and low-temperature performance, polyethers are used in coatings for their resistance to hydrolysis and excellent mechanical properties.
- Polycarbonate (PC): These coatings provide high impact resistance and optical clarity, commonly used in automotive and electronic applications.
- Polyurea: Known for their rapid curing and extreme durability, polyurea coatings are ideal for waterproofing and protective applications in harsh environments.
- Polyvinylidene Fluoride (PVDF): PVDF coatings offer exceptional chemical resistance and UV stability, making them suitable for outdoor and architectural applications.
- Phenolic Plastics: These provide excellent heat resistance and mechanical strength, used in applications requiring high durability.
- Polylactic Acid (PLA): A biodegradable polymer derived from renewable resources, PLA is used in environmentally friendly coatings.
- Polyvinylidene Chloride (PVDC): Known for its excellent barrier properties against moisture and gases, PVDC is used in food packaging and protective coatings.
- Polystyrene (PS): PS coatings offer good clarity and rigidity, used in various applications from protective packaging to insulation.
Polymer Name | Natural or Synthetic | Film Formation | Characteristics | Applications |
---|---|---|---|---|
Rubber | Natural | Thermoplastic | Elasticity, Waterproof | Protective Applications |
Linseed Oil | Natural | Thermoplastic | Durable, Natural Finish | Wood Finishing |
Tung Oil | Natural | Thermoplastic | Hard, Water-resistant | Woodworking |
Safflower Oil | Natural | Thermoplastic | Non-yellowing | Light-colored Woods |
Walnut Oil | Natural | Thermoplastic | Rich Finish | Wooden Surfaces |
Fish Oil | Natural | Thermoplastic | Water-repellent | Marine Coatings |
Alkyd Resins | Synthetic | Thermosetting | Durable, Glossy Finish | Paints, Coatings |
Epoxy Resins | Synthetic | Thermosetting | Adhesive Strength, Chemical Resistance | Industrial, Protective Coatings |
Phenolic Resins | Synthetic | Thermosetting | Hardness, Heat Resistance | High-temperature Applications |
Latex | Synthetic | Thermoplastic | Easy Application, Quick Drying | Household Paints |
Silicone | Synthetic | Thermosetting | Temperature Stability, Water Resistance | Automotive, Electronics |
Polyester | Synthetic | Thermosetting | Durable, UV Resistance, High Gloss | Powder Coatings |
Polyurethane | Synthetic | Thermoplastic | Flexibility, Abrasion Resistance | Protective, Decorative Applications |
Acrylic | Synthetic | Thermoplastic | Clarity, UV Resistance, Weatherability | Outdoor, Automotive |
Vinyl (PVC) | Synthetic | Thermoplastic | Chemical Resistance, Abrasion Resistance | Flooring, Protective Applications |
Polyolefins | Synthetic | Thermoplastic | Chemical Resistance, Flexibility | Industrial Coatings |
Silicone Resins | Synthetic | Thermosetting | Heat and Weather Resistance | High-temperature Environments |
Enamels | Synthetic | Thermoplastic | Hard, Glossy Finish | Appliances, Metal Surfaces |
Powder Coatings | Synthetic | Thermoplastic | Tough, Durable Finish | Various Applications |
Plastic Sols | Synthetic | Thermoplastic | Flexibility, Wear Resistance | Dip Coatings |
Amino Resins | Synthetic | Thermosetting | Hard, Durable Finish | Hard Finishes |
Fluoropolymers (PTFE) | Synthetic | Thermoplastic | Non-stick, Chemical Resistance | Cookware, Industrial |
Polyamide (PA) | Synthetic | Thermoplastic | Abrasion Resistance, Mechanical Strength | Industrial Applications |
Polyether | Synthetic | Thermoplastic | Flexibility, Low-temperature Performance | Coatings |
Polycarbonate (PC) | Synthetic | Thermoplastic | Impact Resistance, Optical Clarity | Automotive, Electronics |
Polyurea | Synthetic | Thermosetting | Rapid Curing, Durability | Waterproofing, Protective Applications |
Polyvinylidene Fluoride (PVDF) | Synthetic | Thermoplastic | Chemical Resistance, UV Stability | Outdoor, Architectural |
Phenolic Plastics | Synthetic | Thermosetting | Heat Resistance, Mechanical Strength | High Durability Applications |
Polylactic Acid (PLA) | Synthetic | Thermoplastic | Biodegradable, Renewable | Environmentally Friendly Coatings |
Polyvinylidene Chloride (PVDC) | Synthetic | Thermoplastic | Barrier Properties | Food Packaging, Protective Coatings |
Polystyrene (PS) | Synthetic | Thermoplastic | Clarity, Rigidity | Protective Packaging, Insulation |
Coating polymer materials are the backbone of many industrial and consumer applications, providing essential protective and decorative properties. Whether natural or synthetic, each type of polymer offers unique advantages. Understanding these materials can help you choose the right coating to ensure optimal performance and longevity. For more detailed information on common coating polymers, please visit our corresponding blog.
What Are the Common Application Methods of Coatings?
Applying coatings is an essential step in many industries to ensure products are protected, functional, and aesthetically pleasing. There are many different ways to apply coatings, each with its own advantages and limitations. Let’s explore these common coating methods: brushing, spraying, roller coating, dipping, spin coating, flow coating, and electrophoretic deposition, and learn what makes each method unique.
Brush Coating:
Brush coating involves applying the coating material using a brush, making it a simple and straightforward method.
- Advantages: Ideal for small areas and detailed work, offering precise control over the application. It’s cost-effective and requires minimal equipment.
- Limitations: Time-consuming for large surfaces and may result in brush marks if not done carefully. It requires skilled application to achieve a uniform finish.
Spray coating uses a spray gun to apply the coating material in a fine mist, covering surfaces quickly and evenly.
- Advantages: Fast application with a smooth, even finish. It’s suitable for large surfaces and complex shapes.
- Limitations: Requires proper ventilation and protective equipment due to overspray and fumes. It can be wasteful if not done efficiently and needs skilled operation to avoid defects.
Roller Coating:
Roller coating uses a roller to apply the coating, commonly used for flat and large surfaces.
- Advantages: Efficient for large, flat surfaces, providing a consistent finish. It’s faster than brush coating and relatively easy to master.
- Limitations: Not suitable for intricate details or uneven surfaces. Can leave roller marks if not applied evenly.
Dip coating involves immersing the object into a tank of coating material and then withdrawing it, allowing excess coating to drain off.
- Advantages: Provides a uniform coating, especially for complex shapes and hard-to-reach areas. It’s efficient for mass production and ensures consistent thickness.
- Limitations: Limited to items that can be fully immersed. The initial setup cost can be high, and it requires careful control of the dipping process to avoid defects.
Spin Coating:
Spin coating is used primarily for applying thin, uniform coatings to flat substrates by spinning the substrate at high speeds.
- Advantages: Produces extremely uniform and thin films, ideal for applications in electronics and nanotechnology. It’s fast and allows precise control over film thickness.
- Limitations: Limited to flat and small substrates. The process can be wasteful as excess material is spun off and lost.
Flow Coating:
Flow coating involves pouring or flowing the coating material over the substrate and then allowing excess material to drain off.
- Advantages: Suitable for large or complex-shaped objects, providing a smooth, even coating. It’s efficient for batch processing and can handle a variety of coating materials.
- Limitations: Requires careful control of the flow rate and material viscosity to avoid drips and runs. It can be messy and may require additional cleanup.
Electrophoretic Coating (E-Coating):
E-coating uses electrical current to deposit the coating material onto the surface, commonly used in the automotive industry.
- Advantages: Ensures a uniform, high-quality finish with excellent adhesion and corrosion resistance. It’s highly efficient and suitable for large-scale production.
- Limitations: Requires specialized equipment and setup, making it costly. It’s limited to conductive materials.
Powder Coating:
Powder coating involves applying a dry powder to the surface, which is then cured under heat to form a solid layer.
- Advantages: Provides a durable, high-quality finish with excellent resistance to wear and corrosion. It’s environmentally friendly, with minimal waste.
- Limitations: Requires curing ovens and precise control over application. It’s not suitable for items that can’t withstand high temperatures.
Each coating application method has its unique benefits and challenges, making them suitable for different applications and industries. Understanding these methods helps in selecting the right technique for your specific needs, ensuring optimal results.
For a deeper dive into these methods and to find the perfect coating application for your project, check out our detailed “Coating Application Method Guide.” Whether you’re a seasoned professional or new to the world of coatings, our guide offers comprehensive insights to help you achieve the best results.
How to Choose the Right Coating Material for Your Project?
Choosing the right coating material for your project is like selecting the perfect outfit for a special occasion. It needs to look good, fit well, and perform its function. In the world of coatings, the stakes are high—choosing the wrong material can lead to premature failure, increased costs, and poor performance. So how do you make an informed decision and select the ideal coating material for your needs? We share some essential factors to consider when choosing a coating material:
- Substrate Type:
The first step is to understand what you’re coating. Different substrates (metal, plastic, wood, etc.) interact differently with coating materials. For example, a metal surface may require an anti-corrosion coating, while wood may require a material that will protect against moisture and UV rays. - Environmental Conditions:
Consider the environment in which the coated product will be used. Will it be exposed to harsh weather, chemicals, or high temperatures? For outdoor applications, a weather-resistant coating is essential. In industrial settings, a coating that is resistant to chemicals and abrasion is essential. - Required Properties:
What do you need your coating to do? Look good, protect, or both? For a smooth finish on consumer electronics, choose a durable, scratch-resistant material. For pipes, an anti-corrosion and durable coating is essential. - Application methods:
Some coatings require specific application methods. For example, powder coatings require electrostatic application and cure in an oven. Make sure the coating material is compatible with your application equipment and process. - Durability and maintenance:
Consider the coating’s lifespan and maintenance requirements. Low-maintenance coatings with a long lifespan may cost more upfront but save money in the long run. Epoxy coatings, for example, are known for their durability and low maintenance. - Regulatory and safety requirements:
It is critical to comply with industry standards and safety regulations. Make sure the coating material meets all relevant safety and environmental regulations. For medical devices, biocompatibility is a key consideration.
Choosing the right coating material is a combination of science and strategy. By considering factors such as substrate type, environmental conditions, desired properties, application method, durability, and regulatory requirements, you can make the right decision for your project. If you are still confused or have been struggling with multiple coating materials. The following tips hope to help you make an informed choice:
- Consult an Expert:When in doubt, consult a coating expert or material scientist. Their expertise can provide insights that may not be immediately apparent and can help you make a choice based on your specific needs.
- Test Samples:Before you commit, test different coating materials on small samples of your substrate. This hands-on approach can reveal how each material performs under real-world conditions.
- Consider Future Needs:Consider the future needs of your project. Will the coated product need to be updated or repainted? Choose a material that provides flexibility for future modifications.
- Cost vs. Benefit Analysis:While budget constraints are important, consider the long-term benefits and savings that a high-quality coating material can provide. Sometimes a higher initial investment can pay off through reduced maintenance and longer service life.
- Read Case Studies and Reviews:Find case studies and reviews of similar projects. Learning from the experiences of others can provide valuable insights and help avoid potential pitfalls.
Remember that the right coating material can not only improve the performance and life of your product, but can also add an extra touch of excellence. Happy painting!
Through this article, you have learned about the basic composition of coatings, different types of polymers, and common application methods. And provide guidance on choosing the right coating for your project. Of course, with the advancement of technology and people’s awareness of green ecology. The development of coatings will continue to be updated and upgraded in the future. Let us look forward to coatings bringing more functions to our world.
To better meet your coating needs, welcome to use coatingsdirectory.com’s powerful filtering tools to quickly find coating engineers, service providers, local coating companies and construction teams to provide professional support for your project.
Is coating the same as paint?
Not exactly, but they’re closely related! While all paints are coatings, not all coatings are paints. Paints are designed primarily for color and basic protection, consisting of pigments, binders, solvents, and additives. Coatings, however, include a wider range of materials that provide specific protective or functional properties, such as anti-corrosion, waterproofing, or heat resistance.
Which coating material is best?
It depends on your project needs! There is no best, only the most suitable. The best coating material varies based on the application. For example, epoxy coatings offer excellent durability and chemical resistance, making them ideal for industrial use. Polyurethane coatings provide a glossy finish and UV protection, perfect for automotive and outdoor applications. Assess your specific requirements—such as environmental exposure, desired finish, and substrate material—to determine the optimal coating.
What are the chemical properties of coating?
Coatings have various chemical properties tailored to their specific functions. They are formulated to exhibit specific characteristics, such as adhesion, corrosion resistance, chemical resistance, and flexibility. These properties are achieved through the careful selection of resins, additives, and curing agents. For instance, anti-corrosive coatings contain inhibitors that prevent rust, while UV-resistant coatings include stabilizers that protect against sun damage.
What are the 4 types of polymers?
The four main types of polymers are elastomers, fibers, thermoplastics, and thermoset polymers.
- Elastomers are rubbery and highly stretchable, perfect for products like seals and gaskets.
- Fibers are strong and durable, used in textiles and industrial fabrics.
- Thermoplastics soften with heat and can be reshaped, making them ideal for packaging and automotive parts.
- Thermoset Polymers harden permanently after curing, great for adhesives and electrical insulation. Each type has unique properties suited to different applications.
What is the key to coating effectiveness?
Proper preparation and application are critical, and the performance of a coating is largely affected by its ability to adhere properly to the substrate! The effectiveness of a coating depends on thorough surface preparation, correct application techniques, and suitable environmental conditions during curing. Clean and prime to ensure good adhesion. Follow the manufacturer’s application guidelines, including temperature and humidity control. Proper curing allows the coating to achieve its full protective and functional properties. Remember, a well-applied coating is a satisfactory coating!